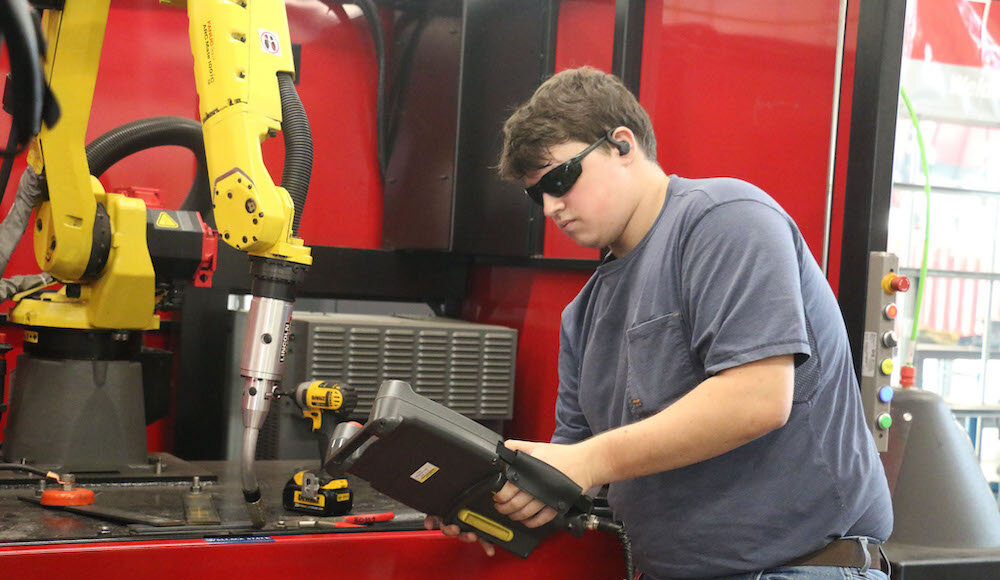
Welders make good money, and just a glance at job postings shows they have no trouble finding work. Now a new multi-million-dollar training facility at a north Alabama community college ensures they’ll have the latest welding skills — including operating robots.
The $8.8 million, 30,000-square-foot Welding Technology and Innovation Center opened Aug. 21 at Wallace State Community College in Hanceville, with college officials describing it as the largest training center in the Southeast.
“The new welding facility allows us to impact more lives by providing more opportunities for students to receive training that leads to high-demand, high-wage jobs,” says college President Dr. Vicki Karolewics.
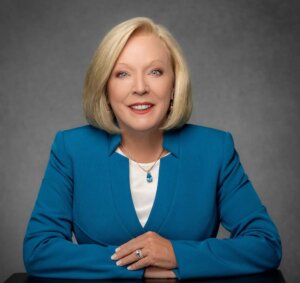
The welding area includes 20 grinding booths, a fabrication area with two welders, pipe-welding equipment and three classrooms with built-in cameras, microphones and speakers for online classes.
Students had asked for training in robotics and more room to learn fabrication methods, college officials say.
“We needed a larger training center to allow more students to attend and to have the ability to offer more specific types of training that we did not have the room to do before,” says Randy Hammond, Wallace State welding department chair and instructor.
“We are now the only college in the state to offer an associate degree in robotic welding technician,” Hammond says.
The program also offers various welding certificates and has three American Welding Society-certified inspectors on staff at its campuses in Hanceville and Oneonta.
The up-to-date technology will better prepare students to enter the Alabama workforce. They are learning the four main arc welding processes: shielded metal, gas metal, flux cored and gas tungsten.
Instructors also explain how to cut and bevel metal with various processes, such as oxy-fuel with acetylene and alternative fuels, plasma arc cutting, and carbon arc cutting and gouging. Students learn how to read and interpret fabrication prints and weld symbols. By learning blueprint reading, they can put the knowledge into action by fabricating parts.
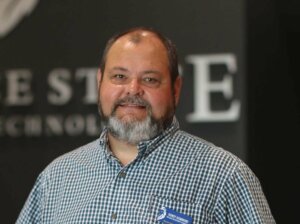
Classes also teach principles of weld inspection and testing in both destructive and non-destructive testing methods, as well as theories of working with AC and DC currents.
In the robotic welding classes, Hammond says, students learn to work safely around robotic equipment and how to program and edit commands to create a program that will weld out assembly parts.
The center has 85 manual welding stations and four robotic welding cells, with three more scheduled for purchase this year. Students learn how to work with sensors, programmable logic controls and motor controls within a robotic welding cell.
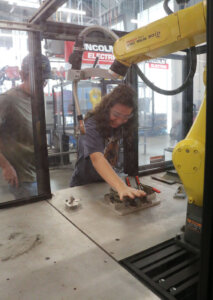
For the fall semester, 99 students enrolled in the program. All welding students must pass two American Welding Society welding certification tests before graduating.
Then they walk right into a job.
“We have a 100% job placement with all graduates of the welding program,” Hammond says.
“We have numerous companies that come monthly and speak to our students about what they build or produce and the benefits that they have to offer employees,” he says. “Many of our students are working in internship programs with companies while they are here in classes.”
The college received several grants for the center, including $2 million from the U.S. Economic Development Administration and $200,000 from the Appalachian Regional Commission. The program is expected to provide an estimated 110 workers yearly in the Southern Appalachian region to supply the roughly 40 new and current manufacturing businesses there. That approximate payroll for the next eight years is projected at $25 million.
Wallace State offers more than 200 options in academic, health and technical programs. Its main campus is in Cullman County on 300 acres in Hanceville, with a satellite location in downtown Oneonta.
Deborah Storey is a Huntsville-based freelance contributor to Business Alabama.
This article appears in the November 2023 issue of Business Alabama.