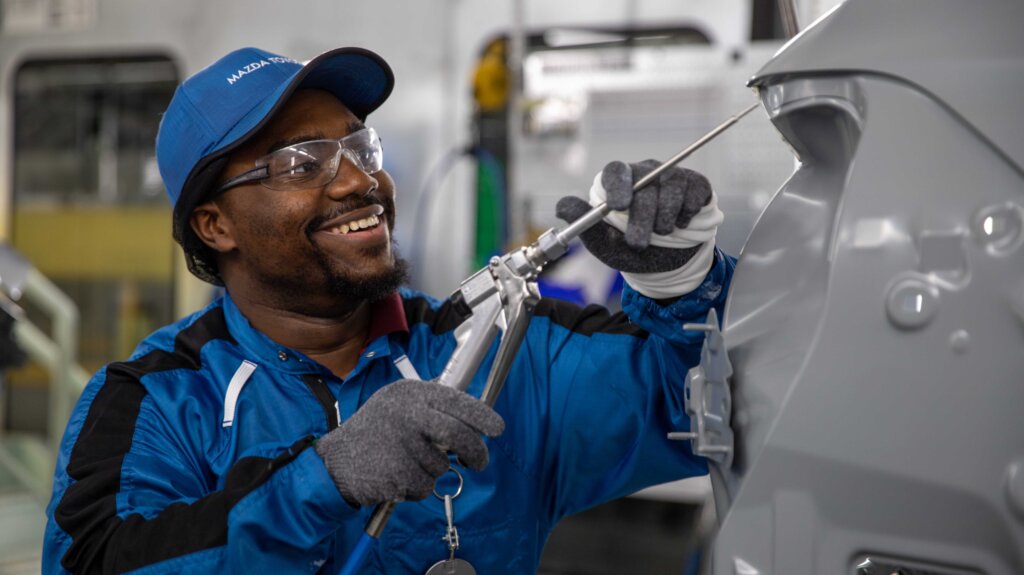
Good-paying jobs with benefits are here for the taking in Alabama’s automotive industry.
Employers are luring workers through job fairs, TV ads, partnerships with workforce development and educational organizations and even appeals on social media.
Roughly 42,000 people work in auto and parts manufacturing in Alabama, labor statistics show, but companies need more. Their strategies include flexible schedules, scholarships, certificate programs that practically guarantee a job and possibly hiring workers with a few blemishes on their criminal records.
Suppliers hiring
Original equipment manufacturers and companies that supply Alabama automakers are all hiring, says Alabama Automotive Manufacturers Association President Ron Davis.
“They’re all in the mode of continuing to work through current workforce challenges,” he says. “There are a lot of jobs out there — jobs with good pay and good benefits.”
Companies are strategizing with the state Department of Commerce, the Department of Labor, the community college system and AIDT to address workforce challenges, he says.
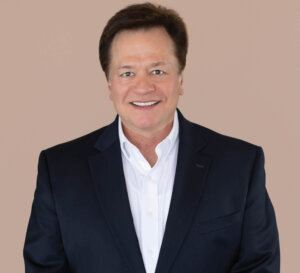
“The OEMs are working together to share best practices that can help the state and not cross any competitive lines defined by antitrust (restrictions) but to really, really improve how we’re managing our workforce,” says Davis.
Every OEM has a strong initiative to evaluate the workforce and continue working on issues like employee retention and recruiting the right people, he says.
“We’ve created videos to encourage young people to take a look at the industry,” Davis adds.
Honda, Mercedes-Benz, MTM, Hyundai and Toyota Alabama are represented together in an AIDT initiative called SHIFT aimed at career “shifters,” high school graduates and workers from other states. The ShiftinAlabama.com website connects people directly to job listings.
SHIFT is “about how you can shift your thinking and shift into a new career and shift into a better life,” Davis says.
“We have creative things going on all across the state,” he says. “One of the things we looked at was the labor participation rate.”
One source of potential workers is families needing a flexible schedule. “They just can’t do a rotating shift because they need to be home at night when the kid gets home from school,” Davis says, “so we were looking at that.”
Another untapped labor source could be people with a criminal record, he says. The idea is practical — and philanthropic. “How can we help them recover from their problems in the past and have a good job in the industry?” asks Davis.
‘Will keep hiring’
Mazda Toyota Manufacturing in North Alabama currently has 3,700 team members and is casting the net for hundreds more. MTM has partnered with AIDT (Alabama Industrial Development Training) to facilitate hiring, onboarding and training new team members, says Mark Brazeal, MTM vice president of administration. Local chambers of commerce and educational institutions also are helping with recruitment.
“We market opportunities at career and job fairs, and through advertising employee services on social media, television and digital platforms,” Brazeal says. MTM will keep hiring “until it reaches the approximately 4,000 team members outlined in its mass hiring plan.”
The goal is to operate “two production lines on two shifts in alignment,” he adds.
Gearing for growth
Toyota Alabama currently employs more than 1,800 people and is looking for more also.
“We are hiring production and maintenance team members,” says Jason Puckett, president of Toyota Alabama. “We are gearing up for growth.
“Our new engine line will start up this year, but, to us, growth is more than increased production,” he says. The company wants to be “a force for growth and change in the community. Ensuring that we have the right qualities for a great career coupled with a strong community mission and impact is our key to attracting great talent,” Puckett says.
“As electrification changes mobility, my focus is on our 1,800 team members and their skill development,” he adds. “We’re the total package — great pay and benefits, career opportunities, challenging and fulfilling work and a culture of inclusion.”
In 2022, Toyota announced a $222 million investment in its manufacturing facility in Huntsville to create a four-cylinder line that will include engines for hybrid electric vehicles. That project should be complete in late 2023.
“This investment marks our sixth building expansion and eighth major investment,” Puckett notes.
‘Huge demand for skilled workers’
Hyundai Motor Manufacturing Alabama currently employs about 3,800 people, says Scott Posey, public affairs manager for HMMA. That’s up about 200 during the past year.
Much of the increase has been due to the plant’s move into electric vehicles, beginning with the Santa Fe Hybrid SUV last year and the new Genesis brand electrified GV70 SUV. Posey says employees with technical expertise are needed throughout the state’s manufacturing sector, not just the growing automotive industry.
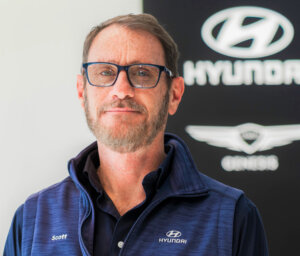
“There is a huge demand for skilled workers, and especially those that have the more highly skilled jobs in maintenance and engineering and other jobs that require strong technical skills. The demand is outweighing the supply,” he says.
Attrition and expansion create a consistent pressure on recruiting, he says, adding, “It’s squeezed and it’s tight, but it’s certainly not critical or catastrophic. It’s not affecting our production.”
Hyundai recruits on college campuses and offers in-house training to existing employees who might be interested in maintenance and engineering work. There are also management and leadership programs. Hyundai also works with AIDT on worker training.
Aside from current recruiting, HMMA has worked in recent years to ensure that the next generation has the needed skills. “As manufacturing processes become more advanced, the skills that are needed by manufacturing become more advanced. I think we all share in this challenge,” Posey says.
HMMA has partnered with the Southeastern Center for Robotics Education (SCORE) based at Auburn University. SCORE creates student teams and encourages competitions. “Their mission is to create interest in robotics technology in middle school and high school students and others,” Posey says. The result has been the creation of the Hyundai Initiative for Robotics Excellence (HIRE), with HIRE teams now in every middle and high school in the Montgomery public school system.
Also last year, HMMA donated vehicles through the Central Alabama Works program to two area high schools for hands on education. “Those vehicles allow students to basically take them apart and put them back together again. They learn about vehicles and how advanced they are.” If some of the students one day decide to work at Hyundai, so much the better.
“We’re investing in a workforce of our future,” Posey says. “It’s absolutely our hope that by being exposed to the technology and making it fun and getting them interested in that early, that we’re also getting them familiar with the Hyundai brand. We’re a local employer with very competitively paying jobs right here in their backyard.”
Develop the skills
Honda’s Alabama Auto Plant, in Lincoln, employs about 4,500 people.
“Like most businesses and industries, we have been impacted by the growing labor shortage,” Samantha Davis, spokesperson for AAP, says.
“That’s why Honda has been active in creating and participating in a number of workforce development initiatives in Alabama, as well as working closely with local and state leadership and groups such as East Alabama Works, the Alabama Workforce Council and AIDT, as part of our efforts to develop the skills of potential associates.”
Educating workers
To keep new workers up to date with technology, auto industry leaders are turning to the state’s community colleges to develop employees ready to step onto the plant floor.
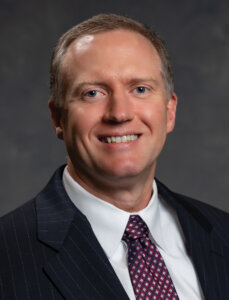
“The automotive industry is rapidly changing with advances in electric vehicles, battery technology and the manufacturing processes associated with them,” says Barry May, executive director of workforce and economic development for the Alabama Community College System.
“The colleges are working closely with the industry to understand these advances and adapt our curriculum accordingly to ensure our students are prepared with the skills they need to be successful.”
May says the college system introduces students to important technologies early in their education programs and joins forces with businesses to make that happen.
“We are a proud partner with the Alabama Automotive Manufacturers Association to provide scholarships to students who are interested in pursuing automotive-connected careers,” May notes. “We also take the lead in developing corporate sponsorships through our FAME apprenticeship programs that connect students to businesses before they graduate from college.”
Students who participate in Federation for Advanced Manufacturing programs are expected to earn 40% more in five years than students who did not pursue these programs, May adds. For more information on the scholarships, see dreamitdoitalabama.com/aama.
The Alabama Community College System website lists dozens of automotive industry careers from service technicians to engineers, with classes on nearly every campus.
Deborah Storey is a freelance writer based in Huntsville. Gail Allyn Short, Jane Nicholes, Kathy Hagood and Katherine MacGilvray also contributed to this story.
This article appears in the March 2023 issue of Business Alabama.