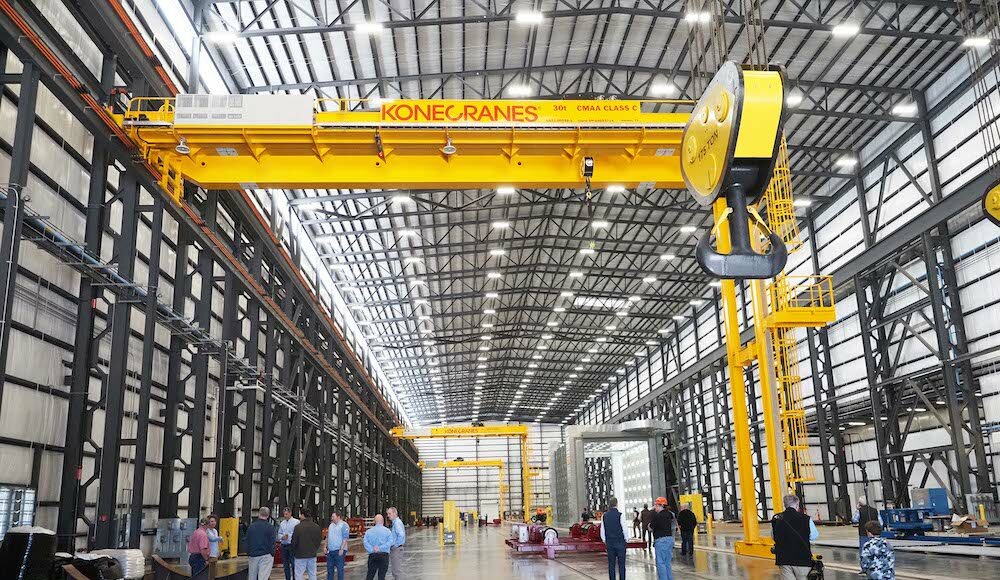
In 1992, brothers Charles and Arthur Holmes established a public holding company and named it by using part of each of their first names. Today, that company — Chart Industries — is literally bigger than ever, thanks to a new facility in Theodore.
Headquartered in Ball Ground, Georgia, approximately 50 miles north of Atlanta, Chart manufactures products that are used in every phase of the cryogenic liquid-gas supply chain, from small CO2 cylinders found in restaurants to massive cryogenic storage vessels used by the aerospace industry. The company, which has grown over the years organically and through acquisitions, currently has more than 11,500 employees with 64 global manufacturing sites and more than 50 repair sites globally.
But it is Chart’s newest facility on a 53-acre site in the town of Theodore, just south of Mobile, that is expected to make a big impact. Really big. From that location, the company is beginning production of the world’s largest shop-built cryogenic tanks, with a capacity reaching 1,700 cubic meters, or nearly 450,000 gallons. The tanks will be up to 150 feet long and 26 feet in diameter, a size that Chart officials have given the non-technical moniker of “jumbo.”
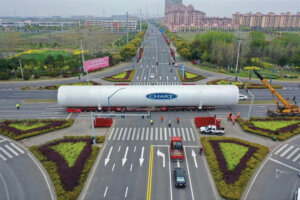
“We build 1,000 cubic meter tanks at our facility in New Prague (Minnesota), but these are 70 percent bigger,” says Bob Knight, who served as the project manager for construction of the new Theodore facility. “The size and weight of these vessels is just massive.”
Chart already had been operating in Theodore out of a facility used to manufacture hydrogen trailers. In 2022, the company began exploring the possibility of building another facility in the area because of increased demand for these types of large cryogenic storage vessels.
“A lot of these are going into the aerospace industry for propellant storage,” Knight says. “Also hydrogen and LNG (liquefied natural gas) storage for power, marine, science and decarbonization industries.”
Knight says the location of the new facility — dubbed “Teddy 2” because it is the company’s second in Theodore — is ideal for the production of these tanks because of easy access to both a rail line and nearby Mobile Bay.
“The piece of property that we found suited us perfectly,” Knight says. “We bought it from Southern Concrete Products, so there already were some buildings on site. It’s right on the canal, which is important because these tanks are way too big to be trucked.
“Part of this project is building a large ramp that leads to the canal, so we can move these tanks directly from the production facility and load them on a barge. From there they float through the canal into Mobile Bay and then to places all around the U.S.
“There also is a CSX rail line through the front of the property, and we’re building an additional rail spur. Because not only are we going to make these very large storage vessels, we’re also going to make a variety of others.”
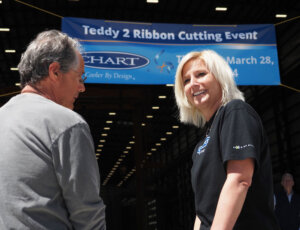
Chart broke ground on the new facility in April, 2023, with Brasfield & Gorrie serving as general contractor. The company invested $7.2 million in improvements to the onsite wharf, and Knight says it took nine major pours of concrete into the ground to establish a foundation capable of supporting the weight of the tanks.
But creating the production facility itself was relatively easy compared to the task ahead when it comes to actually constructing the massive storge tanks.
“The inner vessel is stainless steel and the outer vessel is carbon steel,” Knight says. “You have these large plates that have to be rolled into a cylinder. All those cylinders are welded together to form the tubes for the outer and inner vessel.
“It’s just such a challenge working on something that big. You have a shell that’s 26 feet in diameter. Everything is so big and so heavy, making it a relatively slow process. Everything requires a piece of equipment to pick it up.”
The effort is worth it to Chart, because Knight says there is a strong demand for tanks of this size. He says before it even opened its doors, the “Teddy 2” plant already faced a backlog of production orders.
“For some of these uses, like aerospace, it requires a tremendous amount of fuel and gas,” Knight says. “You could have multiples of smaller tanks, but then you might have 20 trailers lined up to unload, and that can be impractical. So, they like to store as much as possible in one big tank to make the transfer and logistics a little easier.”
Cary Estes and Mike Kittrell are freelance contributors to Business Alabama. Estes is based in Birmingham and Kittrell in Mobile.
This article appears in the June 2024 issue of Business Alabama.