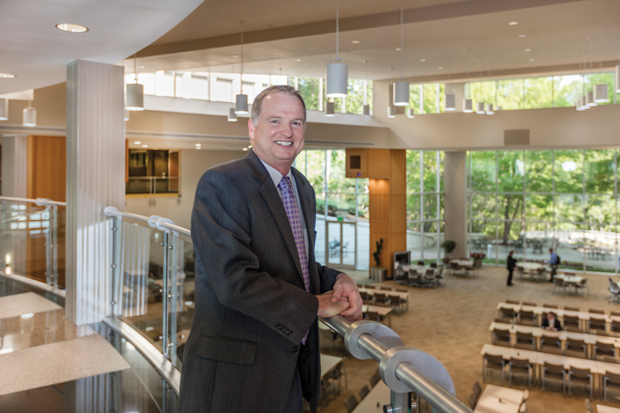
Facility management is like an iceberg in the water, says Joe Morris, “People only see the tip of it.
“Most folks see very little of what is going on. If we are doing our jobs right, then you really are not aware of what it takes to make it happen, ” says Morris, the director of facilities for Blue Cross Blue Shield of Alabama. Morris, based in Birmingham, is responsible for managing all of the company’s facilities from Huntsville to Mobile and around the country.
Used to be, a facility manager’s job was to make sure the toilets flushed, the temperature was right and the light bulbs worked. Not so today. According to the International Facility Management Association website, “Facility management is a profession that encompasses multiple disciplines to ensure functionality of the built environment by integrating people, place, process and technology.” Underscore “multiple disciplines.”
Morris says his job as director of facilities includes planning, design and work place enhancement, maintenance, landscaping, food service, janitorial and physical security, including four Tier 3 data centers that house highly sensitive information.
Understanding budgets, costs and resources has changed the facility management profile, says Morris, who is working on a degree in information systems to better equip him for handling the developing technology challenge.
“We do have to wear a lot of hats, because you never know who is going to ask you a question, whether it falls into your line of responsibility or not, so we have to have knowledge of basically the overall operation, ” says Paul Wuebold, senior executive director, facilities and grounds at the University of Alabama in Tuscaloosa.
Greg McKelvey, executive director of maintenance operations and energy management at UA, says he doesn’t think the basic concept of facilities management has changed much but the way the job is done has changed.
“I think some of the biggest changes for facilities managers and their employees as well is the incredibly rapid advancement of technology, and how to harness that technology to help make equipment last longer, help improve communications to the field or even improve communication from the equipment to the technician, ” says Wuebold.
Most facilities managers will tell you that the increased scope of the job, the rapid advances in technology, increased expectations from employees and management and doing more with less are some of the major issues they face.
Morris says that 20 years ago, “You were writing a service request on a piece of paper that goes into a service box. Everything today is with smart phones. We are tracking every call we get. We use data to make decisions on what needs to be replaced, what needs to be repaired.”
According to Morris, “Our customers are internal customers, so we also try to provide those folks with things they need in order to get their jobs done. They can do their jobs better for our customers because of something that we are doing, not only keeping the lights on, the doors open and keeping water running, but doing things like having an ergonomic work station for them to function properly. When they are sitting at a desk all day taking customer calls or working claims, creating that comfortable environment is important, because what they do is tough.”
“Over the course of the past 10 years, ” Wuebold says, “we have found that we have become more focused on core competencies and have become a master of the trade instead of a jack of all trades. Some of the technicians have been around a long time and are able to take care of 50-year-old equipment just as well as they can 5-year-old equipment. But because of the way the business model has expanded, we have taken on a greater role, and we are looking for long-term strategies instead of short-term strategies, which means that in the old days they may have found, based on funding, a fix that will be good for two to five years, where we are looking for the 30- to 50-year fix.”
“As far as changes, ” McKelvey says, “one of the biggest changes is certainly the expectations of our customers. They expect more not just from their work lives but their leisure lives so everything needs to be newer, better and more efficient. There is more emphasis today on sustainability and being good stewards of the limited resources of the earth, so you always have to take sustainability into consideration today. One of the biggest changes I have seen is there are better tools for management today and better ways of managing the process, such as Six Sigma, LEAN, continuous improvement methodologies and cost-benefit analysis.”
And there is always the money challenge.
“The university always wants us to do more with less, so we have to be very good stewards of the university’s money, to make sure we not only do it right but that we do it as efficiently as possible, ” McKelvey says.
Wuebold adds, “I would say it is trying to find enough dollars to do all the things you need to do. You have to prioritize the things that will have the biggest impact, either positive or negative, on the university’s mission and goals.”
“Our company’s goals are manage costs, superior customer service and support growth, ” Morris says. “When I look at facilities, every square foot has value, so I am trying to make sure that I am getting the most value out of that square foot for this organization. And I am also trying to manage those costs every year.”
Morris says he looks for opportunities to cuts costs, while trying to make sure that Blue Cross Blue Shield is spending “the right amount of money to support the costs needed to generate business.”
And while much of facility management work goes unnoticed, that is not the case when it comes to grounds maintenance.
“We obviously play a very viable role in helping attract and retain students, ” McKelvey says. “Having beautifully landscaped grounds is something that gives a very good first impression when students and faculty first come here and helps them decide that this is where I want to spend my next four years.”
Wuebold adds, “We are evaluated annually by a third party company that comes in and evaluates the facilities: the maintenance component, custodial services, grounds and landscaping and energy management. We are on a multiyear run of being ranked No. 1 in all four categories among 15 peer group institutions that have a similar mission, population and a regional impact like the University of Alabama.”
Facility Management Track to the Majors
Timmy Hinds, director of stadium operations at Regions Field, home of the Birmingham Barons baseball team, faces many of the same challenges as his fellow facility managers.
“A big part of the job is understanding the importance of working ahead, getting as much done today as you can, because you never know what tomorrow is going to bring. If something goes wrong, something breaks down, all of a sudden you get behind the eight ball, ” says Hinds.
Hinds’ job is to keep the stadium clean, presentable and functional on a day-to-day basis, which means a lot of 12-hour days, even on non-game days, when special events are often held at the stadium.
“There are definitely long hours in this particular industry, especially in my department, ” Hinds says.
Hinds has been in baseball five years, but this is his first year in Birmingham. “I studied sports administration at the University of Cincinnati, and that helps me a lot in the management areas here, ” Hinds says, adding that he also learned a lot from previous jobs in New Orleans and Beloit, Wisconsin.
“I have learned a lot of janitorial, a lot of plumbing, a lot of carpentry stuff, a lot of electrical work, a lot of the basics, and when you bring in contractors to do bigger jobs, you learn as much as you can from them as well, so that you can kind of keep things in-house in the future and save the company some money, ” Hinds says.
“We did have a leak in our facility that had been running for quite some time, and that can be a difficult thing to diagnose. It can be as little as a toilet running or it could be a pipe leak. It took a lot of detailed work to determine what was wrong. It turned out to be a running toilet, and we were losing about three and a half gallons of water a minute. Little things like that can really add up.”
And of course, there is new technology at the ballpark.
“We had this new piece of equipment that came in called Trackman, something we had installed from a business standpoint. It tracks velocity and the break of a pitch, how far the ball goes and all that, and that gets sent right to the White Sox. It is another form of scouting that means they don’t need to have a person here, ” Hinds says.
As a new stadium, Birmingham is one of the more advanced facilities, according to Hinds. “There are elements here that only a few teams have, but you can see the effect it has on the team. We prepare them for the major league level.”
Hinds says he likes minor league baseball and has no plans to move to the majors.
“I think it is really cool to watch the players strive to get to the big leagues. I have always wanted to get to a stadium like where I am now, ” he says.
Bill Gerdes and Art Meripol are freelance contributors to Business Alabama. Gerdes is based in Hoover and Meripol in Birmingham.