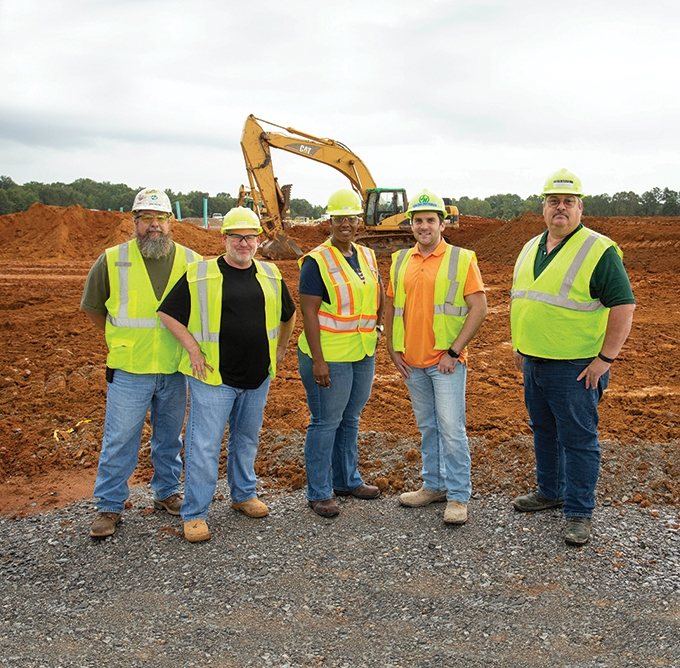
Back in the 1980s, James Hardie Building Products, an international enterprise based in Australia, pioneered the current fiber-cement technology for home siding and trim boards. The company has since marketed its line as a durable, low-maintenance alternative to wood and vinyl for both residential homes and multifamily apartment buildings.
Today James Hardie has operations in North America, Australia, New Zealand, Europe and the Philippines and $1.92 billion in net sales for 2017. Now it is building its 10th U.S. factory in Prattville, a small city just northwest of Montgomery. James Hardie will spend up to $220 million to build a 750,000-square-foot factory on 103 acres in Prattville’s South Industrial Park and eventually hire more than 200 people, says James Hardie’s Sean Gadd, the executive vice president of products and segments.
“The region is a strong region for James Hardie,” says Gadd, adding that the new plant will enhance the company’s ability to target markets in the Southeast.
“The Southeast has been growing quite significantly,” he says. “This will now put a plant right in the middle where it will cover the areas east of Texas and west of Florida. So it makes a lot of sense for us to put added capacity in the region.”
In addition to its HardiePlank siding products, the Prattville plant is also expected to manufacture James Hardie’s new line, the Aspyre Collection from James Hardie™. The upscale line gives homes a “historic wood” look, seen on classic Victorian, colonial and Craftsman style homes, Gadd says.
“As the Prattville plant ramps up, we’ll continue to add other products as needed in the region,” he says. “The capability of the plant will enable us to do a lot of different things if we need to do it.”
Construction on the Prattville plant will be complete by early 2019 with production to start by spring, he says.
Choosing Alabama
James Hardie has been in business for more than 125 years. The company has approximately 3,500 employees worldwide, the majority of whom, some 2,390, are in North America, according to the company’s 2017 annual report.
James Hardie sells its products, including HardiePlank® lap siding, HardieTrim® boards and HardieBacker® cement boards, primarily to wholesalers and distributors, Gadd says. The wholesalers and distributors then sell those products to builders for new residential construction, manufactured housing and light commercial applications, as well as to remodeling contractors and do-it-yourselfers through retail building supply chains.
The company scouted the South for many months looking for possible locations for the new plant site, he says, considering locations in Tennessee, Louisiana, Mississippi, Georgia and Arkansas before settling on Alabama.
“When we got down to the Alabama market,” he says, “we looked at Huntsville, Birmingham, Montgomery and Alabaster. In the end, we picked the site based on a number of factors.”
Those factors included ease of access to high quality raw materials such as sand and cement, sourced locally to help keep the company’s freight costs down, he says. They also wanted a reliable water source. In this case, the water will come from the Prattville Water Works. In addition, James Hardie uses a specialty grade of cellulose pulp — the “fiber” in fiber cement — but the company ships that material into the United States from Chile and Canada.
“We also look for good freight lanes to get products out of the plant to service the markets,” he says. “We look for highway systems and rail access throughout the vicinity. When you put all of that together, Prattville came up as one of the better options.”
But in addition to raw materials and infrastructure, Gadd says James Hardie also considered the availability of a skilled workforce in the Prattville area. The company plans to hire electricians, mechanics, plant managers and workers who can operate its specialized, state-of-the-art manufacturing equipment. Moreover, the company will prepare new hires through its own in-house training program.
“We’ve learned through the years the type of workforce we look for,” says Gadd. “We like people who are willing to be trained. We like people who want to stay in the area and want a consistent job. We look for people who want to come in and make a difference every day. So work ethic is really important for us.”
Once the plant reaches full production, it will operate 24 hours a day with two, 12-hour shifts and a capacity to produce up to 600 million standard feet of product annually, Gadd says.
The Production Process
To make the fiber-cement siding and trim boards, says Gadd, James Hardie ships sand, cellulose pulp and cement into its factories by railway and truck. Production begins with the “Hatschek Process,” where sand, pulp and cement are mixed together with water. Once this slurry mixture is the right consistency, it is pumped to a Hatschek machine, which is similar to a paper machine. There, the slurry is deposited onto a moving felt and de-watered, pressed and cut into sheets of the desired length and thickness.
These sheets are then inspected, stacked and placed in a pressurized autoclave.
Afterward, the sheets are unstacked and finished, using precision coating equipment, before they are packaged for shipment by rail or truck.
Economic Impact
Amy Brabham, the economic director for the Prattville Area Chamber of Commerce, says that within the manufacturing sector, the new James Hardie plant will be the largest industrial development project in the Prattville area since a container board mill, now run by International Paper, moved to the city more than a half century ago.
“If we ran the numbers today from what we know,” says Brabham, “we would see well over $1 billion of [economic] impact, and, for years on end, [James Hardie] will create jobs and transform the entire industrial park in the community, much like International Paper has over time.”
In fact, James Hardie’s investment in Prattville will likely have an enormous residual effect throughout the entire community, she says. Even now, other suppliers and related companies are eyeing the area for potential locations.
“We also have other retail and commercial operations that are coming to town because of the increase of permanent jobs in the community in the manufacturing sector,” she says. “The beauty of the permanent increase in manufacturing jobs is that it increases everything across the board in the community.”
To help facilitate the plant’s construction, Prattville has partnered with Autauga County to fund a new access road and bridge connecting Autauga County Road 4 with U.S. Highway 82, she says. The total cost will reach approximately $6 million. Federal funds from the U.S. Economic Development Administration, however, will cover part of the cost.
Utilities will add sewer, gas and electric lines, and AIDT will assist with the plant’s hiring process, Brabham says.
Hiring will begin in early 2019.
“We’ve had many inquiries about those jobs,” she says.
People have also contacted James Hardie directly about employment in Prattville, Gadd says. “We’ve been getting inquiries since the day of the announcement,” he says. “There’s a lot of excitement locally and in the region, which is great.
“The people of Alabama have been extremely helpful and friendly in terms of helping us get the site picked and started,” says Gadd, “and we look forward to a fantastic partnership with the city of Prattville and the state of Alabama.”
Gail Allyn Short and Robert Fouts are freelance contributors to Business Alabama. She is based in Birmingham and he in Montgomery.