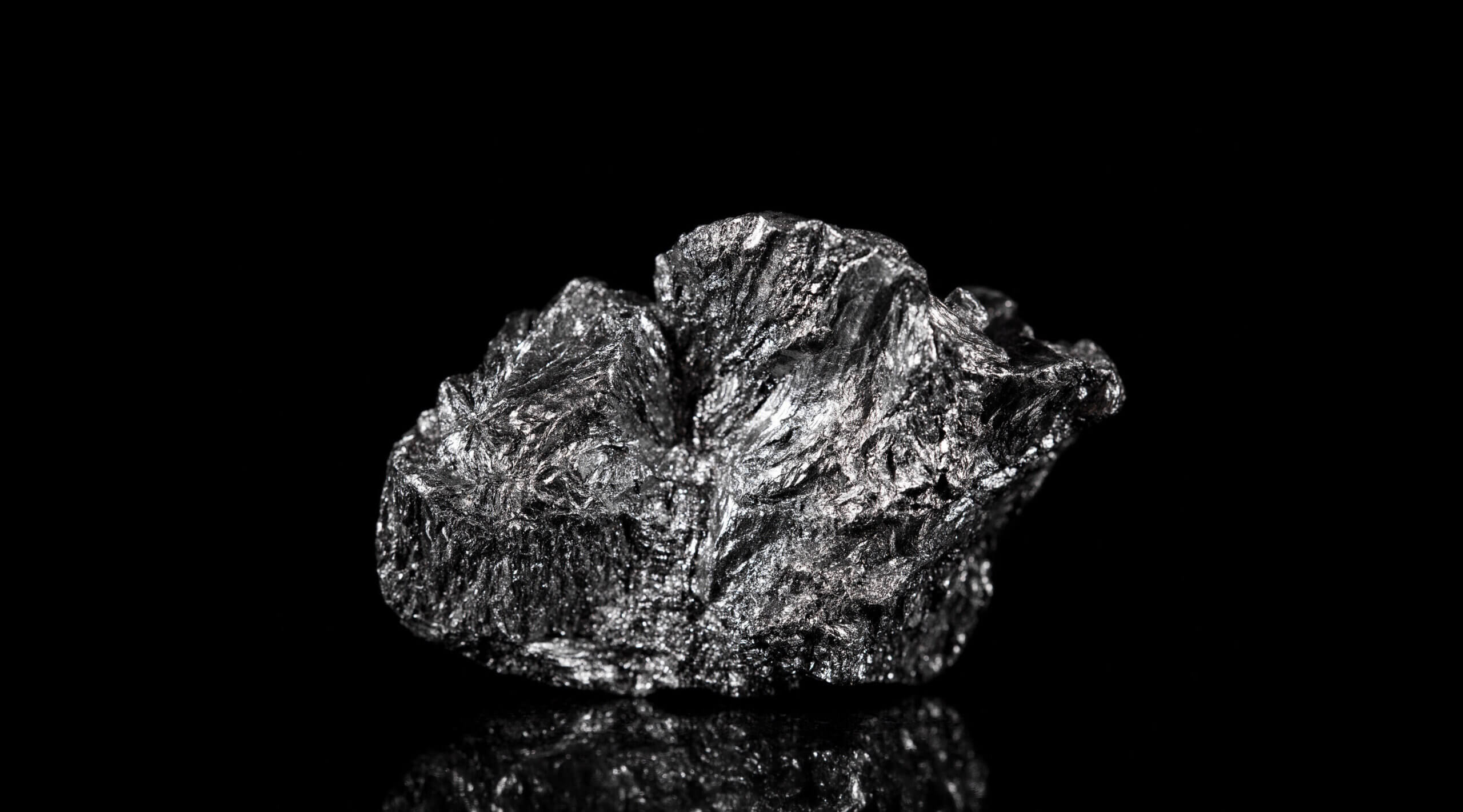
If graphite makes you think of a pencil, you’re running about a century behind the times. The mineral that you might easily mistake for coal is an essential ingredient in lithium-ion batteries.
And lithium-ion batteries are an essential ingredient in laptops, phones and — even more so — electric vehicles.
Eager to tap that market, Colorado-based Westwater Resources announced plans last June for a graphite processing plant in Kellyton, in Coosa County, virtually on top of Alabama’s rich deposits of graphite.
“You may see a Tesla coming down the road at you,” quips Christopher Jones, president of Westwater until his retirement in mid-February. “I see 800 pounds of batteries and 200 pounds of graphite. A Ford F-150 has twice that much.
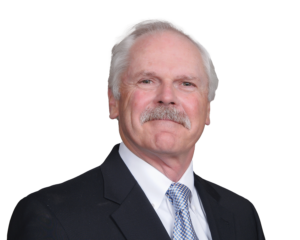
“Graphite is one of several essential parts of a lithium-ion battery — it’s 25% of the weight. Whether you’re holding a power tool or driving an electric car, you need to understand that there’s a batch of graphite in there,” he says.
“And you need to understand that virtually all of it is now coming from China.”
Alabama Graphite Products and its Westwater parent hope to tap the “made-in-America” market by sourcing graphite that will help “make those electric vehicles made in Alabama just a little bit more American,” Jones says.
First step is a processing plant.
The firm has received the environmental permit it needs to begin construction and expects to have work in progress this year and a completed, operating $80 million graphite processing facility before the end of 2023.
To start with, the plant will process graphite acquired from other sources, but structurally similar to Alabama graphite. That will allow the processing plant to be up and running quickly, producing 7,500 tons of graphite annually.
Jones is proud of the process the firm has developed.
“Our processing method is different than anybody else’s. It is much more kind to the environment, safer for our employees.” Instead of the hydrofluoric acid typically used in China, Westwater has developed a caustic bake process — “more complicated but easier on the environment” — and applied for a patent on the process.
Westwater and Alabama Graphite believe it’s important to consider the environment. “We want to know that the graphite that is in the battery that runs the laptop you may be using right now or the phone in your right hand — we want to know that that graphite comes to us, produced in a way that is environmentally sensitive and not harmful,” Jones says.
“One of the reasons that Chinese graphite is such a big part of the market is that their cost structure can be less because they’re not as fussy,” he says. “We think we can compete on cost; we know we can complete on environmental footprint and health and safety of our employees. We want people to be proud of the graphite we produce and the graphite that’s in their phone or their electric car or even their power tools.”
“We’re protective of our workers, the community and the environment,” Jones said when the project was announced. “Whether it’s mining or processing graphite, our company is committed to doing it in an environmentally safe, sustainable manner. The biggest virtue of electric vehicles and other battery-powered products is they reduce carbon emissions and are better for the environment. Producing the key materials for those batteries, we believe, can and should be done in an environmentally responsible way as well.”
While Jones sees an element of symbiosis for Alabama Graphite locating near Alabama’s robust automakers — all of whom are introducing electric vehicles throughout their product line up — the magnetic pull of Alabama comes from its bounty of graphite.
Alabama’s graphite belt, running up to 7 miles wide and 40 miles long through Clay, Cleburne, Coosa and Chilton counties, probably has “the most extensive high-grade flake graphite deposits in the conterminous United States,” according to Dane Vandervoort, a geologist in the state’s Geological Survey office.
While it was mined during the world wars, there has been no active mining since about 1950. But the demand for graphite has sparked a notable interest in the mineral, Vandervoort says. Research by Alabama Graphite indicated resource reserves of some 78 million short tons containing some 2 million short tons of recoverable graphite.
Alabama Graphite brought 42,000 acres of mineral rights along when Westwater purchased the company in 2018 and mining is definitely in the picture — but not yet.
Jones emphasizes that permitting for a mine is a lengthy process and he doesn’t anticipate any construction before 2027, with ample time for public input in the process. He expects mining to begin in 2028.
“We understand the deposit,” says Jones. “We are working now to explore that deposit in greater detail. We have a drill on the property and we’re sending core from that drill out for analysis. Once we understand that deposit a little better, we can put forward a design for that mine — another year or two — and begin the permitting process, which is lengthy.”
Local and state officials have jumped on the Westwater bandwagon, putting together a multi-million-dollar incentive package — nearly $30 million in state jobs and tax credits; employee recruiting and training from AIDT, and $4.7 million from local sources.
In return, the company pledges an $80 million initial investment, 80 to 100 jobs with an average hourly wage of $21.15, and plans for a total investment of $124 million.
When the project was announced, Gov. Kay Ivey said, “This plant not only will make Alabama the U.S. leader in graphite production, the go-to place for this important resource in battery manufacturing, it also will elevate our standing even more as a major player in the fast-growing electric vehicle sector.
“We’re home to four major auto plants, and the ability to source precious materials in state for the lithium-ion batteries used in electric and hybrid vehicles will be a big plus in attracting other manufacturing jobs to the state.”
In mid-February, Jones, who has shepherded the Kellyton plant through initial dealings with local and state government, announced his retirement. Chief Operating Office Chad Potter will be the president and CEO and will fill Jones’ seat on the corporate board of directors.
Potter, who joined Westwater last year, has been involved in all aspects of plans for the Coosa County plant, said Westwater Board Chairman Terence Cryan. Potter is based in Alabama and has been responsible for construction of the processing plant, which should be complete in early 2023.
“He will continue to be based in Alabama to oversee the completion of construction activities at the Coosa Graphite Project in addition to his expanded role as CEO,” said Cryan.
Before joining Westwater, Potter was COO and vice president of operations for American Consolidated Industries in Alabama, Ohio, Kentucky and Tennessee. Before that, he worked in senior management at Nucor Steel in Decatur.
Nedra Bloom is copy editor for Business Alabama.
This article appeared in the March 2022 issue of Business Alabama.