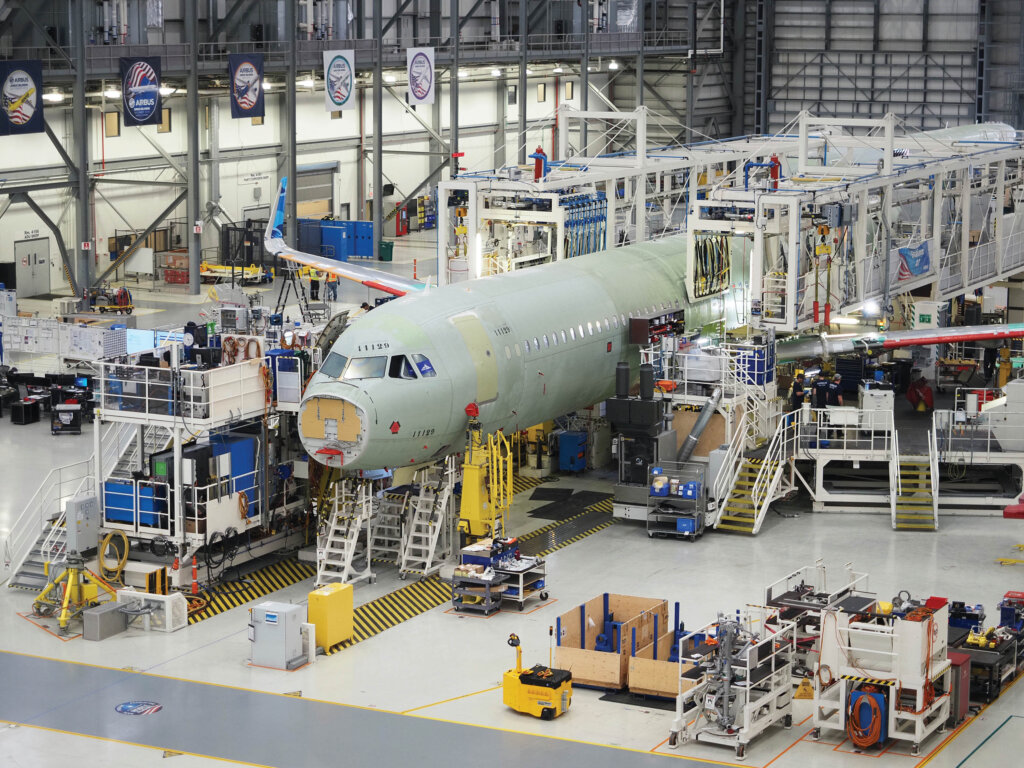
There are only three basic concerns at Airbus in Mobile these days beyond making the popular A320/321 and A220 jets its known for — build additional facilities that more than double the company’s footprint here; equip them with all the required jigs and tools for a major manufacturing program; and find another 1,200 or more employees when the state’s at nearly full employment.
All in a time of snarled supply chains and inflationary increases to costs.
But Daryl Taylor is upbeat about it.
“We are blessed to have certainly the most successful commercial aircraft in history,” says Taylor, who is vice president and general manager of Airbus’ Final Assembly Line USA.
The worldwide company has an order backlog for more than 6,000 of the single-aisle A320/321 aircraft. Globally, the company has been producing 64 aircraft a month. In an earnings call with investors in April, CEO Guillaume Faury announced plans to increase the rate to 75 a month by 2025 or 2026.
And that meant changes at the company’s facilities.
In Mobile, it means new paint shops, new final phase flight line hangars, and a third final assembly line — big projects for a rapidly growing presence in Mobile.
Just 10 years ago, Airbus officials announced plans to have any plane-making presence in Mobile. There had been an engineering facility here for a while and a helicopter support center. But joining the ranks of cities actually making commercial jets was such big news that city officials threw a party at the Convention Center.
Since the April word from global headquarters, the Mobile facility has already appointed a project manager — HPM, which superintended the first two FAL projects. Contracts have been awarded for the paint shops and hangars. Ground is being turned and a construction village is taking shape. Workshops have been offered for local companies that might like to be considered for various elements of the project.
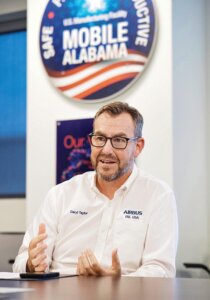
“We will almost double the footprint of what we have in Mobile today to accommodate the growth,” Taylor says.
The first pieces should be done next year, with the FAL opening in 2025.
While supply chain issues could disrupt plans, Taylor says the aircraft maker was aware of problems when it set schedules.
“From a construction point of view, we’re seeing the strain on the system — delays in the steel market and in the mechanical equipment — but we’re not seeing that we can’t get them,” says Taylor. “We’ve accommodated that in our timeline. That’s why we’ve started building as quickly as we have. What might have taken us 12 months to build a building previously, it’s going to be more like 15 months this time. And we’ve accommodated that in our detailed planning from Day 1.”
Jigs and tools — the equipment needed to assemble an aircraft — are in the same situation. “The good news — most of this has been built before. We’re not designing anything significantly new,” Taylor says. “We’re in the middle of finalizing a new FAL in our Toulouse facility so we’re able to take lessons learned there. We recognize that the timeline to build some of these new tools is longer than it was before, so all of that is built into the project timeline.
“In a company the scale of Airbus, while we might not always be putting new jigs and tools into Mobile, we are putting them into Hamburg, Toulouse, Tianjin, our facilities in Canada, Germany — we have a pretty mature organization that’s capable of doing this; we have a very mature supply chain.”
People are the final element needed. Right now, the company employs just more than 1,400 workers. By the time the third FAL opens, it will need another 1,000, perhaps as many as 1,300.
Three new programs have been instituted to attract more workers.
First is an apprenticeship program in partnership with Bishop State Community College. Taylor, who started his career with an apprenticeship at the Airbus wing facility in Broughton in the UK, is a firm believer in the power of apprenticeship to develop workers. The 45 students in the program that started this year spend several months in Bishop State classes learning the basics in a program called Flight Path 9, then spend three months in classes developed for Airbus by the state’s AIDT program, and then 12 months on the shop floor rotating through a variety of workstations.
The firm has also created a new program, Airbus On Board, which offers people with five years of work experience in any field a chance to be retrained for aerospace work. The first class of 50 is in progress now, with plans to offer the program twice a year going forward.
Finally, Airbus has created Airbus Global Graduate Program, bringing new college graduates to the team. The first cohort has four people, but plans call for increasing it to 20 or 30.
“We’re trying to create a mix of developing our own talent and hiring,” says Taylor. Hiring 1,200 people simply by tapping the market would not be feasible, he says. But if Airbus can find two thirds of its needed personnel through its own training programs and connections with nearby universities, the task becomes more manageable.
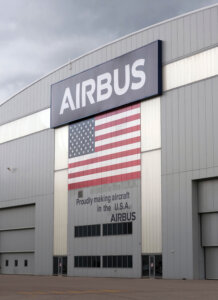
With all the need for growth, why Mobile?
U.S. customers like the option of U.S.-built planes, he says. Delta, American, Frontier, Spirit and United (which is waiting for the A321XLR) all appreciate the convenience of picking up new planes here rather than in Europe.
Since opening in 2015, Airbus Mobile has delivered 300 A320/321 aircraft. The demand is also growing for the A220 craft, made in Mobile and in Mirabel, Canada. Delta, JetBlue, Air France and KLM have been adding the smaller jet to their fleets and startup Breeze Airways has built its entire business plan around the A220. The excellent Bombardier design coupled with Airbus expertise supporting commercial aircraft are leading to an exponential growth in sales, Taylor says.
More than that, Mobile has offered Airbus an unusual degree of support. City, county and state officials have stood alongside business leaders to welcome Airbus, support its plans nationally and help it succeed.
That alignment for support, says Taylor: “That’s the magic source that happens in Alabama that doesn’t happen elsewhere.”
Nedra Bloom is writer/editor for Business Alabama and Mike Kittrell is a freelance contributor. Both are based in Mobile.
This article appears in the October 2022 issue of Business Alabama.