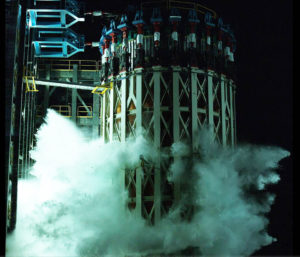
Engineers at NASA have completed the Space Launch System rocket’s structural testing for the Artemis lunar missions. The first Artemis mission will take humans back to the Moon, with subsequent missions going to Mars.
For the final test, the liquid oxygen tank test article — measuring 70 feet tall and 28 feet in diameter — was bolted into a 185,000-pound steel ring at the base of Marshall Space Flight Center’s Test Stand 4697 in Huntsville. Hydraulic cylinders were then calibrated and positioned all along the tank to apply millions of pounds of force from all sides while engineers measured and recorded the effects of the launch and flight forces. The liquid oxygen tank circumferentially failed in the weld location as engineers predicted and at the approximate load levels expected, proving flight readiness and providing critical data for the tank’s designers. This final test on the liquid oxygen structural test article met all the program milestones.
“The Space Launch System and Marshall test team have done a tremendous job of accomplishing this test program, making a major milestone not only for the SLS Program but also for the Artemis program,” said John Honeycutt, the SLS program manager.
The successful completion of the structural qualifying testing at Marshall wraps up the largest test campaign at the center since tests were conducted for the Space Shuttle Program, more than 30 years ago. During the test campaign five structural tests articles underwent 199 separate test cases and more than 421 gigabytes of data were collected to add to computer models used to design the rocket.
Earlier this year, NASA and engineers from Boeing, the core stage prime contractor, completed 24 baseline tests that simulated actual flight conditions on the liquid oxygen structural test article. For all the tests, thousands of sensors measured stress, pressure and temperature while high-speed cameras and microphones were used to identify any buckling or cracking in the tank’s wall.
Marshall also has been conducting structural qualification testing on the rocket stacked together, which includes the interim cryogenic propulsion stage, the Orion stage adapter and the launch vehicle stage adapter. This testing was followed by tests on the four largest structures that make up the core stage — the engine section, the intertank, the liquid hydrogen tank and the liquid oxygen tank.
“The Marshall test lab team has worked closely with the Space Launch System Program to test the rocket’s structures from the top to bottom,” said Ralph Carruth, Marshall’s test lab director.
With the testing done, designers now have data that may be helpful in optimizing SLS hardware.
“We have successfully completed our core stage major structural tests at Marshall Space Flight Center and are making progress on Green Run testing of the Artemis I core stage at Stennis Space Center that will simulate launch,” said Julie Bassler, the SLS stages manager.
Teams at Stennis, in Mississippi, are making progress on Green Run testing of the assembled SLS core stage for the Artemis I mission. At Michoud Assembly Facility in New Orleans, Louisiana, Boeing has manufactured all the main core stage structures for the Artemis II mission and started work on the Artemis III structures. Aerojet Rocketdyne has assembled engines for the Artemis II mission and is in the process of assembling Artemis III engines.
Northrop Grumman has delivered booster segments to NASA’s Kennedy Space Center in Florida, where they are being prepared for launch. All 10 of the segments for the second Artemis mission are cast and Northrop is now working on the boosters for Artemis III.
The only remaining pieces of hardware for the Artemis I flight test to be delivered are the launch vehicle stage adapter, which connects the rocket to the Orion spacecraft and will arrive this summer, and the SLS core stage, which will be transported to Kennedy by barge after the Green Run test at Stennis later this year.