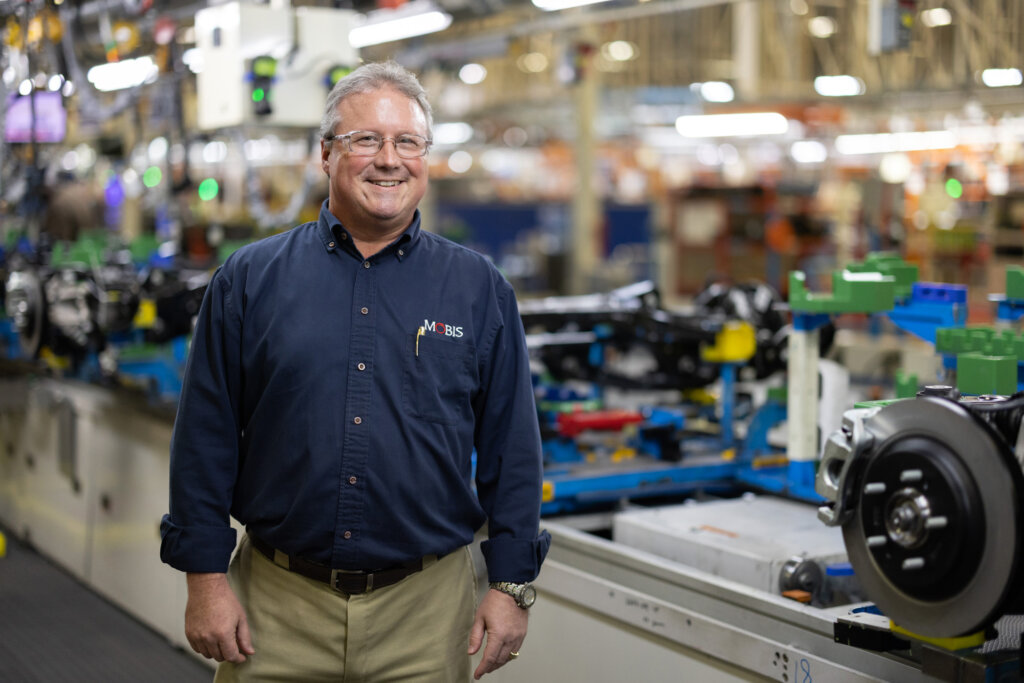
When a supplier firm wins kudos from the Alabama Automotive Manufacturers Association, it’s something to brag about.
This year’s winner among large manufacturing firms, Mobis Alabama LLC, has earned those bragging rights.
The firm that’s nestled alongside Hyundai Motor Manufacturing Alabama was nominated by the OEM firms it supports, then vetted by the association and then selected as the year’s winner.
Although the firm has announced a major expansion, that’s not the reason they won, says AAMA CEO Ron Davis. “It isn’t why they won, but it highlights their role. It’s the bow on the package,” he says.
“What’s more important,” says Kevin Taylor, assistant director of prospect recruitment and training for AIDT, the state agency committed to helping companies find the workers they need, “is operational excellence and production to their customers. Hyundai is heavily involved in the nominating process. The OEMs know who produces good quality parts — that’s most important — and making sure they’re coming in in the proper time.”
That phrase, “the proper time,” may seems somewhat off-hand and casual.
For Mobis, however, it’s anything but.
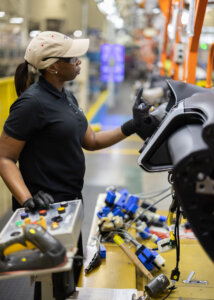
When the team’s associates go to work to craft front and rear chassis and cockpit modules for HMMA, the turn-around time — from order to delivery — averages 45 minutes to an hour, says Senior Manager Scott Gordy.
The modern trend to just-in-time delivery, where neither supplier nor client devotes voluminous space for storage or inventory, results in a carefully choreographed system.
“It’s a very precarious dance we do,” says Gordy.
Most of the company’s team works in the module building, where those chassis and cockpit units are created.
Next door is the plastic extrusion facility, molding bumpers and instrument panel skeletons for both HMMA and its sister Kia plant nearby in Georgia. “There’s a little more leeway on timing” for those elements, Gordy says.
Mobis has two more buildings at the Hyundai location, part of the redistribution center that gathers its own parts plus more from other Tier 1 and Tier 2 suppliers, then ships them to dealerships and others who need aftermarket parts.
Early in 2022, Hyundai announced that it would begin to produce electric vehicles at its 21-year-old Montgomery plant. Just a few months later, Mobis announced that it would invest $205 million to develop an EV battery module plant to support both Hyundai and Kia.
“As the EV market continues to grow, having a strong production capacity will be key in allowing Hyundai Mobis to see continued growth in the market,” says H.S. Oh, vice president of electric powertrain business of Korean-based parent company Hyundai Mobis. “We believe this new facility in Montgomery will be an important step in that process, and we are excited for the project to be under way.”
Alabama Secretary of Commerce Greg Canfield lauded the announcement, saying “Hyundai Mobis’ investment project in Montgomery reflects an acceleration in the development of the EV supply chain in Alabama’s auto industry. We’re going to be a major production player in the EV market, and that’s going to trigger more growth within the sector.”
At present, the firm has about 900 employees and a total of 1,100 workers, when contractors and temporary hires are included. Adding the new battery stacking capability will add some 400 employees to the staff, Gordy says.
At the same time, parent company Hyundai Mobis is opening an additional plant in McCalla to support Mercedes.
While finding workers is a challenge for all industrial employers these days, Gordy says, “We have been fortunate enough to secure the labor we need, but it is difficult. We use several temp firms and outsource some to contractors.”
He hopes that the firm will be able to find the additional workers it needs, because the jobs on offer are “full-time permanent jobs, well compensated.”

Beyond the new battery work, the new emphasis on electric vehicles creates changes in the module facilities, too, says Gordy. Because of different needs, the cockpit module for an EV is quite different from that for a gasoline-powered vehicle.
Growth is nothing new for the Montgomery Tier 1 supplier. The module and plastics element of the plant were completed in 2004, all designed to serve two Hyundai models. Now it provides key elements for seven models.
Gordy worked for Hyundai until 2020, then moved to be closer to family during the worst of the COVID-19 times. But that move meant a change to a different industry. When the chance arose to come to Mobis, back to Montgomery and back into the automotive world, he jumped at it, moving into his leadership role in 2022.
“Automotive is where my heart is pulling me,” he says.
Now he is thrilled at the honor from the AAMA.
“With the numerous Tier 1 suppliers in Alabama — and there are some huge names out there — to be recognized for the things we do every day, for doing the right things for the right reason at the right time, to be honored by the OEMs is a great honor, a huge honor.”
Nedra Bloom is a Mobile-based writer/editor for Business Alabama, and Cary Norton is a Birmingham-based freelance contributor.
This article appears in the March 2023 issue of Business Alabama.