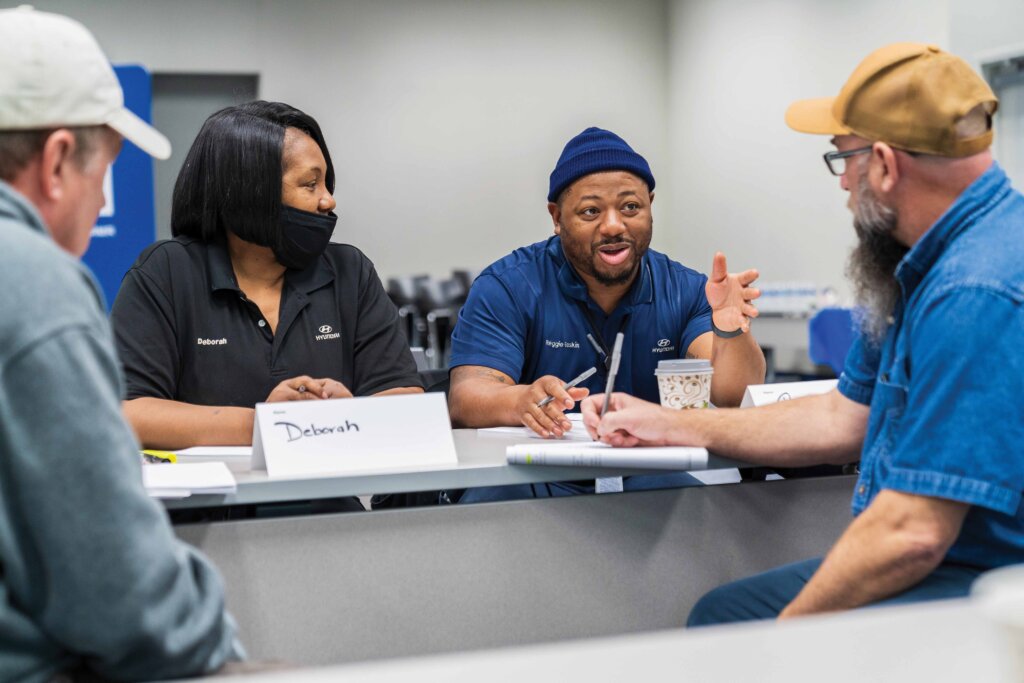
As Alabama businesses win big government contracts, add production lines and announce plant expansions, CEOs are all smiles for the cameras — until they can’t find enough employees to manage the work.
With Alabama’s employment rate hovering around 3%, most people who want jobs have no trouble finding them. Even as the economy slowed in late 2022, many business windows were decorated with more “now hiring” signs than paper snowflakes before the holidays.
In November, the Alabama Department of Labor announced that the state added nearly 47,000 jobs over the previous year, going so far as to call it “remarkable job growth.”
In such a competitive hiring market, many Alabama companies are becoming creative to lure workers with big bonuses, commercials in Spanish and English, partnerships with area colleges and expanding apprenticeship programs. The notion of keeping current employees happy is not forgotten, either, with management tracks and in-house training and development.
Airbus
Airbus in Mobile is flying high.
The company announced an expansion earlier this year, with plans for 1,000 more employees, and announced a three-prong strategy to attract workers — an apprenticeship agreement with Bishop State Community College, the Airbus On Board program to teach anyone with five years of work experience in any field how to do aerospace work, and the Airbus Global Graduate Program to attract new college graduates.
Almost before the new programs took off, Airbus launched a series of high-profile TV ads — during the World Series, Crimson Tide football games and more — featuring current employees encouraging folks to join the team. (See more details in our October 2022 issue.)
Hyundai
Over in Montgomery at Hyundai Motor Manufacturing Alabama, automotive assembly is in high gear.
With the rapid growth of advanced manufacturing in the Southeastern U.S., Hyundai is investing in its future workforce with a number of in-house development and training initiatives.
“Recruiting a workforce that has the skills and proficiencies needed to complement continual advancements in automotive manufacturing is challenging, due to competition for talent among manufacturing employers,” says D. Scott Posey, HMMA public relations manager.
The company cultivates and develops current team members and participates in partnerships with local two- and four-year colleges and area public schools.
To lure workers, Hyundai is in partnership with AIDT for the Pre-Employment Selection Program “to match our specific needs for the recruitment and hiring of new team members,” Posey says. “This includes the conducting of interviews, as well as classroom and hands-on training for prospective production team members.”
Another approach is Hyundai’s Modern Manufacturing Program in partnership with Central Alabama Works.
It “provides a hiring pipeline for area high school students via job fairs and site visits to HMMA,” Posey says. “HMMA also donates new automobiles to CAW’s modern manufacturing labs to provide students exposure and early training on vehicle assembly.”
Meanwhile, HMMA continues in-house development and training programs for existing employees to help fill positions.
The Maintenance Apprenticeship Program creates an internal pipeline of qualified HMMA team members to fill positions in production. Those who qualify for the program are required to complete industrial maintenance education courses and on-the-job training to become eligible for maintenance positions.
During the 12-month program, participants work toward achieving Maintenance Technician Certification offered by Trenholm State Community College in Montgomery.
Through partnership with AIDT, HMMA also offers Group Leader Leadership Training to provide “Leadership Skills 1” for new supervisors.
Current employees can take part in the career opportunity placement program, pre-promotional leadership training and a leadership boot camp.
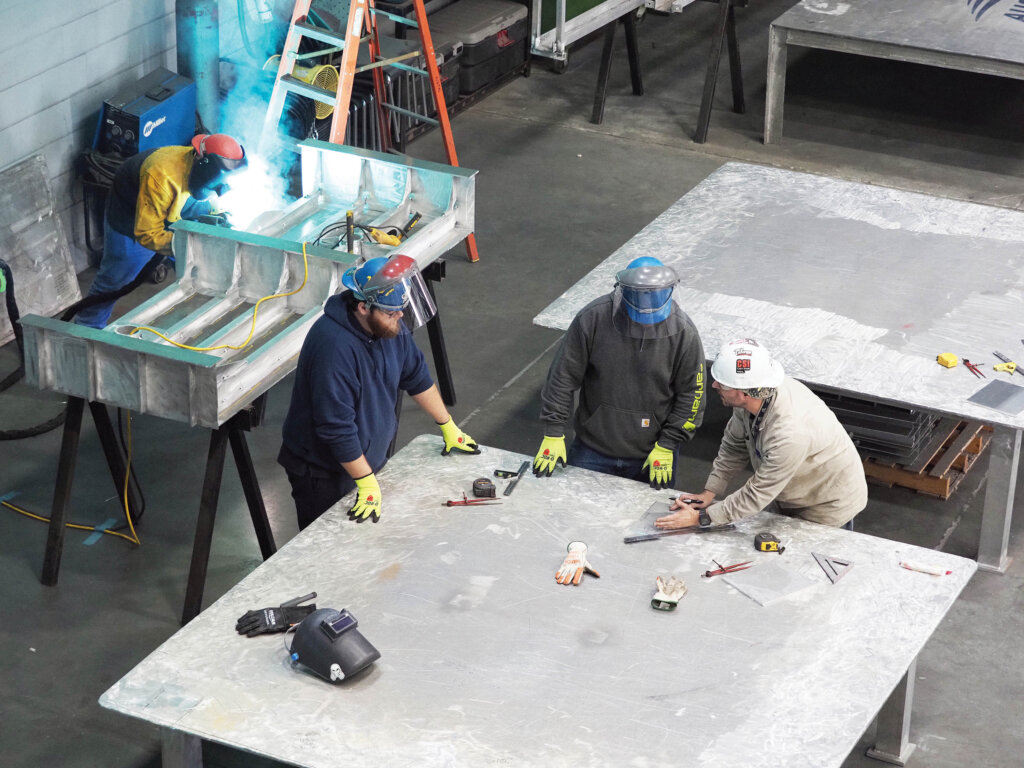
Austal USA
In July of 2022, the U.S. Coast Guard awarded Mobile-based Austal USA a contract worth up to $3.3 billion for design and construction of up to 11 offshore patrol cutters. The company also won a $230.5 million contract for the EPF 16, an Expeditionary Fast Transport ship for the U.S. Navy.
Fortunately for Austal, its leadership had started an in-house workforce development program for welders and fabricators in partnership with AIDT way back in 2001. Also that year, Austal, AIDT, Mobile Works and Bishop State Community College collaborated to develop a two-year apprenticeship program. That program expanded to four years and now includes pipefitting, electrical and outfitting.
Graduates earn U.S. Department of Labor certification and journeyperson status, giving them opportunities for full-time employment and career growth. They often advance into management or critical roles in engineering, production control, test and activation, project management and more, Austal officials say.
After a hiatus for COVID-19, the program should reopen in early 2023.
Through a partnership with Alabama Career Center, selected applicants go through a four-year program of 576 hours of classroom training and 8,000 hours of on-the-job training in their chosen crafts.
“Those remaining in their craft become elite technicians who support Austal USA’s new construction and post-delivery service business,” Austal says, adding that the apprenticeship program has been extremely successful.
“Current team members within our production trades are graduates of the program, many of whom have been promoted into leadership positions,” company officials report.
Mazda Toyota
And in Huntsville, officials of Mazda Toyota Manufacturing announced in summer of 2022 that the ramp-up to hiring 4,000 employees for the massive $2.3 billion production facility was almost complete.
“We’re getting close but we can always use more,” Janette Hostettler, senior vice president of production, told AL.com at the time.
In its early phase of hiring, MTM announced a sign-on bonus of $3,000 for new hourly employees, and an “appreciation payment” of the same amount for existing hourly workers. Wages also increased, from $17 to $18.35 an hour to start.
Hostettler said prospective employees don’t need manufacturing experience. “Our maintenance guys, we will teach you everything you want to know,” Hostettler said.
Wellborn Cabinet
Wellborn Cabinet in Ashland started in 1961 and now employs just over 1,300 people. Business is so good that the company announced that a $17 million expansion in Oxford will start operations in 2024.
The number of applicants isn’t a problem, company officials say, and resulted in more than 300 hires thanks to a revised recruiting strategy, local market analysis and new compensation structure.
Once a company finds the workers, however, Wellborn officials say, then “retention is key.”
Deborah Storey and Mike Kittrell are freelance contributors to Business Alabama. She is based in Huntsville and he in Mobile.
This article appears in the January 2023 issue of Business Alabama.