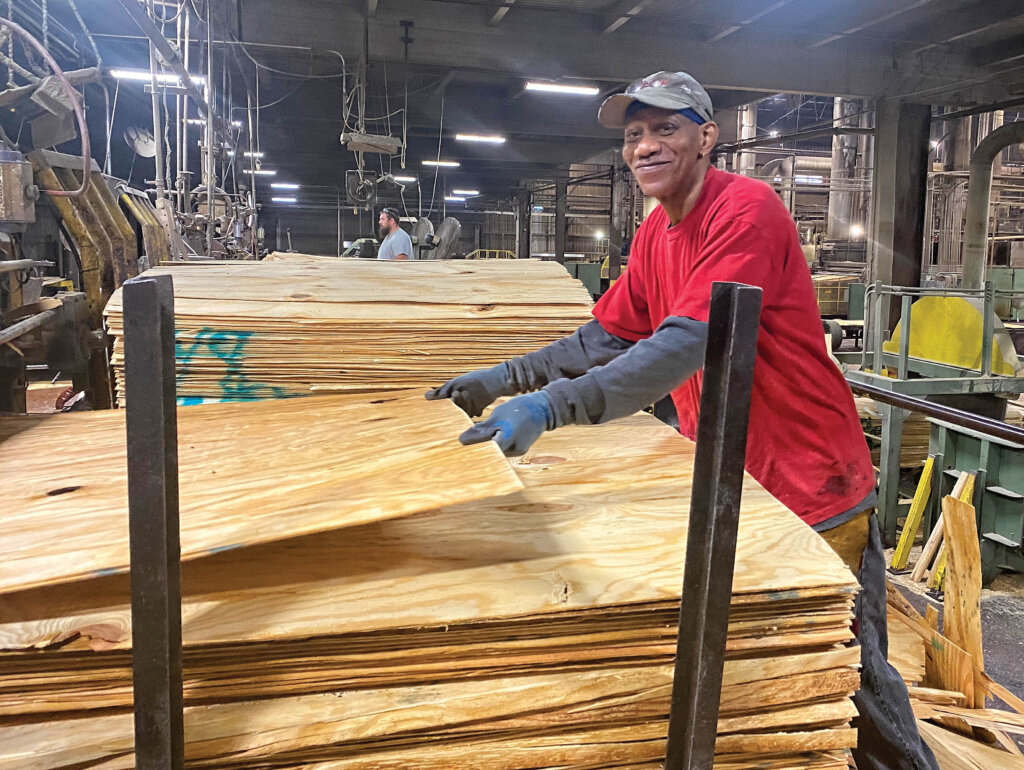
I’ve never seen anything like this during my career,” said Gray Skipper, vice president at Scotch Plywood.
The pandemic continues to take its toll on lives and livelihoods; families and finances; individuals and industries.
In fact, every aspect of the economy and business has been adversely affected by a labor shortage, plant and business shutdowns and a broken supply chain.
The construction industry has, itself, been impacted on several fronts — price spikes, supply chain issues, lack of labor, revenue, schedules.
Factories have shut down creating a scarcity of building supplies. The lack of workers and surplus stock has contributed to construction delays and pushed deadlines.
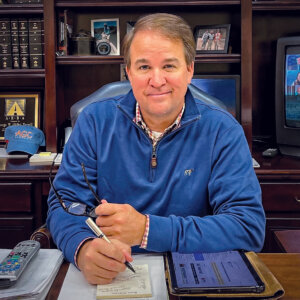
“Our industry is struggling mightily with the labor shortage,” says Billy Norrell, CEO of Alabama Associated General Contractors. “Every one of our guys has a sign on their mailbox that says ‘Apply Inside.’”
Construction companies must work within the time constraints of contract deadlines. Prices are set and budgets are settled.
But even the most-experienced contractors have never encountered this so-called “perfect storm” of pandemic-labor shortage-supply chain issues. While project managers plan ahead to make sure they have the materials, if a single item is delayed, that can be a potential disaster for the project.
“It’s squirrely how to predict trends down the road,” Norrell says.
“We try to lock down prices,” says Alex Whaley, of Whaley Construction in Troy. “We used to know what nails cost; what screws cost. Things you never dreamed of doubled overnight.”
By ordering the supplies earlier and purchasing them in bulk, some managers have been able to avoid shortages.
“When COVID hit, we realized there would be shortages,” says Michael Hendrickson, vice president of preconstruction and estimating for Birmingham-based Capstone Building Corp. “We did everything we can to secure the supply of materials.”
Meanwhile, double-digit price increases in building materials have appeared “overnight.”
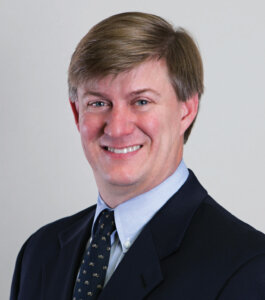
“You have to change your mentality in the way a contract is written,” Hendrickson says. “It’s difficult times across the board.
“In construction, you’ve always dealt with the same issues you have today — delivery, shipping. Today, though, the lead times are a lot longer.”
Another kink in the supply chain has been a shortage of truck drivers to transport products from manufacturers to the market. And it’s not just over-the-road deliveries; there have also been problems with the railways.
“Our main thing in the supply chain is getting products from our mill to the customer,” says Scotch’s Skipper. “The railroad has been horrible; there are hundreds of complaints from the South and Midwest.”
All in all, logistical bottlenecks have suddenly become the norm.
“There’s no way to see when the bottleneck will end,” Norrell says.
Skipper says his Clarke County-based company is having to deal with unprecedented demand from his customers, too.
“There have been very wild swings in demand … never seen before in our 50-plus years of existence,” he says. “Usually, in December, demand tails off but now we’re seeing an unprecedented demand.”
Companies are moving supplies and materials from site to site to avoid construction delays. Others are using warehouses to store materials in the event of shortages.
“We rented warehouse space to keep the employees on hand and business running,” Skipper says. “And we’ve emptied warehouse space. We’ve done this three times since April (2020).
“We’re in negotiations to purchase the warehouse we rented because we see a swing in demand over the next two years.”
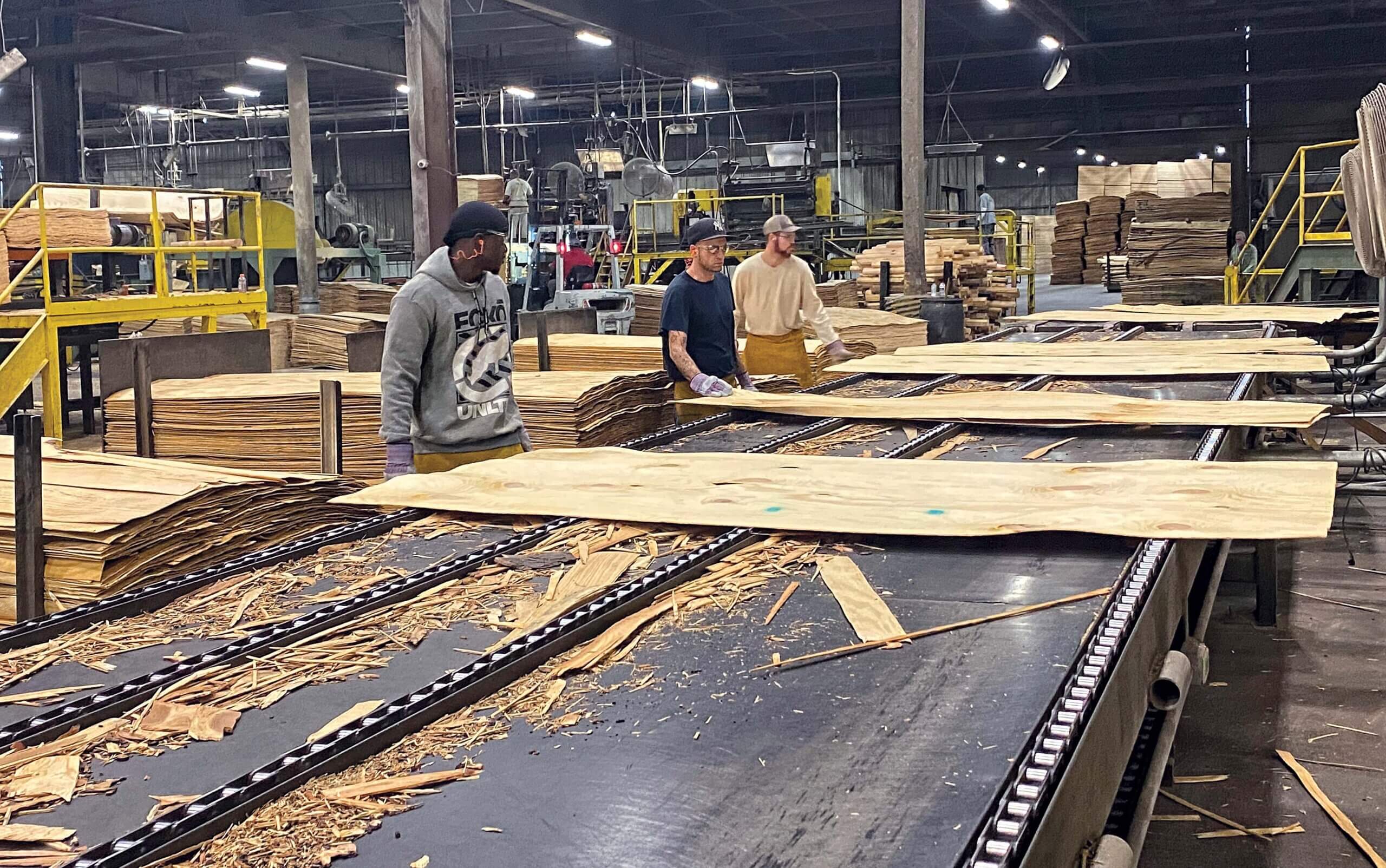
Contractors are no longer relying on just-in-time delivery, and materials that have been ordered ahead are taking up space on job sites. Carrying the inventory will increase costs and can create safety issues.
“The first reaction is to secure and obtain all the materials,” Hendrickson says. “The lender has to realize there will be a cost to that — you have to pay the owner for storage.
“You have to have a conversation with the owner.”
It’s just not a shortage of building supplies that is creating problems. Steel, which is used for buildings, is also used for appliances. And these appliances can be in short supply — be they washers, dryers, stoves.
This not only affects consumers but also creates problems for construction of multifamily residences and single-family houses.
“We’ve got manufacturing problems with appliances,” says Hendrickson, whose company only deals with the multifamily industry. “Some models are affected more than others.”
With the arrival of the Omicron strain, a return to lockdowns and shutdowns is probable. And it’s a situation that is concerning to everyone.
“I don’t know where it ends,” Whaley says.
“We are concerned about what the future will hold,” says Norrell. “It’s fortunate we have companies with innovative thinking.”
Bud McLaughlin is a Huntsville-based freelance contributor to Business Alabama.