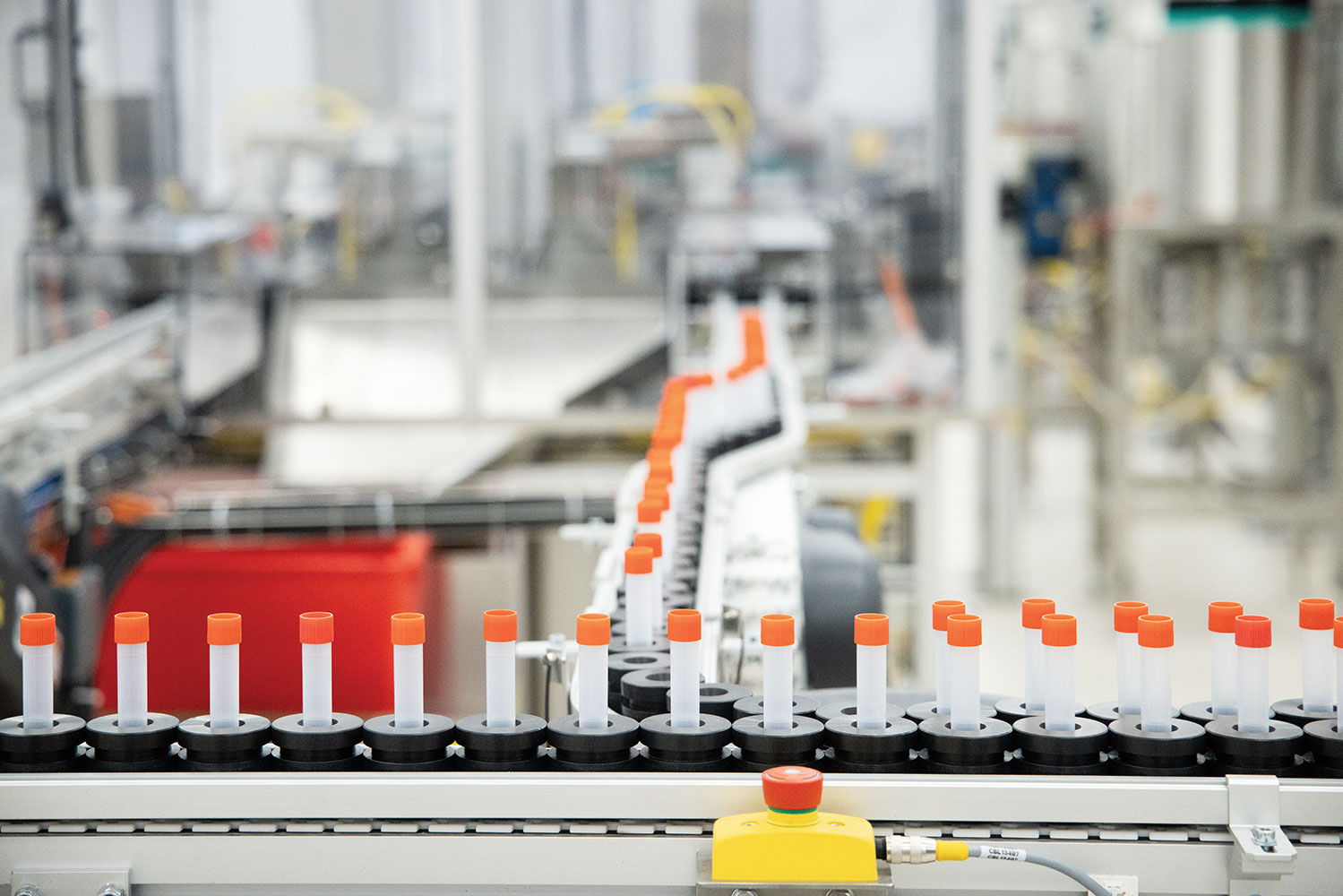
This story appears in the April 2021 issue of Business Alabama magazine
As Alabamians and others continue to receive COVID-19 vaccines, we can be thankful in part for vaccine container vials developed and manufactured by Auburn-based Operation Warp Speed success story SiO2 Materials Science.
The advanced materials science company, privately owned through a 110-year Abrams family legacy of business and innovation, fortuitously had created a revolutionary biomedical material just prior to the pandemic. That material, a specially formulated polymer formed and then coated inside with several microscopic, glass-like layers, is perfect for safe and effective vaccine dissemination, a vast improvement over traditional glass vial delivery systems, says Lawrence Ganti, SiO2 president and chief business officer. “The creation of the material in time to be scalable to support mass vaccination was an extremely lucky thing for us all,” he says.
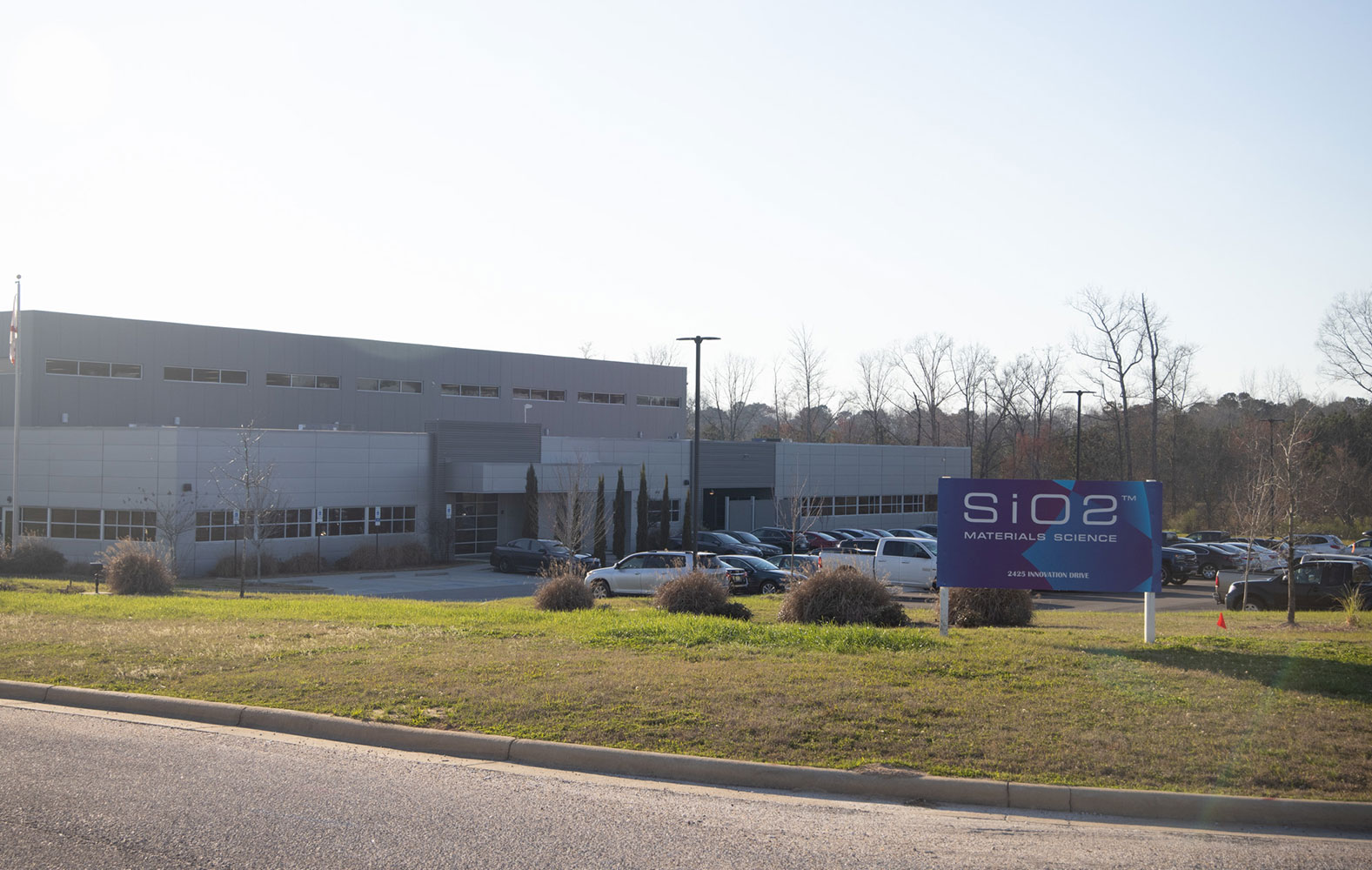
Combining the best qualities of plastic and glass, the new material provides improved thermal and chemical stability, as well as a better gas barrier, mechanical durability and precision molding than either material alone, according to SiO2. Vials made of the material can be used in storage conditions from -196 ºC to 121 ºC, can withstand 1,500 pounds of direct force and are shatterproof. The advanced technology used to create the inert vials includes a proprietary process using a plasma-enhanced chemical vapor to deposit each vial’s interior coating.
One of the stand-out companies chosen for the national COVID-19 vaccine rapid deployment, SiO2 received a $143 million federal grant, announced last June, to help ramp up its workforce from 150 to 500 employees and its manufacturing space from 180,000 to 350,000 square feet. “We have always had great cooperation from local government but with the additional Warp Speed support, we were off to the races,” Ganti says.
“When you have the Defense Production Act behind you, your needs (for construction, materials, etc.) are given first priority.”
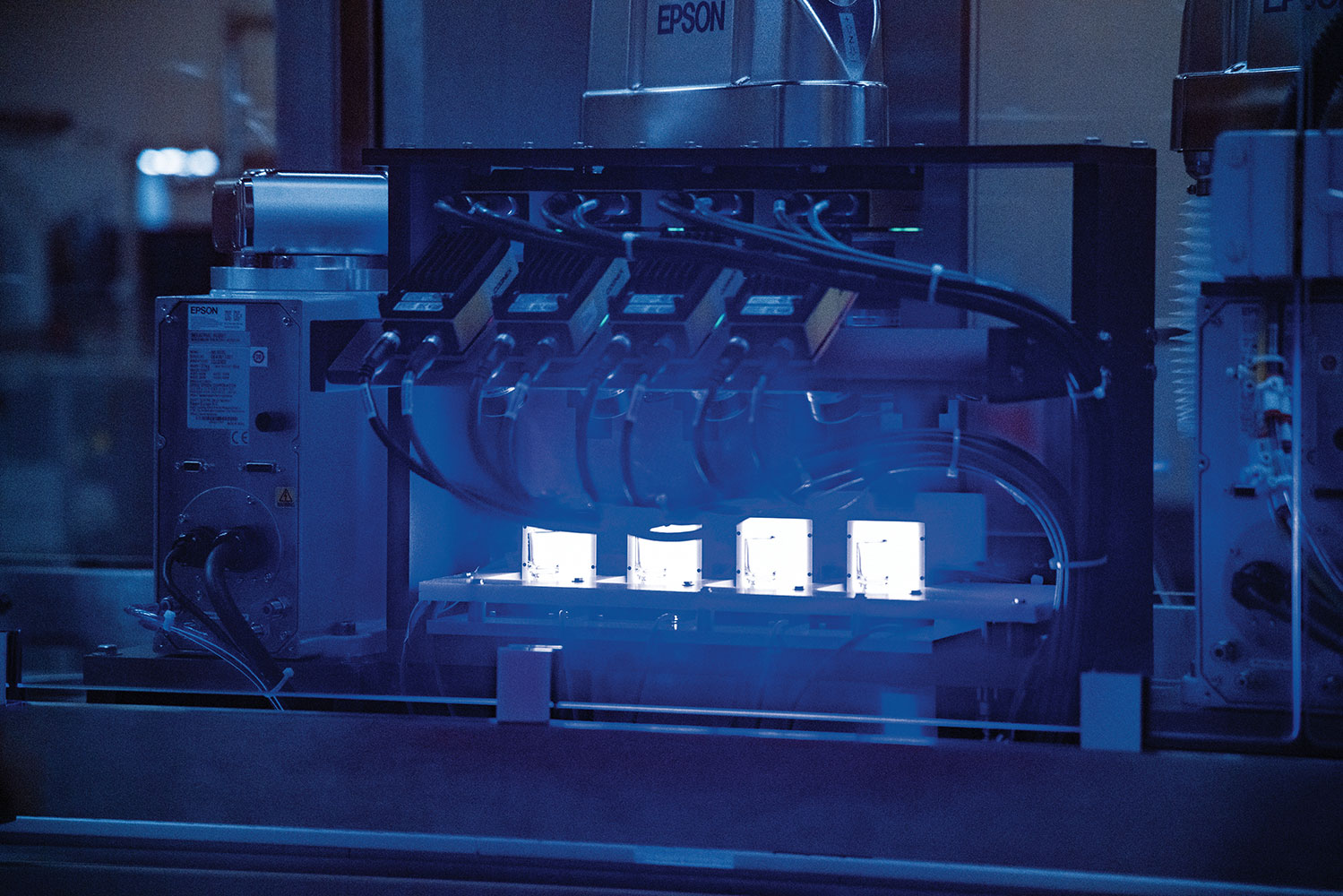
SiO2 announced in July, only a month later, it had scaled its vial manufacturing capacity to 400 million doses and expected to hit a 1.2 billion capacity before the end of 2020, in part thanks to an additional investment of $160 million by the company itself. “The company knew how critical these vials are to helping address the pandemic,” Ganti says.
Developing the advanced material used for the lifesaving COVID-19 vaccine vials was made possible by a multi-year $500 million SiO2 investment. The material’s almost decade-long development process kicked off with a renaming of the Abrams family company and its relocation to Auburn, where it was attracted by the university’s talent and resources. “If you look at the full heritage of the company, SiO2 has had roots in Alabama for about 25 or 30 years,” Ganti says.
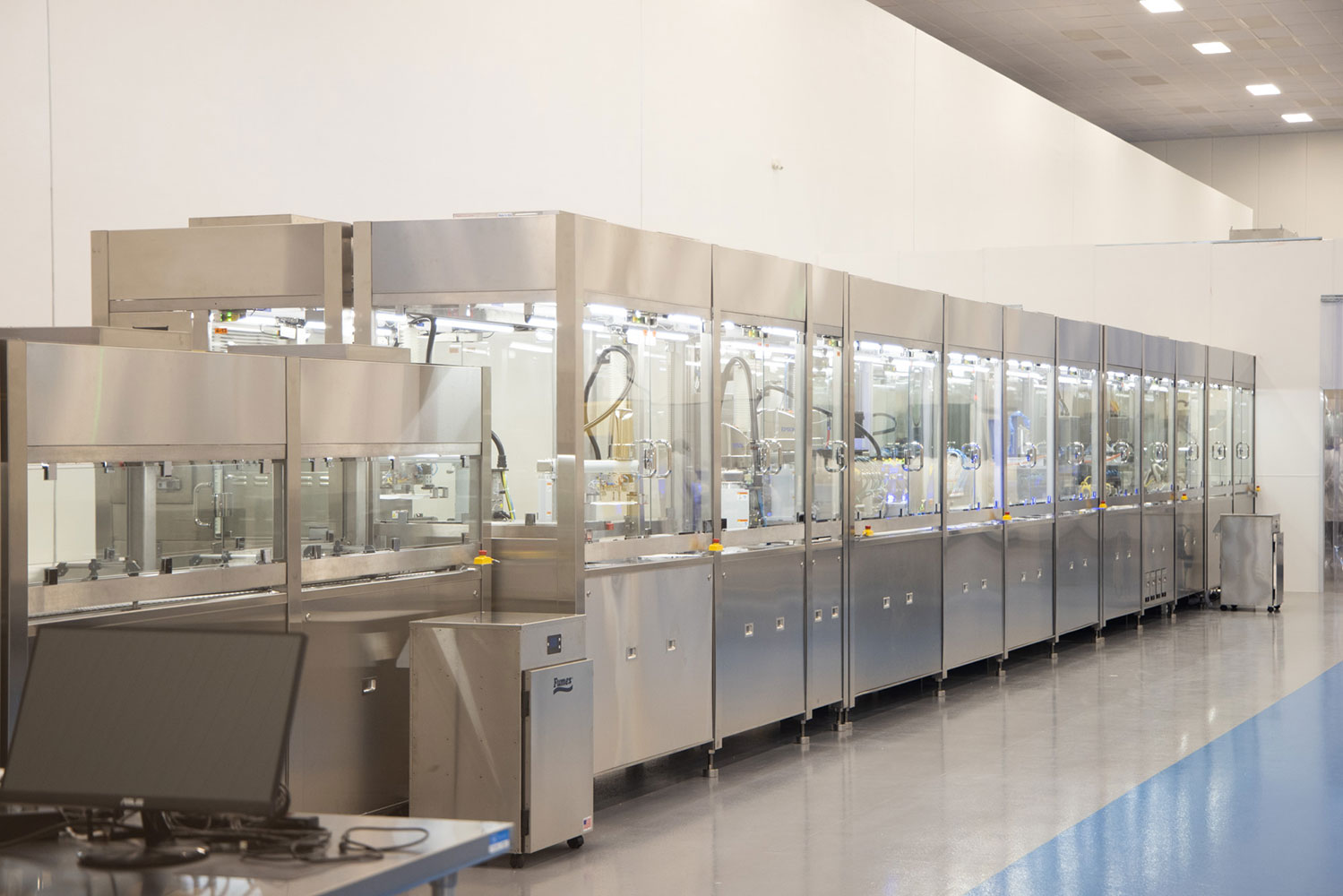
The genesis of the advanced material’s development came from a 2012 request from Children’s Hospital at Stanford University, where a number of premature babies were dying each year because of reactions to tiny particles found in traditional glass syringes and medicine vials.
Bobby Abrams, founder and chief executive officer of SiO2, enlisted the help of scientists from four major research institutions across the country to contribute to the development of the revolutionary material and proprietary coating technology. It not only solves the problem of toxic particles but also dozens of other limitations that plague traditional glass and plastic delivery systems. The advanced material has multiple applications over a number of industries, including but not limited to pharmaceutical, molecular diagnostics and health and beauty.
One of the company’s early products using the new material, officially launched in December 2019, was the Synergy Tube, an extraordinary blood collection tube designed to optimize nucleic acid recovery and cancer tumor cells from the point of blood draw. It was SiO2’s first genetic diagnostics product on the market.

“The Abrams family has made many contributions to advanced materials innovations over the years,” Ganti says. “The company brought me in early 2020 to help commercialize its latest developments. The emphasis at the time was production of pre-filled syringes made from the company’s new material, but then suddenly we needed to pivot to accommodate scaling up our vial production for COVID-19.”
Ganti’s background includes work for major pharmaceutical companies, including an 11-year tenure with Merck, which was desirable for his current role. But Ganti also has significant international business experience. He says that experience helped him learn to be highly adaptable to uncertain situations and changing needs. “When I was hired by SiO2, I don’t think any of us realized how much that would help in responding to the pandemic,” Ganti says.
But the COVID-19 vaccine vial push is not all that’s on Ganti’s plate. The long-range vision for the company is not to have excess production capacity as needs for COVID-19 vials winds down, but instead to expand its customer base to create continuing high demand for its products, Ganti says. SiO2 primarily supplies major pharmaceutical and other companies that have global distribution networks. “We are pursuing various markets, but with the commitment to supply the emergency needs of our country first,” he says. “Before we developed our vials, 90% of the vials produced were manufactured outside the United States, which was concerning.”
During the 1950s, CEO Bobby Abrams took the helm of his family’s company, which Mauri Abrams originated in 1910 as an upstate New York accounting firm, Ganti says. The younger Abrams created what was to become one of the largest dairy companies in the nation and providing the dairy industry with numerous innovations, including the first integrated plastic milk jug and the first resealable milk carton spout. “The original family company evolved greatly over time,” Ganti says.
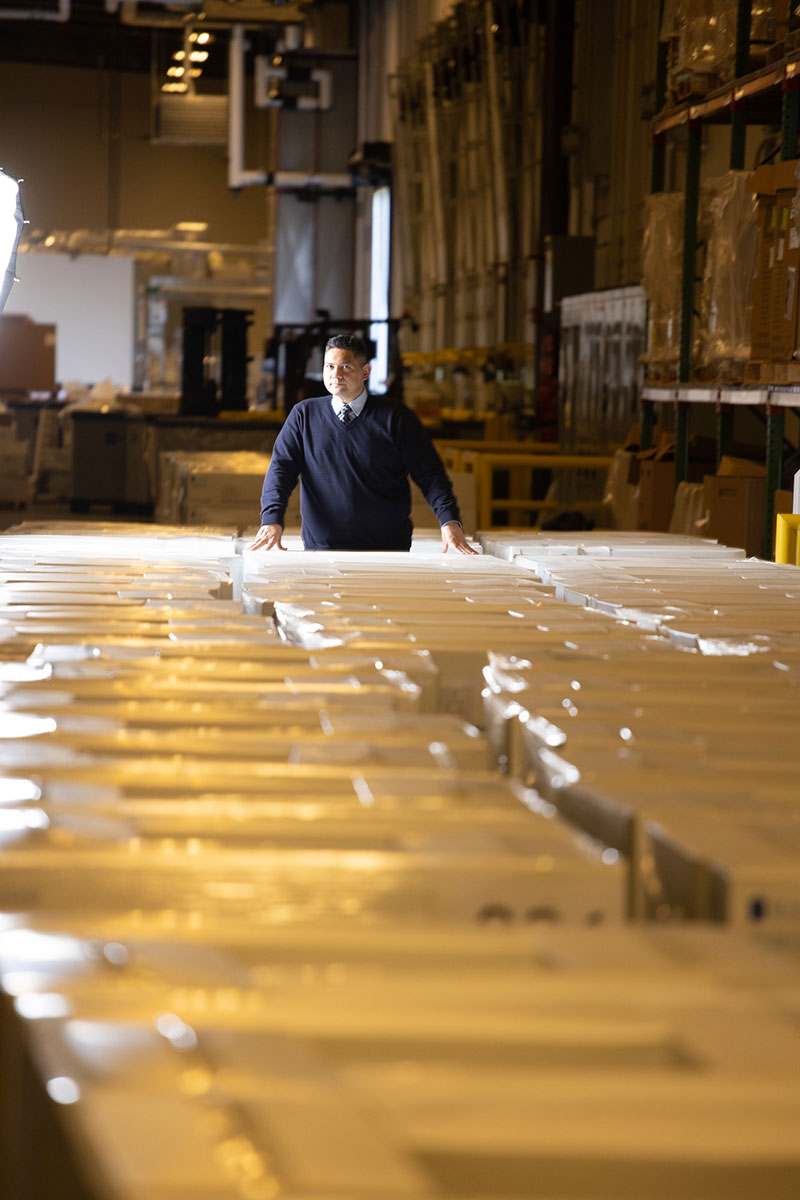
After he began growing the company’s dairy interests, Abrams focused on inventing a number of molded plastic containers, including the desiccated plastic vial for diabetic strips, the infant sippy cup and airtight vials for drugs for abuse testing. The innovations he led provided revolutionary packaging for companies including M&M Mars, Johnson & Johnson, Abbott Laboratories, Roche Diagnostics, Glaxo Smith Kline and governmental agencies across the world associated with athletic drug testing and national dairy boards.
Over the decades Abrams and his company have produced more than 3 billion custom container units for M&M Mars and more than 10 billion custom container units for Johnson & Johnson, Roche, Abbott and Bayer. Abrams holds 100 of the company’s 300 patents for new coatings, treatments and methods of manufacturing.
“The company has a long heritage of innovation and contribution, and we want to keep providing advanced materials that solve the unique problems of our customers,” Ganti says. “The Auburn area continues to be a great location for us.”