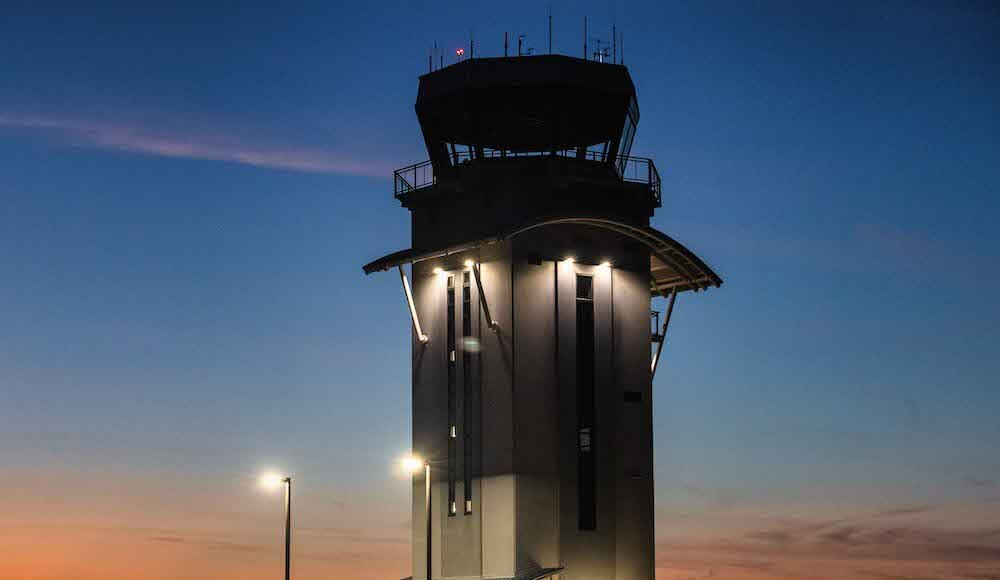
It sounds like a futuristic physics challenge: Build a seven-story, 87-foot-tall air traffic control tower with an interior of 25 feet by 25 feet, and make sure all of it can withstand hurricane-force winds of 174 miles per hour.
White-Spunner Construction LLC did just that with the new air traffic control tower at Gulf Shores International Airport at Jack Edwards Field. The result serves an airport with the second-largest number of takeoffs and landings in the state.
Completed in 2021, it is thought to be the first new tower in Alabama in 30 years. It was named General Aviation Project of the Year by the American Association of Airport Executives.
“There were some unique aspects of it,” says Adam Bryce, the construction superintendent on the tower for White-Spunner. “The height wasn’t really so odd — 87 feet is a tall building, but it’s not like a skyscraper.
“What did make it unique was the small footprint — 25 by 25, straight up, brings up challenges in itself because you just don’t have much room inside the building.”
Working with AJT Engineering of Cocoa, Florida, and Barge Design Solutions, with three offices in Alabama and headquartered in Nashville, Tennessee, Mobile-headquartered White-Spunner had to emphasize coordination and advance planning even more than on a project with a larger footprint.
The basic materials were pre-cast concrete and steel.
“The amount of steel that is in those precast panels is amazing. Each panel weighed around 53,000 pounds,” Bryce says. The entire structure weighs more than 2 million pounds.”
Everything going into the concrete had to be placed exactly. Two feet off the mark could make a big difference within limited space, he says.
“The challenge itself was because the tower was so straight up and small, you had to coordinate and think about how much stuff you’re really going to pack with manpower up the stairs.”
Speaking of stairs, the stairwell had to go up before people could really work on the upper floors, but the elevator was one of the last parts of the structure to be installed. Only a limited number people could work inside on one floor at a time.
In areas where glass had not yet been installed, construction materials and equipment could be lifted into place with cranes.
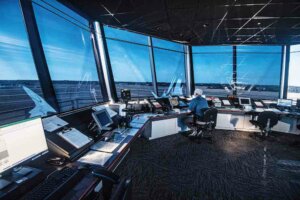
Overall, the control tower was not built from the ground up with upper elements stacked on top of each other, Bryce says. In fact, the glass-enclosed top floor, the so-called cab where the air traffic controllers do their work, was erected on the ground, then lifted by crane and set down gently on top.
“We had the glass in it,” Bryce says. “We had the cabinets in it, probably about 70% finished when we picked that thing up as one unit and set it on top and welded it off. It was pretty cool.”
The tower has seven floors, but the elevator only goes up six floors, so the controllers must climb one flight of stairs to get to their cab. The entire tower sits on 49 piers driven 15 to 20 feet into the ground and filled with crushed stone.
The first floor, on top of four feet of fill and the foundation, contains the lobby, elevator and mechanical room. The second and third floors are for shelf space and storage. The fourth floor is the manager’s office and a conference room where training takes place.
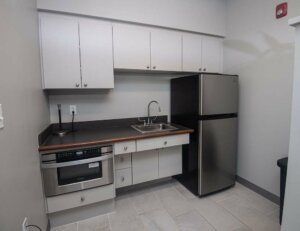
The fifth floor contains a break room, kitchen and access to the catwalk and balcony so employees can sit outside on their breaks. The sixth floor holds what Bryce calls “the brains of the building,” including computers, servers and electronics equipment.
Bryce lives in Gulf Shores and is well aware of the damage hurricanes can do.
“Everything on that tower is designed for 174 mph winds, even down to the enclosure on the generator,” he says. “As far as the glass is concerned, you have large-missile and small-missile impact glass all the way around that tower.” The glass in the cab weighs more than 500 pounds per panel.
For all the planning that went into the project, and even contending with delays in receiving supplies because of the COVID-19 pandemic, construction was finished on time in less than a year, Bryce says. The total construction cost was $4.3 million.
The Gulf Shores International Airport is owned privately by its airport authority, but must meet FAA regulations as well as state and local building codes.
“There’s not that many private towers that go out (for bid),” Bryce says. “The FAA builds towers as well.”
White-Spunner Construction is aware of other towers currently on the drawing board in Mobile and Auburn, and plans to bid on those projects when they are released for bid, according to Kayla Seawell, external affairs manager for White-Spunner.
White-Spunner is currently involved as the construction manager at risk for the multi-use cargo warehouse facility being built at Brookley Aeroplex for Mobile’s Airport Authority and is building a hangar for a private client adjacent to the airport in Fairhope, says Emily Stewart, communications specialist with White-Spunner. It is White-Spunner’s first construction project serving Fairhope’s growing airport.
Whether or not another new tower comes along, White-Spunner will be able to tout its experience in such construction.
“It’s a good-looking building,” Bryce says. “You’re not in Atlanta or in D.C. You’re in Gulf Shores. They put a lot of effort into the design. It’s a very good-looking building.”
Jane Nicholes is a Daphne-based freelance contributor to Business Alabama.
This article appears in the February 2024 issue of Business Alabama.