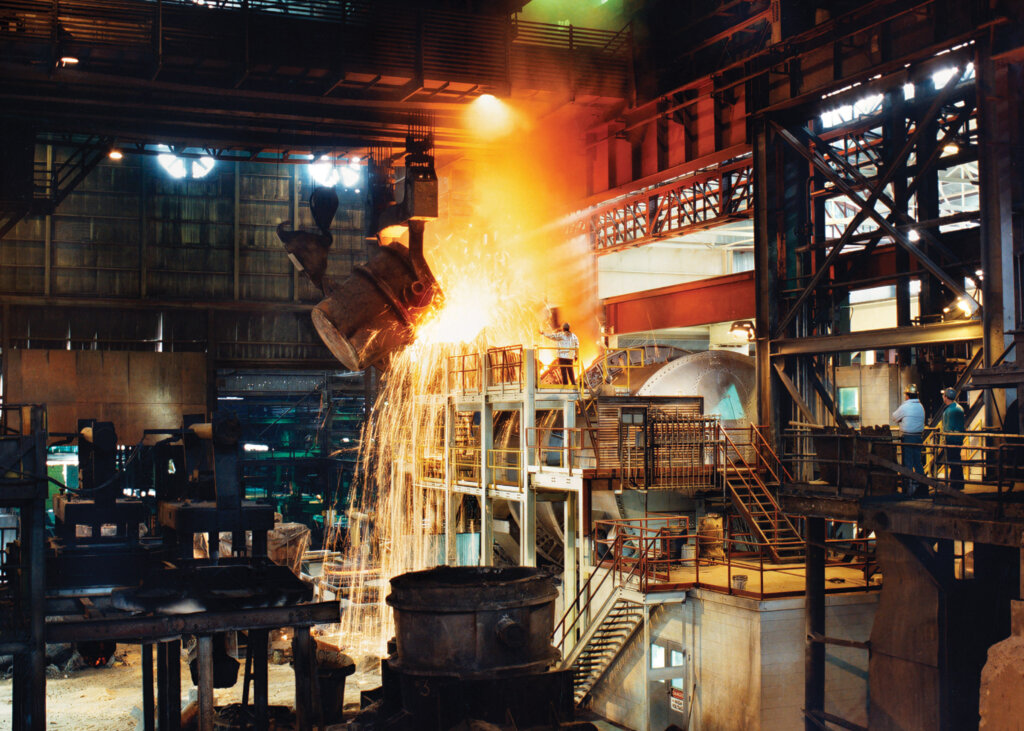
Switching to greener technology is a great concept. Getting federal money to help the environment makes it even more appealing to business owners.
A new project at American Cast Iron Pipe Co. in Birmingham is one of 33 to share up to $6 billion in federal funding for decarbonization efforts. The intent of the awards is to give American manufacturers a competitive edge in the emerging clean-energy economy.
The company’s $185.4 million Next Gen Melt project will replace its existing single-cupola furnace with four coreless induction furnaces by 2027. Existing buildings near the current melt center will house the new facility and the transition shouldn’t interrupt operations, company officials say. New induction furnaces will be phased in as they come online.
American, formerly known as ACIPCO, and all other ductile iron pipe manufacturers in the U.S. currently use cupola furnaces for primary melting. This new project replaces the single-cupola furnace with coreless induction furnaces that use electricity as the energy source for melting.
The new electric-melt technology is expected to reduce the plant’s carbon-dioxide emissions by 62% and melting/holding process CO2 emissions by 95%. The company also will be able to source energy from cleaner and renewable sources.
Next Gen will be among the first in the ductile iron pipe industry to use this electric-melt technology on this scale and could revolutionize the process for everyone, company leaders say.
“These upgrades can be replicated throughout the industry to provide lower-carbon footprint piping for municipal water systems to replace America’s aging water infrastructure,” explains H. Joe Thomas, senior vice president of engineering and project co-lead at American.
Another advantage of the new process is that it is expected to increase efficiency by 25%.
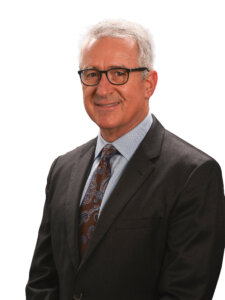
“This is the first of several initiatives planned over the next five to seven years to improve the company’s carbon footprint and sustainable manufacturing processes,” says Scott Murphy, American’s chief financial officer and project co-lead.
“This project will allow us to increase our melting capacity to meet growing demand from people and manufacturers across industries,” Thomas says.
In making the awards, the U.S. Department of Energy’s Office of Clean Energy Demonstrations hopes to accelerate clean energy technologies and help the country reach net zero emission by 2050.
The company is choosing to invest in the project because it is an integral part of the company’s culture to do things the “right way,” says Thomas.
“We saw a need for the development and successful implementation of a modern, sustainable, low-greenhouse gas emitting solution to produce ductile iron pipe,” he says.
Ductile iron pipe is critical to the nation’s water infrastructure, Thomas notes, and that aging water and wastewater infrastructure needs attention.
“We knew now was the time to invest in a modern and sustainable method of melting,” Thomas says. “We wanted to be the first in our industry to make this important transition and hopefully compel other ductile iron pipe manufacturers to do the same.
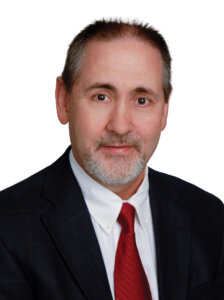
“The Next Gen Melt project is good for the environment and uses better technology,” Thomas adds. “We will be reducing our CO2 emissions while also alleviating supply chain concerns.”
The new process is expected to provide better production flexibility and quality control, as well as allow for increased capacity in the future.
And it’s expected to create more high-paying jobs in Birmingham. “We estimate 80 to 100 jobs will be created for the Next Gen Melt Project and future projects to increase production capacity,” Thomas says.
Cost saving is a significant benefit, with the new process expected to reduce operating costs by roughly 15%.
Company leaders say the project will be among the first of its kind in the U.S. ductile iron pipe industry to use the electric-melt technology on this scale. Other firms use the technology but not on this scale, company officials say.
“We plan to share best practices with other iron casting producers that rely on cupola furnaces, such as automotive and agricultural component suppliers, to accelerate uptake of the technology,” Thomas says.
The company’s pipe is an important part of the country’s infrastructure, Thomas says. It carries water from sources like lakes, rivers and streams to treatment facilities, then on to homes and businesses and back.
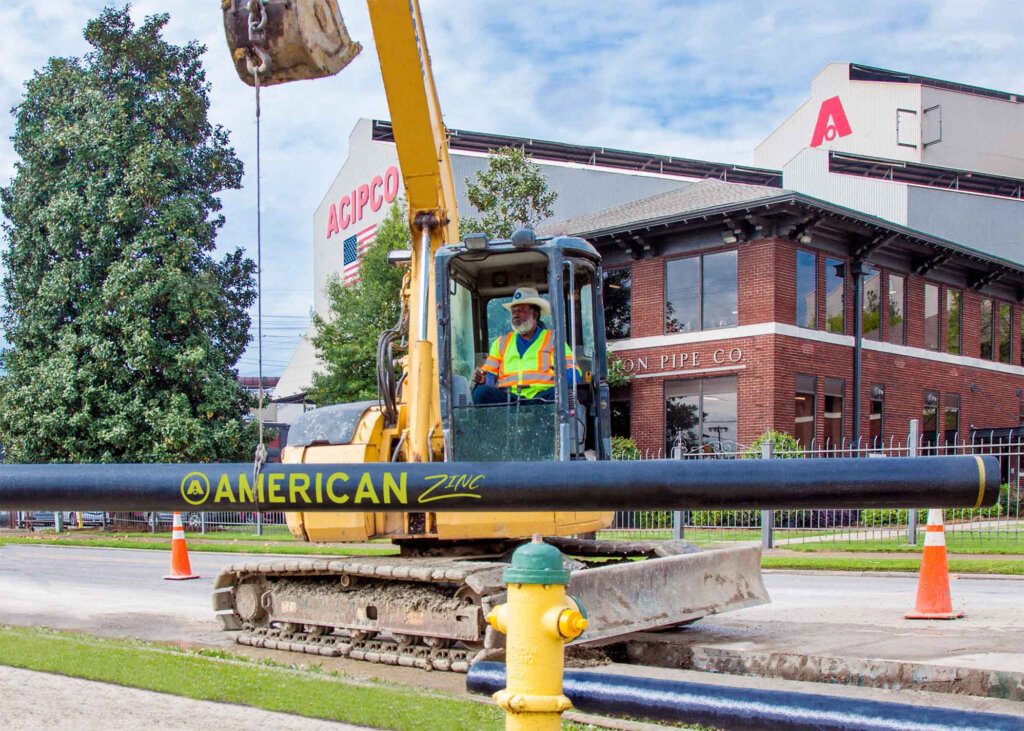
Founded in 1905 in Birmingham, American Cast Iron Pipe Co. manufactures valves, ductile iron pipe and fire hydrants for the waterworks industry, and electric-resistance steel pipe for the oil and natural gas industries. The company’s products are used around the world, often in high-profile projects.
For example, their pipes and hydrants delivered drinking water and provided fire protection in the 2015 expansion of the Panama Canal.
A new water reclamation facility in Jacksonville, Florida, used 53,000 feet of the company’s ductile iron pipe and its wedge gate valves.
In Guatemala, the company’s pipe installed above and below ground in the 1930s is still in service and meeting the needs of almost 3 million people in Guatemala City. In 2023, the water supplier there contacted the company for stock pipe for repairs in that earthquake-prone region.
The company employs about 1,600 people in Birmingham and 2,900 across the family of companies that includes American Ductile Iron Pipe, American Flow Control, American Spiralweld Pipe and American Steel Pipe.
More green news
In more good news for the environment, another Alabama company will receive financial support for a world-class electrical steel facility with reduced carbon emissions.
Steel producer AM/NS Calvert, co-owned by ArcelorMittal and Nippon Steel, is planning an advanced manufacturing facility that could deliver 150,000 metric tons of domestic production capacity of non-grain-oriented electrical steel each year.
The Internal Revenue Service has awarded the Calvert plant $280.5 million in investment tax credits as part of the Qualifying Advanced Energy Project. Construction of a new electric arc furnace is under way.
Non-grain-oriented electric steel (NOES) plays a key role in the performance of electric motors used to power electric vehicles and hybrids. The current domestic capacity of that steel is inadequate, leaders say, and this effort could help expand the supply and reduce dependency on imports.
Steel made using innovative processes uses less energy, emits significantly less carbon and reduces costs. Electrical steel is used in the cores of electromagnetic devices like motors and generators.
“Expanding U.S. NOES production will support the goal of having 50% of all new vehicle sales be electric by 2030,” says John Brett, CEO of ArcelorMittal North America.
ArcelorMittal is one of the world’s leading integrated steel and mining companies with a presence in 60 countries. ArcelorMittal sells its products to a diverse range of customers including the automotive, engineering, construction and machinery industries.
Deborah Storey is a Huntsville-based freelance contributor to Business Alabama.
This article appears in the June 2024 issue of Business Alabama.