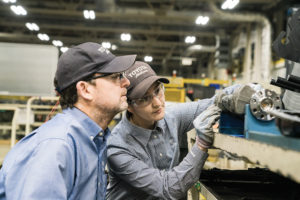
In March of last year, Toyota Motor Manufacturing, Alabama Inc. (TMMAL) announced the plant’s fifth expansion, a $288 million investment, adding two new production lines that will increase its annual engine capacity to 900,000 and add 450 new jobs by the end of 2021.
“900,000 engines, that’s incredible! That tells us the market demand is there for the products we’re making, and it’s exciting to be a part of this expansion and growth,” says Dave Finch, who was announced as the new president of TMMAL in July. He joins the plant from Toyota South Africa where he has worked for 28 years, most recently as the senior vice president of manufacturing.
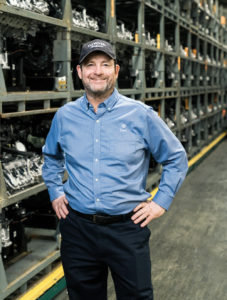
This is Finch’s first U.S. assignment. He and former TMMAL President David Fernandes are on a two-year rotation as part of a global executive development strategy. “The global rotation is to expose and develop Toyota’s executives in other regions,” explains Finch. “It’s based on the ‘teach and be taught’ concept, developing leadership skills while transferring unique experiences and best practices from your region or country to make the company more effective and efficient.”
The new 4-cylinder and V-6 engine lines require a building expansion, as well as the largest hiring requirement in the plant’s history, bringing the total investment to $1.2 billion and 1,800 team members.
“We are in the full throes of our expansion,” says Finch, referring to the building construction currently underway for the new V-6 engine line and scheduled for completion in fall 2020 with trial production set to begin in summer 2021. “We’re very excited to add a new V-6 line to our production capabilities,” he continues. “It’s going to be the longest engine line globally with a lot of complexity. The fact that our plant is expanding yet again says a lot about Toyota Alabama and the level of confidence that Toyota Motor Corporation has in our workforce.” The 4-cylinder line will begin production in summer.
“We aren’t ready to announce the product mix yet,” says Kim Ogle, corporate communications analyst at TMMAL. “Right now, our focus is positioning the plant to be more flexible and competitive in the market, and the addition of the two lines helps us accomplish that goal.” She adds that the plant produced approximately 610,000 engines in 2019, about 2,500 engines a day and five times the amount since production began in 2003.
The Alabama facility is the only Toyota plant globally to build 4-cylinder, V-6 and V-8 engines under one roof. The plant’s engines go into six of the ten Toyota vehicles produced in North America, making it a critical part of the Toyota supply chain and one of the largest Toyota engine plants in the world. Around 42 percent of the facility’s production volume consists of V-6 engines built for the Tacoma and Highlander, 36 percent is 4-cylinder engines for the RAV4, Highlander and Corolla, and roughly 22 percent is V-8 engines for the Tundra and Sequoia.
“Our flexible production environment allows us to respond quickly to market demands and what our customers want now and down the road,” says Finch, who anticipates another high-volume year in 2020. The plant is on course to produce its seven millionth engine in April.
To handle that volume, the plant continues to develop strategies for the recruitment and training of its employees.
“We collaborate with many local and state partners to build programs that spark interest in automotive manufacturing careers,” says Ogle, who has taken the lead on developing programs at the plant tied to National Manufacturing Day in October. In 2019, she tried something new to specifically reach out to young women. “Only 25 percent of the people who work in manufacturing are women,” she points out. “So this year we wanted to focus on helping to close the gap.”
Ogle and her team developed Girls Learning About Manufacturing, or GLAM Camp, to expose young women to career opportunities at the plant. Working with career coaches in Huntsville city schools, they invited high school seniors to apply for one of 25 spots in the camp, keeping the number low to ensure participants would have plenty of one-on-one interaction with plant staff, especially female employees in leadership positions.
The six-hour visit included a plant tour that Ogle says helped to dispel misperceptions about what manufacturing jobs look like and instead revealed a high-tech work environment where employees use critical thinking and problem-solving skills on the production floor. GLAM Camp attendees also rotated through four stations where they participated in hands-on STEM activities related to manufacturing. Finally, the young women were introduced to the company’s Advanced Manufacturing Technician program, which allows students to gain workplace experience while earning a salary and a degree.
“We had the best time and were able to introduce manufacturing to the girls in a relatable way,” says Ogle, adding that the program received a lot of recognition within Toyota North America and that other plants are looking to use the TMMAL model to do similar outreach in their communities.
“We always want to have a healthy pipeline of talent coming through Toyota,” says Finch. “But the programs that we’re involved in, it’s about broader community development. If they come back to work at Toyota, that’s great. That’s what we want. But if they don’t, you’re developing people that are going to make Alabama stronger, Huntsville stronger, the community stronger. That’s the Toyota way.”
Katherine MacGilvray is a Huntsville-based freelancer for Business Alabama.