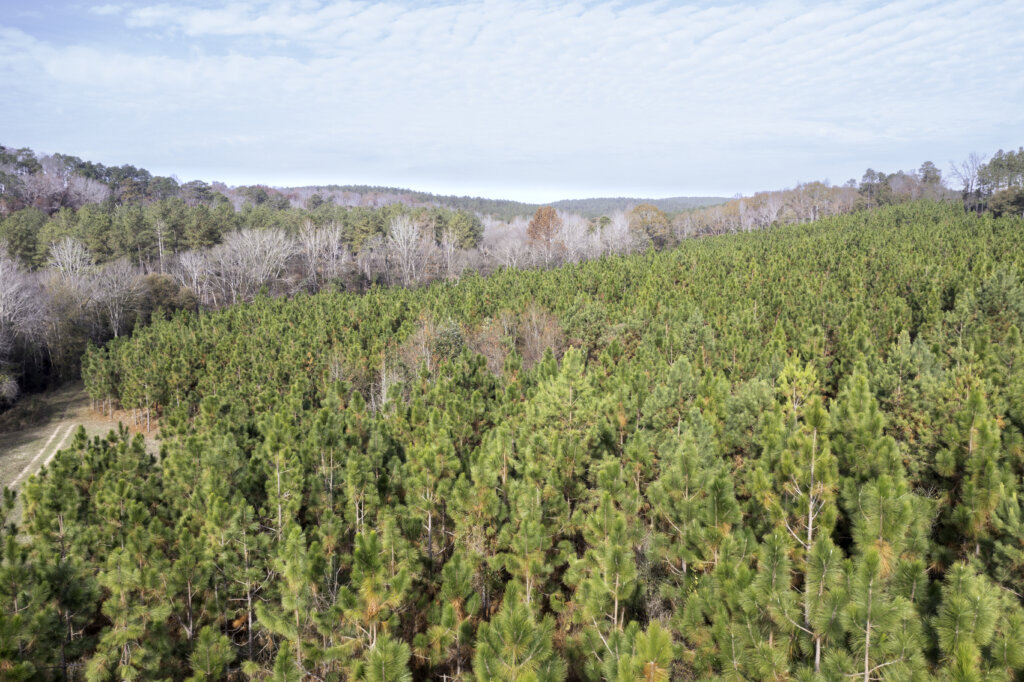
I think that I shall never see, a poem as lovely as a tree. Poet Joyce Kilmer was correct. Trees are stunning, and in Alabama, lucrative.
According to the Alabama Forestry Commission’s Forest Inventory Analysis Data, the state’s 23 million acres of forested land is larger than Connecticut, Delaware, Massachusetts, New Jersey and Rhode Island combined. Approximately 93% of it is privately owned.
In 2019, Alabama exported $1.3 billion in forest products. From farmer to factory, many hands nurture and move these products.
This is their story, Alabama’s wood industry, men and women going out on a limb — sometimes literally.
In the world of wood, misconceptions abound. “Many people compare our trees to the rainforest or old growth,” says Ashley Smith, director of education programs for the Alabama Forestry Association. “It is not true. Our climate and growth patterns are different here.” She adds that much of Alabama’s timberland has been here for years, cut for agriculture long before most of us were born.
“Our soil is fabulous for tree growth,” says Smith. Therefore, tree farms flourish. Red Hill Farm is one such fertile entity, owned by husband-and-wife team, Trice and Johnnie Nichols.
The couple has farmed their 900 acres near Prattville for about two decades, growing pine and hardwood on land that has been in Johnnie’s family since the 1850s.
“Pines grow from seedling to 70 feet tall in 30 years,” Trice says. “A tree is similar to livestock,” he continues. “In the earlier stages of life, you ‘fatten it up,’ with plenty of water and rich soil to make the tree bigger, faster.”
Pines are rotated, thinned and sold throughout the life cycle, but as a rule, the taller the better. At its maximum height, pines reach telephone pole category — the most valuable and very marketable. Loggers take it from there.
“I love being in the woods,” says forester Earl Edmondson, of Harrison Forestry/Harrison and Sons Logging in Maplesville. “The business is more mechanized now.”
His schedule is straightforward. “When the weather is dry, we haul wood.” His crews average about 156,000 tons of logs annually, spanning 22 Alabama counties.
Co-owners of Montgomery’s Legacy Land and Timber LLC, Bobby Loughridge and Donald Clark agree about logging’s mechanization. “Insurance companies don’t want to see us in the woods ripping trees,” Loughridge notes. “We are much less hands-on.”
In the tree business, the logger is the broker, with contracts between farmers and sawmills and factories. Once delivered, logs become raw materials and the magic happens. Alabama trees become products for the world — timber, plywood, wood pulp, paper, liner board, sawdust, poles, crossties, lumber and more.
Wood becomes commodity at the state’s major players, including Georgia-Pacific, International Paper, Packaging Corp. of America, WestRock, Kronospan, Brown-Forman Cooperage, Louisiana-Pacific, Weyerhaeuser, Westervelt and Great Southern Wood Preserving.
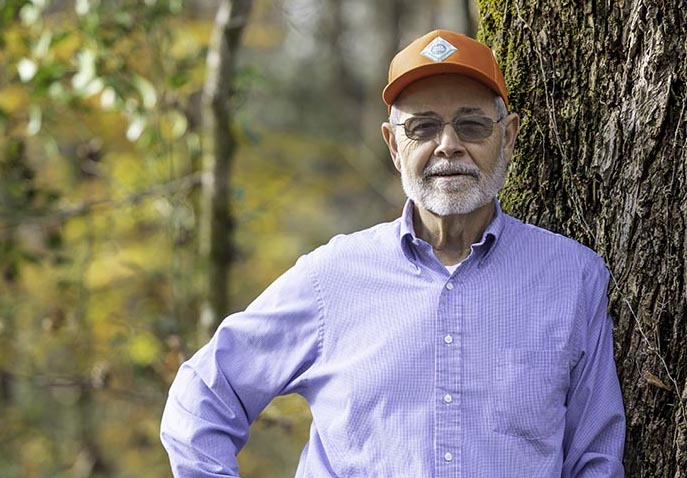
Newer entries to the market are Rex Lumber, Abbeville Fiber, Jasper Lumber and Westervelt’s new Thomasville mill.
Nothing is wasted. From bark to sawdust, every component of a tree is marketable. Though each factory marches to the beat of a different saw, Alabama mills are challenged with evolving markets, increased operating costs and the erratic supply and demand issues from COVID.
“We have seen increased demand from the DIY markets in 2020 and 2021,” said Georgia-Pacific spokesperson Erica-
Denise Solomon. “That market has pushed volume up across the board in all of our building products businesses.” GP has six facilities across Alabama.
As some markets increased, others — once staples of the industry — are dramatically shrinking. Paper, once the cornerstone of sawmills, is one such commodity. Data once written is now stored electronically. Georgia-Pacific exited the communication paper business in 2019.
Meanwhile in Abbeville, life is good for YellaWood. “We run all the time,” says Michael Lancaster, vice president of sawmill operations at Abbeville Fiber. The facility opened in summer 2019 and joins other mills supplying 15 Great Southern Wood treating plants.
“We were having a good year even before COVID,” recalls Great Southern Wood’s Ryan Blalock, chief purchasing officer. “But once the coronavirus hit, markets plunged and so did lumber supplies. But people were homebound and wanted to make improvements.”
He continues, “Suddenly, demand for YellaWood soared. We had weeks trying to supply the outrageous demand for wood.”
Today Great Southern’s supply and demand are gradually lining out but issues remain with fuel costs and staffing. “Fuel effects our loggers, truckers, suppliers, almost all phases of the business,” says Blalock. “We are seeing those costs rise dramatically.”
“Labor is also a problem,” he notes. “Fortunately, we have a group who is our backbone, but for additional growth it’s now difficult finding additional workers.”
With a January 2021 startup, one of Alabama’s newest mills is Westervelt in Thomasville, the sister plant of Westervelt in Moundville. “Production has been a struggle,” says Mark Richardson, sales and marketing director in the company’s wood products division. “We hired a full crew, but because of COVID, we were unable to conduct planned training in our Moundville plant for new Thomasville employees.”
Westervelt’s Woodlands Director Dave Donaldson adds, “I still think from a supply chain standpoint we are 18 to 24 months away (from normality). The swing may be less but we still have to deal with interruptions due to a next variant.”
Westervelt’s markets include the construction industry through building component manufacturers like truss makers, building material distribution yards and pressure treaters.
From the newest to one of the oldest, Scotch Plywood Co.’s origins trace back to Clarke County, 1888. Today, two Alabama sites, Fulton Plywood Mill and Beatrice Mill, have a combined workforce of more than 400 employees.
“Our peak production is generally May through October,” says company Vice President Gray Skipper. “[Sales] demand goes in cycles. February through May.” He adds, “September and October are also big for us as people are rushing to make home additions, repairs and projects before winter snow hits in our Northeast and Midwest markets.”
New technologies and new uses for wood are emerging in Alabama, too, as companies create substitutes for coal. The list includes Zilkha Biomass Energy, Alabama Pellets (Pinnacle Renewable Energy) and, coming soon to Sumter County, Enviva.
With a projected 2023 startup date, Enviva is designed to produce more than one million metric tons per year of wood pellets. The site will be the largest wood pellet production plant in the world.
“Alabama has been supportive for business and industry,” says Rick Frederick, Enviva’s Gulf Coast community relations manager. “The state provides a combination of skilled workforce, raw natural resources and tremendous terminal and port access to the Gulf, such as the Port of Mobile. It’s a match made in heaven.”
Finally, the finished product, wood in all forms, goes to market by trucking domestically, or from tree to shining sea.
“The breakbulk and container tonnage from Alabama State Port Authority and APM Terminals Mobile is approximately 875,764 NT (net tonnage),” says Anna Ward, ASPA director of sales and customer service. “This figure includes wood pulp, lumber, plywood, poles and crossties.”
She adds that major markets for wood out of Mobile’s ports are Germany, Spain, Italy, Dominican Republic, Haiti, Jamaica and China.
Alabama’s wood is nurtured, cultivated and transformed into products shipped across the country and throughout the world in the final process from seedings to selling.
“Over the years I have learned how vital the forest industry is to Alabama,” says Ashley Smith. “We grow 23 million acres of trees, about two-thirds of the state.” But it’s more.
She adds, “Alabama forestry is a community, from landowners to loggers to foresters, to natural resource professionals and others whose livelihoods depend on the sustainability of trees. Alabama forestry is rooted in the past while also looking to the future.”
Emmett Burnett and Art Meripol are freelance contributors to Business Alabama. Burnett is based in Satsuma and Meripol in Hoover.
This story appeared in the January 2022 issue of Business Alabama magazine.