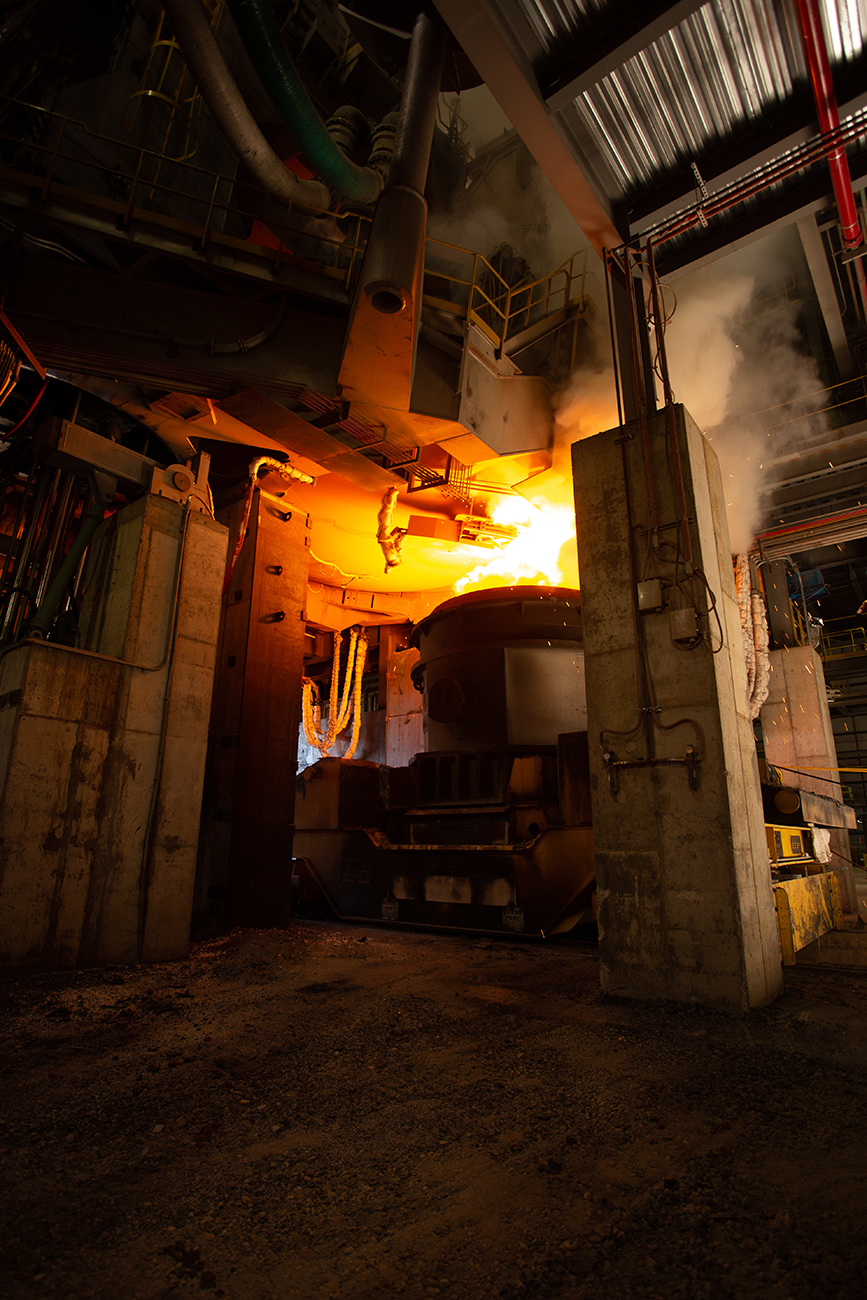
Birmingham endured many hazy days of summer during its steel-making peak of the 1960s and ’70s. Back then, whenever stagnant air descended upon the city, it often trapped the smoke and soot billowing from the steel plants, coating the skyline in a brown murky mess.
This was tolerated because Birmingham had literally been built on a mountain of steel — or at least, the iron ore that produced steel — and the brown haze represented sunny skies for thousands of plant workers and their families (nearly 20,000 at one point).
But both the haze and the jobs gradually dissipated, as steelmaking lost its grip on the Birmingham economy, replaced over the decades by banking, health care and the sprawling research campus of UAB.
Finally in 2015, Pittsburgh-based U.S. Steel, which had been operating a major plant in Fairfield for more than 100 years, shut down its blast furnace, affecting more than 1,000 workers and eventually dropping employment at the plant to approximately 700.
Now, some of the jobs are coming back, though the haze is still gone. Both developments are because of a new electric arc furnace (EAF) that U.S. Steel began operating late last year at the Fairfield plant. It is a more environmentally friendly form of steelmaking that is adding approximately 150 jobs to the plant but zero pollutants to the sky.
“When we shut down the blast furnace, we still had a rounds caster that made products for our pipe mill, but it didn’t have a steel supply,” says Scott Dorn, head of U.S. Steel’s Tubular Solutions division. “So we elected to embark on a manufacturing operation that’s newer and cleaner. It’s a much different technology than the old blast furnace.
It’s sustainable and much more flexible. You can turn it on and off to meet your demand.”
With EAF steelmaking, existing scrap metal is in essence recycled by using electric heat instead of a fiery furnace to melt it into liquid steel. Matt Matthew, plant manager of U.S. Steel Fairfield Tubular Operations, describes the process like this:
“We primarily use scraps of steel that may come from automotive or demolition,” Matthew says. “We add a little bit of pig iron to it, then put these scraps into an electric
arc furnace, which is a 25-foot vessel. The roof is shut, and the scrap steel is melted
into new steel. It’s done with tremendous amounts of electricity, along with some
natural gas, carbon and oxygen.
“We refine the steel and bring it up to 3,000 degrees. Then we tap it, which is
emptying the vessel of liquid steel. Then we take it to a ladle furnace where we adjust the chemistries to the perfect levels for the products that we’re making. We’ll do a vacuum tank degasser, where a vacuum pulls impurities out of the steel, like hydrogen and nitrogen. Then we’ll go to a continuous caster, which will make round tubes that will be used for seamless pipe production.”
Not exactly Rachael Ray or Bobby Flay, but it is a recipe that will keep the plant operating for the foreseeable future. U.S. Steel invested $412 million to install the EAF, along with
a gas-cleaning plant, a water-treatment plant and a revamped continuous rounds caster. The plant is now running 24 hours a day, Monday through Friday, with a potential production output of approximately 1.6 million tons of steel per year.
“We started this process last October, got some things adjusted, and then went to round-the-clock operations this year,” Matthew says. “We’re having a very successful ramp up, making more and more batches of steel of 170 tons each. We’re developing capabilities and confidence with our people, our processes and our equipment.”
The Fairfield plant EAF is important to U.S. Steel, because the former smog producer has publically stated a commitment to a much greener future. The company has a goal to reduce its greenhouse gas emissions by 20 percent worldwide by 2030, and in April announced an initiative to reach net-zero carbon emissions by 2050.
To do so, the company stated in a news release that it “expects to leverage our growing fleet of electric arc furnaces, coupled with other technologies such as direct reduced iron, carbon-free energy sources, and carbon capture, sequestration and utilization.”
“This fits the objectives we have to reduce emissions and increase our sustainability,” Dorn says of the new Fairfield plant EAF. “It represents a much smaller carbon footprint and the reduction in greenhouse gasses compared to the previous blast furnace process.”
The EAF also represents jobs, though admittedly many fewer than were needed for the old blast furnace. Matthew says many of the employees who are working with the EAF have been part of the Fairfield plant in the past.
“The people who were here before make up the majority of our workforce (for the EAF),” Matthew says. “Some of them went to the pipe mill and other types of things like that. But we didn’t bring in a big workforce from somewhere else. It was the workforce that was already around here.”
While some of the steel-making techniques remain the same, there are enough differences that the employees had to go through an EAF training process. Some of that was done
at the technologically advanced Big River Steel in Arkansas, a U.S. Steel subsidiary that is the only LEED-certified steel mill in the United States.
“They had to learn some new skills,” Matthew says of the Fairfield plant EAF employees. “They had some classroom train-ing. We brought consultants here from all over the country to teach them the philosophies. There are a few leadership positions where prior electric furnace experience was required. But for the most part the workforce is people who were already here who we trained (for the EAF).”
Steel-making has long been important to Birmingham’s economy, particularly in Fairfield, and U.S. Steel has been part of that for more than a century. The company’s connection
to Birmingham dates to 1907, when U.S. Steel bought the Tennessee Coal, Iron and Railroad Company, which despite its name was headquartered in Birmingham.
“We have a lot of history in the Birmingham facility,” Dorn says. “Our tubular mill was put in during the early ’80s, and we’re very proud of that. It’s really the focal point of our tubular solutions division. Now we have an electric arc furnace to supply that facility. It really gives us a good combination of the two production facilities.”
This story first appeared in the June 2021 issue of Business Alabama.