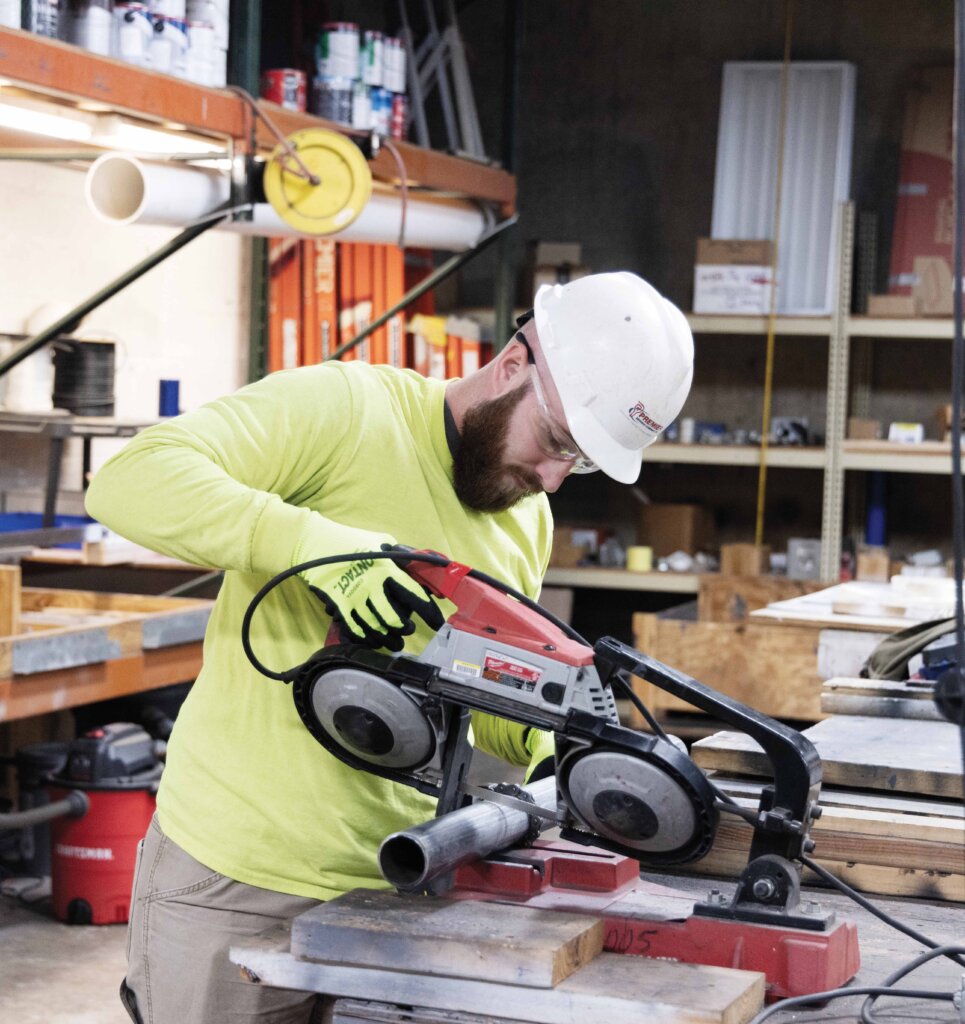
Byron Horst got a job at Premier Service Co. about three-and-a-half years ago, but he knew he had a lot to learn.
“I was about as green as you could be,” he says. “I was getting on-the-job training, but I needed more.”
So, a few months into his job, he joined Premier’s apprenticeship program, which allowed him to stay on the job while at the same time going to classes a couple of nights a week to learn what he needed for his journeyman electrician’s exam.
And it’s worked. Within six months, he’ll have the on-the-job hours — 8,000 of them — needed to get his certification and take the journeyman’s exam, and he’s been studying for it along the way.
That’s exactly the goal of Skilled Trades of West Alabama, which sprung out of the apprenticeship program that Gary Phillips developed at Premier, where he’s president. Only a year old, the program geared toward construction trades — electrical, HVAC, plumbing and alarms — already has 73 apprentices working for 16 different companies in Tuscaloosa County.
“I believe that training and apprenticeship programs are what works,” Phillips says. “I’m a supporter of Shelton State and what they and other schools do, too, but I just think that working eight hours a day, five days a week, and going to school one or two nights a week is the way things ought to be.… The on-the-job training is a better learning experience for the employee and the apprentice.”
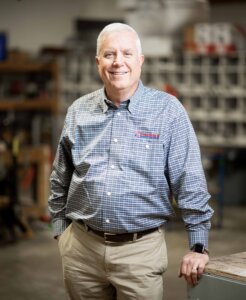
FILLING THE CONSTRUCTION PIPELINE
This is not a new need, says Johnnie Aycock, Skilled Trades’ director of development.
Aycock, who spent 30 years as CEO of the Chamber of Commerce of West Alabama, has almost 50 years of experience surrounding workforce development.
“There has always been a challenge in workforce development for as long as I can remember,” he says. “The whole idea of whether a student should or shouldn’t go to college — should they get a skill, or should they get a technical background? That’s been going on for a long, long time. It’s not really new.”
Things have been improving in Alabama, though, Aycock says.
“There’s always been a disconnect between education and industry in terms of needs and demands and how to fill them, and I think that has improved over the past several years,” he says. “Alabama can take some credit in trying to consolidate their efforts and have more of a common purpose and common effort. That has been a real positive, in terms of the way regional economic councils are organized and in terms of priorities at the highest level, including the governor and the legislature.”
But attention often is diverted from the construction industry.
Aycock recalls that when Mercedes set up shop in Tuscaloosa County, “all the existing industries started screaming bloody murder.”
“’You’re taking our workforce,’ they said,” Aycock recalls. “Where’s the pipeline to replace those skilled, experienced people we’re going to lose? That was an awakening, at least in our part of the state.”
Along the way, Aycock started noticing that attention toward building a skilled workforce was especially necessary for the construction industry.
“There’s always been a demand, but the supply has not always been there in terms of skilled trades that apply directly to the construction sector,” he says. “Manufacturing, automotive, aerospace all get the attention, and that’s where the jobs seem to be growing. As I remind folks, somebody’s got to build that infrastructure, and in our case, the construction industry has often been overlooked. That’s true in Tuscaloosa, but we could go to Huntsville, Mobile, Montgomery, and probably the same conversation can be had.”
QUICK SUCCESS FOR SKILLED TRADES
Aycock was doing some consulting work when Phillips, an old friend, called and asked him to do some work for Skilled Trades.
It kicked off in January 2021 and has seen “amazing” success in just a year.
Why? Aycock says there are a couple of reasons.
“Number one, it’s employer-based,” he says. “A lot of workforce development programs connect with employers, but they’re not led by employers. Secondly, it has a tight focus on the construction industry. We’re a business employer-directed organization focused on one thing — building a pipeline of skilled tradespeople for the construction industry. That’s all we do, and we don’t try to get outside of that.
“We are very focused,” Aycock adds. “And I think we hit a nerve. I think there was a need and a demand, and I think we’re filling it.”
That doesn’t mean that Skilled Trades isn’t planning to grow.
It already has, with the addition of a program it calls JumpStart.
“I think this is going to be our biggest success,” Phillips says of the program designed to be a feeder program into the apprenticeship program. “We take someone who doesn’t know anything about the trades and take them through a 14-week, one night a week class,” he says. “They obtain an OSHA 10 card and other safety credentials required by the industry. Then they’re hired by one of our contractors. We give them a full set of tools and a hardhat so they’re ready to go to work.”
Many of the JumpStart participants — and right now there are more than 120 of them — will then go through the full apprenticeship program.
“The idea was that if they could complete that 14 weeks, at the end of that time, they’d be more employable, then we move them into the apprenticeship program,” Aycock says. “We’re filling the pipeline for the construction employers and also giving the individual a path toward a more fulfilling career and higher-paying career.”
Skilled Trades will soon expand to the eight counties around Tuscaloosa, and other trade programs are on their way.
“We hope to start a carpenters program and then one in the landscaping industry,” Phillips says. “But they’ll all be related to construction.”
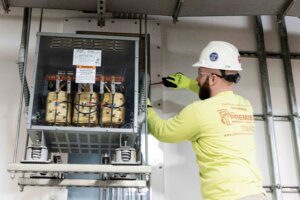
A MODEL FOR THE STATE
Primary funding for Skilled Trades comes from the construction industry.
“The Alabama Construction Industry Craft Training Board receives funding from a percentage of permitting and license fees that contractors have to pay,” Aycock says. “That goes into a fund, and that fund is then used for construction-based training only.”
Phillips is confident the Skilled Trades of West Alabama model could work anywhere.
“We hope we’re building a model program for the state,” he says. “We want to be the model that others follow, and we’re willing to help anyone who wants to do this.”
Skilled Trades is successful and will continue to be successful because it’s different from other programs out there, Aycock says.
“There are some similar programs like us, but we’ve got so much uniqueness about us — our core, our belief system, the vision behind it,” he says. “And we are the only pre-apprenticeship construction program in Alabama and one of the very few apprenticeship programs in all of the trades.”
Alec Harvey is executive editor and Cary Norton is a freelance contributor to Business Alabama. Both are based in Birmingham.