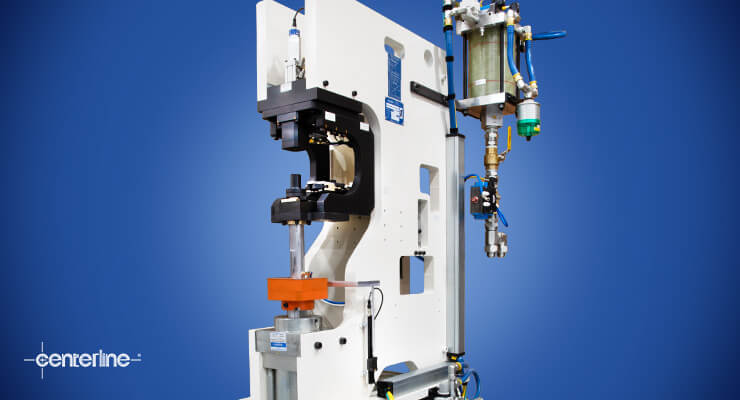
The Automotive Industry’s migration to lightweight materials, such as aluminum castings and extrusions, Magnesium, and thin gauge Ultra-High-Strength Steel, has increased the need for clinch fasteners versus traditional projection-welded fasteners. Clinch fastener installation is particularly well suited for joining thin and lightweight materials.
The Patented SoftMount™ Clinch Press (SMP) solves a problem that manufacturers have struggled with locating the hole in a robotic cell to concentrically clinch the fastener robotic production cells. The SMP uses compact and compliant tooling that allows the press to mechanically fine-adjust its position to a stamped hole.
This system is available in two configurations:
- Inverted Feed Process (IFP): the part is loaded to the upper smart sensing pin while the nut is loaded to the lower pin. This inverted process saves cycle time.
- Standard Feed Process (SFP): the part is loaded to the lower smart sensing pin, and the nut or stud is fed to the lower pin on top of the part. This standard process is required for studs and nuts where the part geometry interferes with the IFP process.
Overall, machine efficiency is increased because the SMP can fin-adjust its position to locate the hole.
CenterLine’s experienced applications team can solve many challenging applications. An example is a retractable upper punch. Limited part clearance was required on a recent project, but the SMP was able to overcome this with a unique solution that allowed the feeder to present the fastener to the lower smart sensing pin. This was possible because the punch is able to retract in the throat of the press frame to make the tooling accessible. Once the part and fastener were located on the pin, the punch moved into position and proceeded to install the clinch fastener.
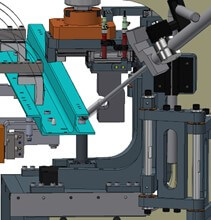
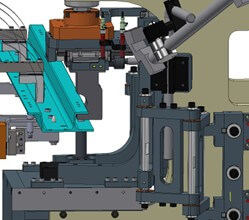
SoftMount™ Clinch Press (SFP) with retractable upper tooling.
Another example of the SMP’s flexibility was utilized when a customer requested to clinch multiple fasteners on one SMP with a quick changeover feature. The solution was in the upper die and lower punch/pin assemblies, which can be quickly removed and stored on the side of the press frame, depending on which fastener is chosen to run. Tooling presence sensors are also used to ensure the proper tooling is in place while running the specific program.
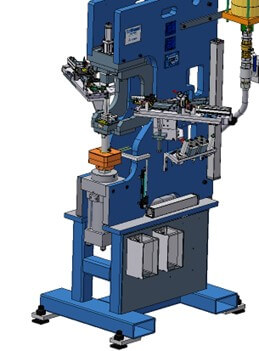
Another important feature of this press is its two Quick Fastener Placement (QFP) units and press tooling, which are unique to the two fasteners installed on the machine. This layout allows for easy tooling changeover with a Poka-Yoke to ensure the correct tooling is used.
Due to the shortage of skilled workers, more companies are moving their fastener applications into automated robotic processes. CenterLine’s SMP meets this growing need head-on with a compliant and versatile machine that ticks all the boxes. In conclusion, the CenterLine SoftMount™ Clinch Press process is a game-changing machine for the automotive industry due to its innovative technology, reduced cycle time and increased efficiency, which gives our customers an advantage over their competitors who are using conventional clinch press processes.
If you’re interested in our SoftMount™ Clinch Press, please don’t hesitate to contact us at [email protected] to connect directly with one of our sales managers.