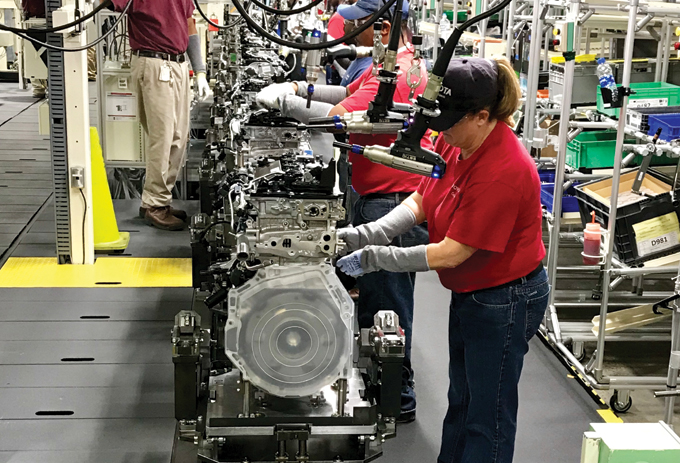
As the state’s automotive manufacturers and automotive supplier companies have rapidly expanded in recent years and their work has become increasingly high-tech, the industry has consistently faced challenges in recruiting and retaining enough qualified workers.
Almost 40,000 employees work in Alabama’s automotive manufacturing sector, and now, with Mazda Toyota Manufacturing USA constructing a new, $1.6 billion joint venture assembly plant in Huntsville, the state’s need for qualified automotive workers will intensify. Construction is set to begin in 2019, and the facility will employ at least 4,000 workers, with an annual production capacity of 300,000 vehicles, says Ed Castile, deputy secretary of the Alabama Department of Commerce and director of the state’s worker training agency, AIDT (Alabama Industrial Development and Training).
“The company has said they will need 4,000 people, so we’re planning for that, but in many cases, Japanese companies are conservative on their numbers, so it could be even more,” Castile says. “Before construction even began, we were laying out a process for how we’ll recruit workers and the skills that will be needed.”
Training automotive workers has been an ongoing project for AIDT and its partners since Mercedes-Benz announced it would build its first U.S. plant in Alabama more than 25 years ago. But the demand for 4,000 skilled automotive workers at Mazda Toyota, as well as expanding workforce needs at Mercedes and other Alabama-based auto manufacturers, adds urgency to the task.
Because Alabama has a history of success in recruiting and preparing an adequate workforce, business and governmental leaders say they’re ready to face the challenge. “Toyota Manufacturing [which already operates an engine plant in Madison County] had a great deal of comfort when selecting this site because of their 15-year history in our area with the engine plant,” says Chip Cherry, president and CEO of the Huntsville/Madison County Chamber of Commerce. “They’ve done five expansions, and AIDT was there to help with workforce needs each time. Also, we have a long history of being able to generate a long list of people to interview.”
Neither the city of Huntsville, Madison County nor the state of Alabama made any guarantees regarding the number of workers that could be secured for the new Mazda Toyota plant. However, “we did guarantee that we’d be available to help as much as possible,” Cherry says.
Harnessing Existing Workforce
While more workers are needed to fully staff the new plant, state leaders are quick to point out that a tradition for a strong workforce was one of the selling points that led Mazda Toyota to select north Alabama.
“One reason this area was popular is that there’s a really good workforce in the [Tennessee] Valley,” Castile says. “A lot of people live in north Alabama and drive to Tennessee to work, so it’s a chance for them to stay home and work. In addition, there are three other automotive plants in the state that have been very successful, so we have a track record of finding and keeping good automotive workers.”
Because Huntsville leaders have “chased large projects before,” they knew that workforce would be an important piece of the puzzle, Cherry says. That’s one reason they hired Deloitte to undertake an updated labor study.
“That study showed that we have the capacity to handle an additional 7,000 employees in the automotive sector over the next five years,” Cherry says.
That means other automotive plants — such as the nearby Toyota engine plant — don’t have to worry about experiencing employee shortages when the new factory comes online. “Our definition of success is not robbing Peter to pay Paul,” Cherry says.
There’s room for more skilled jobs partly because many residents are employed in jobs that do not meet their full potential. “There’s a significant pocket of underemployed individuals in north Alabama and southern Tennessee,” Cherry says. “They may not be unemployed, but they’re interested in improving their prospects.”
For instance, when Polaris opened a plant in Huntsville in 2016, about 10,000 people applied for about 450 jobs, and more than 7,200 were qualified to move to the next stage of the process, Cherry says. Similarly, when Huntsville’s Toyota engine plant announced a need for 100 new workers recently, 10,000 people applied.
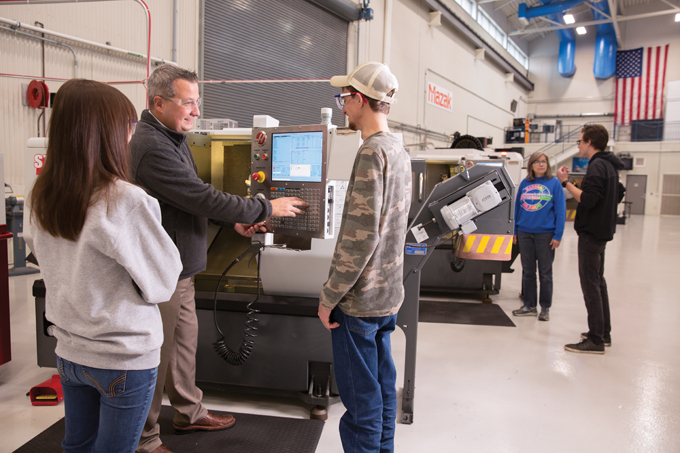
Preparing New Talent
While north Alabama already has a valuable existing workforce, area leaders are also working to train new workers and students to be prepared for the jobs that will be available at Mazda Toyota now and in the future.
“The automotive industry will look completely different in the next five years compared to today,” says Kim Ogle, manager of external affairs at Toyota Motor Manufacturing Alabama. “It is critical to have a workforce that can adapt to change, solve problems and quickly learn new technologies. Stronger partnerships and collaboration between the industry and educators is key for developing and maintaining a talent pipeline. Educators must understand what the industry needs so they can create programs that help develop students to meet the workforce needs. We also need educators to help us overcome misperceptions of careers in manufacturing to help increase interest in the field.”
To help meet an ongoing need for skilled maintenance technicians, Toyota partnered with Calhoun Community College in 2014 to develop the Advanced Manufacturing Technician Program (AMT), Ogle says. The AMT program is a two-year work and study program that allows students to gain industry work experience that aligns with classroom curriculum, making them ready for employment upon graduation. About 12 partner companies now participate to sponsor AMT students, so graduates help fill the gap for skilled workforce needs across the industry, not just at Toyota.
Toyota is also working with AIDT to develop innovative new hire assessment and training programs, Ogle says. For instance, at Toyota’s request, AIDT is ramping up an apprenticeship program that supplies maintenance technicians and other skilled professionals to several local manufacturers and will now prepare more workers.
In partnership with Calhoun Community College, the Federation of Advanced Manufacturing Education (FAME) provides a two-year technical associate degree, along with paid work experience at a local plant and experience in advanced manufacturing technology. The program has operated successfully for several years, and at Mazda Toyota’s request, AIDT is currently working to expand it. A new FAME center will be located in the Alabama Robotics Technology Park, located in Tanner, adjacent to Huntsville, Madison and Decatur.
Along with the FAME apprenticeship program, local community colleges also offer standalone courses and curricula, such as those that will be available at the new plant. “Calhoun, Northwest-Shoals, Wallace State and Drake State community colleges are all gearing up to offer programs in advanced manufacturing to help provide the workforce we’ll need,” Castile says.
High school technical education programs are also part of the effort. When the Alabama Legislature’s 21st Century Workforce Act passed in 2013, it provided $50 million to equip high schools with high-tech equipment to teach students the skills needed for advanced manufacturing and other jobs of the future.
The investment is paying off, Castile says. “We’re one of only a few states in the country that have high school career tech programs that allow kids to graduate high school with industry certifications,” he explains. “Those students are successfully entering the workforce, or going on to college to become high-level engineers. These programs are supporting a wide range of workforce needs that are all important.”
The Huntsville/Madison County Chamber of Commerce has recently developed a plan “to help people select a career path before they select an education path,” Cherry says. “We want to provide opportunities for people who are interested and share the information with schools. With co-ops available, many students can cover the cost of their education and get out of school without debt.”
Assisting with the Recruiting Process
A highly trained workforce will clearly benefit companies across the Tennessee Valley and the state, not just the new Mazda Toyota plant. But at the moment, the new factory is top of mind.
When Mazda Toyota is ready to begin the process of sourcing new applicants, AIDT will help get the ball rolling, just as it has for other automotive plants when requested. “We’ll craft a process for individuals to apply online for jobs, and those applicants will be reviewed automatically and organized into different buckets based on their experience and expertise,” Castile says. “As closely as we can, we’ll match the applicants to the precise skills the company is looking for. Those who are strong matches will be interviewed and go on through the process.”
As construction continues on the plant, education and training continues to prepare its future workers. “We have the workforce to support this,” Castile says. “We don’t just have warm bodies, but we also have specific skills that have been built into this workforce.”
Nancy Mann Jackson and Dennis Keim are freelance contributors to Business Alabama. Jackson is based in Birmingham and Keim in Huntsville.