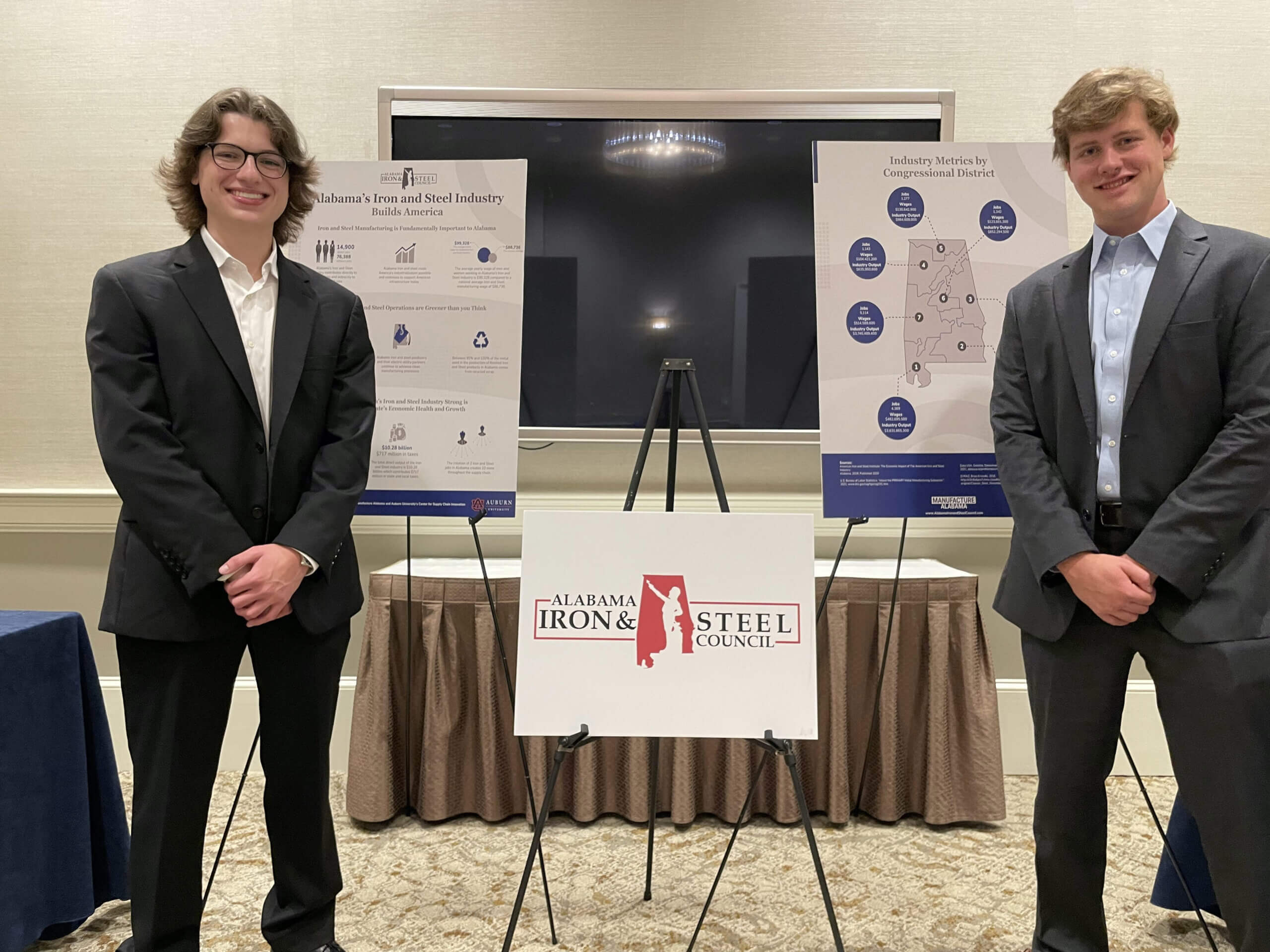
Auburn University’s Harbert College of Business recently studied Alabama’s iron and steel industry with an initial goal of determining its economic impact, but instead found a greener, cleaner, high-tech producer key not only to Alabama’s economy but to America’s as well.
The study, a partnership between Manufacturing Alabama and Auburn’s Harbert School of Business Center for Supply Chain Innovation, found that the industrywide average annual salary in Alabama is almost $100,000, including both skilled and unskilled labor; that producers have upgraded to engineering and production methods that have exhaust stacks emitting harmless steam and much less carbon dioxide; that it uses recycled materials to produce new iron and steel; and that it contributes to other industries such as shipbuilders and critical infrastructure suppliers.
“The initial project was an economic impact study on the iron and steel industry in Alabama, but what it turned into was a document for the current government and the public to realize the tremendous influence of iron and steel production in the state,” said Grant Stallworth, an Auburn senior in supply chain management who played a lead role in the study.
That influence includes almost 15,000 direct jobs and more than 76,000 indirect jobs. The report also stated that the industry “supports Alabama families by paying $1.48 billion in direct wages and $4.68 billion in indirect wages that are directly traceable to the support of iron and steel manufacturing.” Indirect jobs include suppliers and consultants to retail services, such as convenience stores and restaurants that move into an area directly serving iron and steel workers.
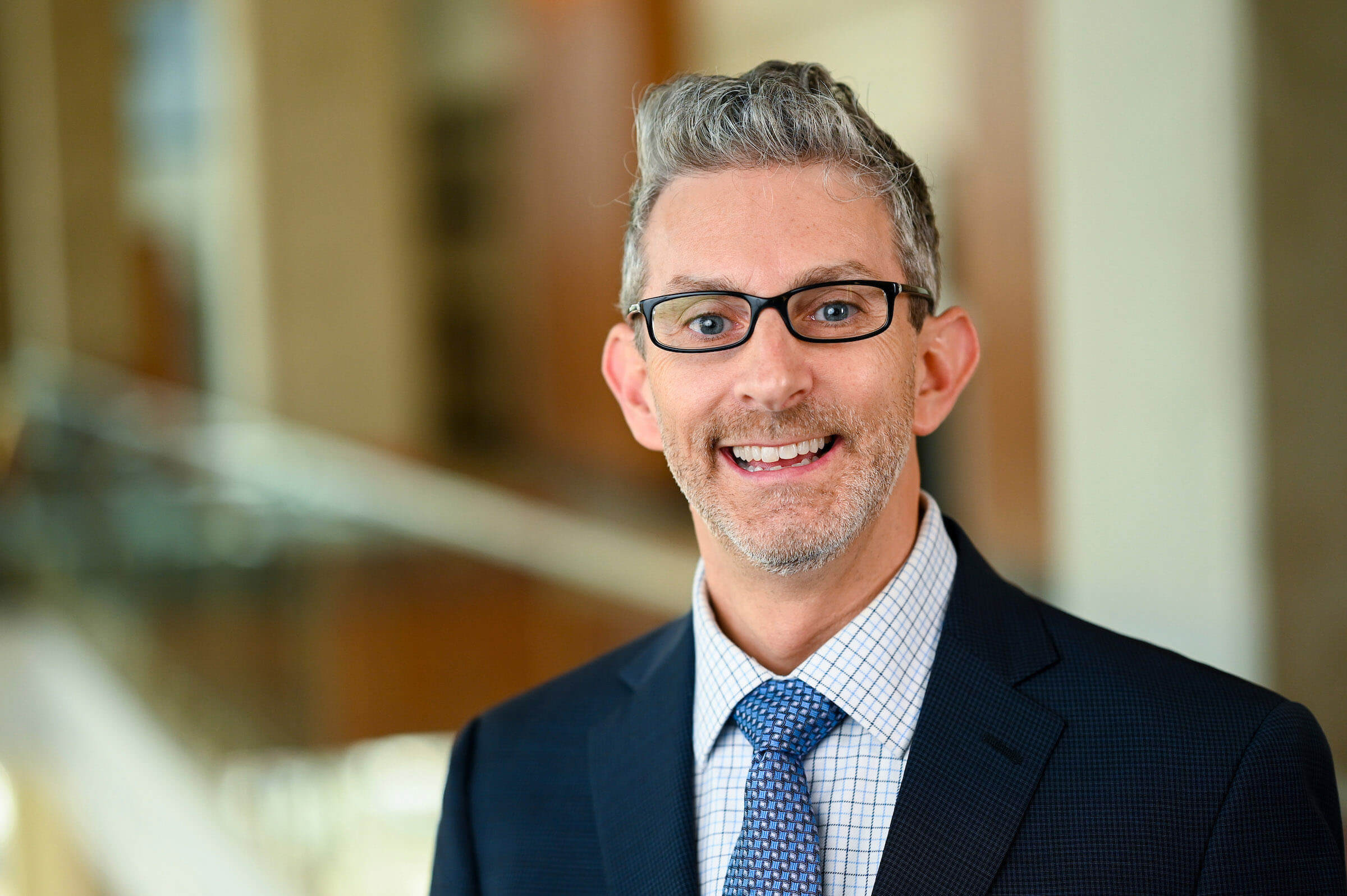
New technological advances in the production process, as well as a need for efficient managers, have changed the look of the industry from unskilled, heavy lifting labor to skilled, educated work. Another factor is the longevity of the workforce.
“People seem to stay there forever, like 40 or 50 years,” said Erik Sjolseth, an instructor in the Department of Supply Chain Management in Auburn’s Harbert College of Business who supervised the project.
Perhaps the most surprising to the researchers was learning of the advancements the industry has undergone — becoming a major recycler. For example, steel is now being made through electric arc furnaces. “The EAF is great for recycling iron and steel,” said Stallworth.
“Between 95% and 100% of the metal used in the production of finished iron and steel products in Alabama comes from recycled scrap,” the study reported. In addition, the process is cleaner, producing significantly less carbon dioxide than traditional melt sources.
One of the people not surprised by the report was Alabama Secretary of Commerce Greg Canfield, who said, “Alabama’s iron foundries and steel mills acted as a catalyst in the industrialization of the state’s economy going back more than a century, and the industry continues to be an important employer in communities across the state, supporting jobs that pay far above average wages. Today, the iron and steel industry in Alabama remains committed to growth, thanks to new investments that will increase production through processes that are sustainable and more environmentally positive.”