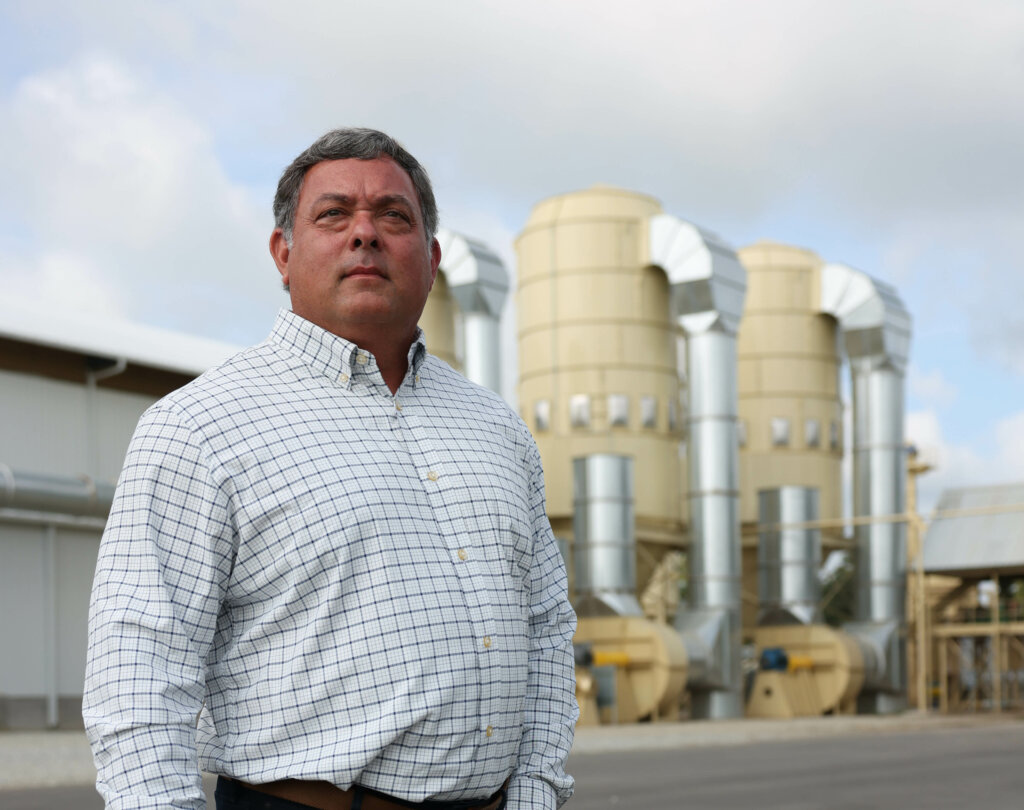
Over the last few years, more than $100 million has been invested in rural communities in and near Alabama, providing hundreds of families in underserved areas with good jobs. And at the center of this frenzy of economic development are two things — Dothan-based contractors Hollis & Spann Inc. and the humble peanut.
Glenn Spivey has been president of Hollis & Spann since 2011 and has seen the company at every level. “I started in 1993 as an intern when I was trying to make enough money to finish Auburn [University],” says Spivey. “[Then] in 1995, I started off as an assistant superintendent, quickly transitioned to a project manager, then vice president and then president.
“Our company was founded in 1950. They went through residential work, in the early days building cabinets, even boat work one time. And then in the ’60s [we] transitioned over to commercial construction. It just kind of grew from there. When I came on in 1993, we were doing a lot of corrections work — prisons, jails,” says Spivey. “In the ’90s we got into building hotels.”
And now, Hollis & Spann has grown into a major player, ranking 23rd on Business Alabama’s list of largest contractors in Alabama, with close to $100 million in contracts annually. And while Hollis & Spann specializes in the hospitality industry — they have constructed more than 85 hotels in the Southeast for national chains like Hilton and Marriott — their most unusual recent work has involved peanuts.
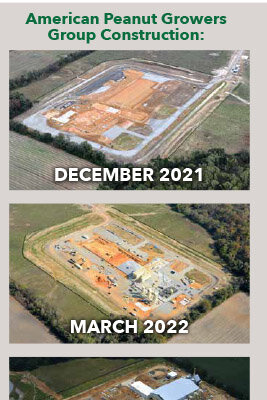
Hollis & Spann has completed two different but similar peanut-related facilities — a peanut-shelling facility in Atmore for Coastal Growers LLC and a peanut storage, shelling and processing complex for the American Peanut Growers Group LLC (APGG) just a few miles from the Alabama border in Donalsonville, Georgia. “These two projects were about as much fun as I have had in my whole career,” says Spivey. “They’re tremendously rewarding, satisfying projects for me and all the people involved. We would love to do more of these kinds of things.”
Part of what makes these projects more fun, according to Spivey, is the challenge they pose and the precision required, especially in the planning phase. “There are aspects of [hotels] that are more difficult than industrial projects, but with industrial projects, you have to have everything perfectly planned ahead of time. It all has to fit exactly right.
“For the peanut plants, we provided the electrical system, which included the controls of all the equipment. Our subcontractor programmed the operation of all the equipment, which is a big deal…The coordination between the general contractor and the equipment designer, manufacturer and provider — who’s all the same company — was extremely important,” says Spivey.
Coastal Growers in Atmore has leveraged its new facility, completed in 2021, to realize the dream of peanut farmers throughout the area. One of Coastal Growers’ three co-founders, Joe Parker, explains, “[We have] 180 investors made up of farm families throughout the Southeast… It’s a game changer for them financially with great potential to…double their profits per acre.”
“This allows [the farmers] to be vertically integrated up the value chain for the peanuts they grow,” explains Alex Jones, president of UB Community Development, which assisted with finances for both projects. “So instead of a corporation shelling and selling the peanuts to Mars or Smuckers or Jif, the farmers now own this plant that sells those peanuts, and they get a proportional share of that profit.”
In Donalsonville, APGG and its President and CEO Neal Flanagan are still readying for the sweeping economic impact that their brand-new complex, officially opened in June of this year, will have on the local community. “We employ over 240 employees in a town of 2,800 people,” says Flanagan. “So that says something about the size and the scope of our business in a small town.”
The Donalsonville complex consists not only of peanut storage and shelling, but also on-site processing of peanuts into goods like peanut butter and paste, primarily for industrial applications — a side of the business in which local farmers weren’t yet experts. “We needed somebody with horsepower,” says Flanagan. “It was a little bit of a dive off the deep end for us as far as complexities like air pressure and those kinds of things. We needed somebody with expertise that could research and learn together with us.” Having just been involved with the Atmore shelling plant, Hollis & Spann was the logical choice.
Both projects have more than just peanuts in common. Also shared between the two sites is a large boon of federal assistance in the form of new market tax credits, corralled by UB Community Development and Jones. “We created UB Community Development years ago to do new market tax credit transactions. We built it from the ground up. There are other CDE’s [community development entities] all across the U.S. that do what we do… but we’re the first ones here in Alabama.”
These new market tax credits are focused on developing businesses in underserved communities and have helped bring prosperity to rural areas throughout Alabama and neighboring states. “We’ve secured almost $300 million in federal tax credits from the Department of the Treasury,” says Jones. “We’ve probably done about 30 projects now with about a billion dollars in capital expenditure over the years.”
Those crucial economic incentives are just one reason why these peanut companies have turned to Hollis & Spann. “There’s a lot of general contractor work in getting the new market tax credit — [contractors] have to be vetted, they have to have certain credentials, they have to have a lot of budgets and timelines in place,” says Flanagan. Again, Hollis & Spann “had done it all before.”
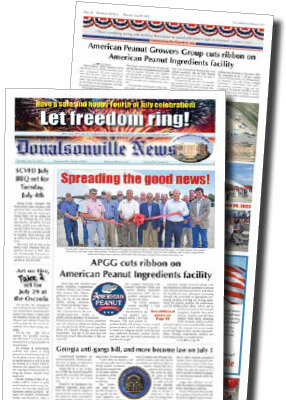
Hollis & Spann’s history with these credits isn’t the only draw for their clients. Their communication and relentless diligence are commonly praised. “When [the project] was just a dream, they were involved,” says Parker. “They were willing to take some risk in doing the dream stage with us before ever breaking ground.”
“They communicate well,” says Flanagan. “They’re always available, they’re always engaged. You always feel like you’re communicating with them on a daily basis… [It was] a true partnership.”
These projects may have recently finished, but their positive impacts have only just begun. “This money is going back into the rural communities where the farmers are located that they can use to buy another tractor, or just do other things in their communities that boost economic activity,” says Jones. “Plus, [in Atmore and Donalsonville], there are 100 people in each place who have jobs that didn’t before.”
That positive impact in rural communities sits well with Spivey: “Hometown pride,” he says. “You can imagine when we finished [these projects] how proud we were — just to be involved in something grower-owned. My dad farms and has always been in agriculture. It was something we were super proud to be involved in.”
The challenge of distributing wealth and economic opportunities to the far reaches of rural Alabama may often seem daunting, but for UB Community Development, Coastal Growers, the American Peanut Growers Group and Hollis & Spann, that challenge did not prove a very tough nut to crack.
Steven Castle and Jay Hare are freelance contributors to Business Alabmaa. Castle is based in Mobile and Hare in Dothan.
This article appears in the September 2023 issue of Business Alabama.