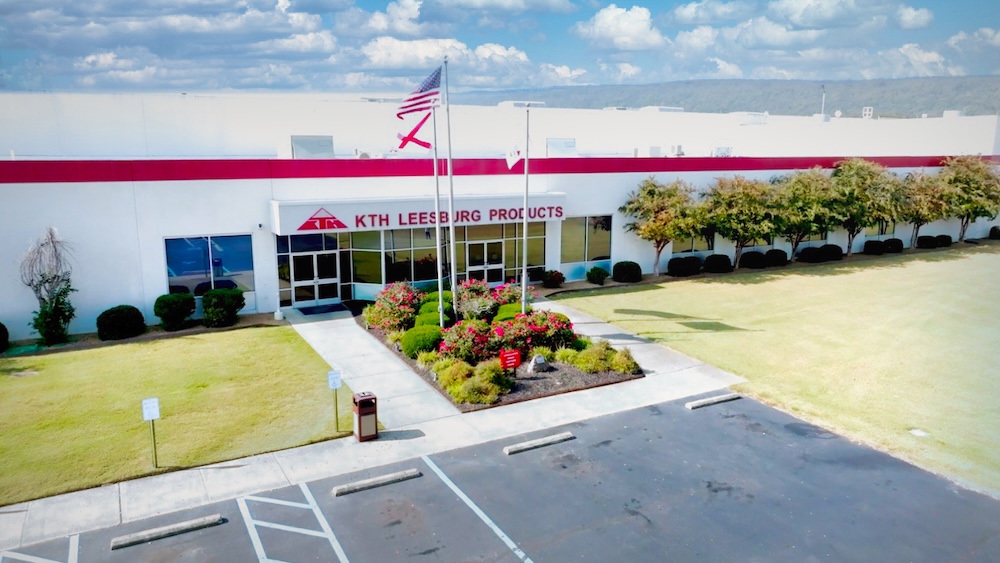
In November 2024, the Alabama Automotive Manufacturers Association (AAMA) announced the winners of their Supplier of the Year awards. At the top of their list was KTH Leesburg Products LLC (KLP), winning for Large Manufacturer of the Year.
“It’s really a tremendous feeling to get such an award,” says Gene Cleveland, assistant vice president of administration of KLP. “When [the AAMA] do their due diligence, they’re checking with our customers and saying ‘hey, this plant has been nominated for an award — what kind of company are they?’ And when they give their answers, they’re considering quality workmanship, overall safety calls, delivering on time, all those major characteristics that they look for in their suppliers. So, to have that affirmation from our customers… really is beyond words.”
And this isn’t the first honor the company has received. “Over the years we’ve won various awards from Honda,” says Cleveland, “and we just recently won an excellence award from Mazda.”
Kim Hoyles, KLP’s assistant vice president and plant manager, explains: “Mazda had their supplier conference in Huntsville and out of 150 different suppliers, KLP was one of only 5 that received a Quality Excellence Award, which is very impressive because … the criteria to win that award is very high. So, it was a great honor for us.”
Nestled in Leesburg — a town of less than a thousand people in Cherokee County in northeast Alabama — KLP is anything but small-time, supplying enough stamped and welded steel frame components for the automotive industry in Alabama to build roughly 1,500 to 1,800 automobiles every single day from its 515,000-square-foot manufacturing plant employing more than 475 people. Those components are checked for quality and safety and shipped directly to KLP’s customers for use in the automotive assembly lines — primarily either to Honda in nearby Lincoln or to Mazda in Huntsville.
“A lot of our frame parts [are] called ‘crash parts’,” says Ryan Enloe, senior manager for quality and engineering at KLP. “They are a lot of the parts that have a big impact on the crash worthiness rating of the vehicles, so they tend to be more important parts, as you can imagine.”
With such an important role in the automobile, Hoyles explains, quality is paramount: “Every component that goes into a car is important. When it comes to the quality or stability of any of the parts we produce, every part has to be 100% good… The parts that [we] produce have a significant impact on the survival rate of [people] in the cabin of that car. So, every part that we produce has to be 100% perfect, because the customer relies on it.”
And KLP ensures that the plant’s associates know the importance of the work they’re doing. “We try to inform all the associates,” says Hoyles. “In our plant we have vehicles from Honda that are called ‘white bodies’. It’s just the shell of the car without any components in it [so that we can] show them where our parts are located. We have a display in the front of our shop showing… where [our] parts are located in the vehicle, what they do, and how they fit together to make that vehicle.”
“They can actually see where this crazy-looking part they’re producing plugs in,” adds Enloe. “When a vehicle comes together it’s like a giant 3-D puzzle… and when I know why I’m doing something, I’ll tend to take it more seriously and have more buy-in… Our associates understand just how important their parts are, and when you understand that I think you just naturally take it more seriously.”
This understanding is paying dividends for KLP, says Enloe, specifically in the quality of associates’ work and employee tenure. “One of the things that I’ve noticed down here is the associate’s willingness to work very hard, and it’s refreshing to see that… We have a lot of people here that have multiple years of experience and we try to do our best to make it comfortable for them to work and to someday retire from our facility.”
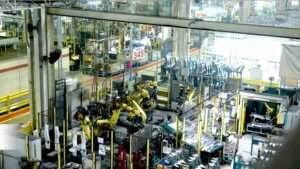
KLP’s road to success was a long one, dating all the way back to 1939, with Hirata Press Kogyo, a metal press in Tokyo, Japan, which found success in the years afterward producing car parts for Honda. As Honda’s success grew, so did Hirata Press Kogyo’s, and in 1985, the first North American branch began operations in St. Paris, Ohio. A second Ohio plant followed about a decade later, then a location in Canada, and finally in 2001, an Alabama manufacturing plant in Leesburg.
But why choose Leesburg for such a large undertaking? Location was a big factor, according to Cleveland: “[We] like to do the stamping and welding of steel parts in a fairly close proximity to the customer. So when Honda made the decision to come to Lincoln, Alabama… we looked around the area and decided to locate about 60 miles north of Lincoln… Other factors obviously go into that [decision], you know: employment and demographic data … infrastructure, what incentives are available in what areas. There’s a list about as long as your arm, but obviously, close proximity to the customer was important.”
It has certainly not escaped KLP’s notice that it is a major employer in a small town, which is why giving back to the community is a high priority for the company. “There are a lot of very small towns in and around this area,” says Cleveland, “and we do a number of things to participate in and engage with those communities throughout the year.” For example, the company helps support Leesburg Day, a September event that helps raise funds for the local volunteer fire department.
The benefits of KLP’s success don’t just extend to community activities, but associate benefits as well, company officials say. “The company looks beyond just the associates that actually come to work here each day, and we actually look after their family members, too,” says Cleveland. “KLP provides a medical clinic for all the associates and their covered family members absolutely free of charge. In addition to that, we have the ability to provide prescriptions free of charge.… This has been a tremendous benefit for our associates and their families to help alleviate a lot of medical concerns. It’s not a mandate that they have to use the clinic, but it gives them another option, and it’s just awfully hard to beat free.… Having this free access to medical attention has been a really wonderful benefit for our associates, and I think they recognize that.”
Steven Castle is a Mobile-based freelance contributor to Business Alabama.
This article appears in the February 2025 issue of Business Alabama.