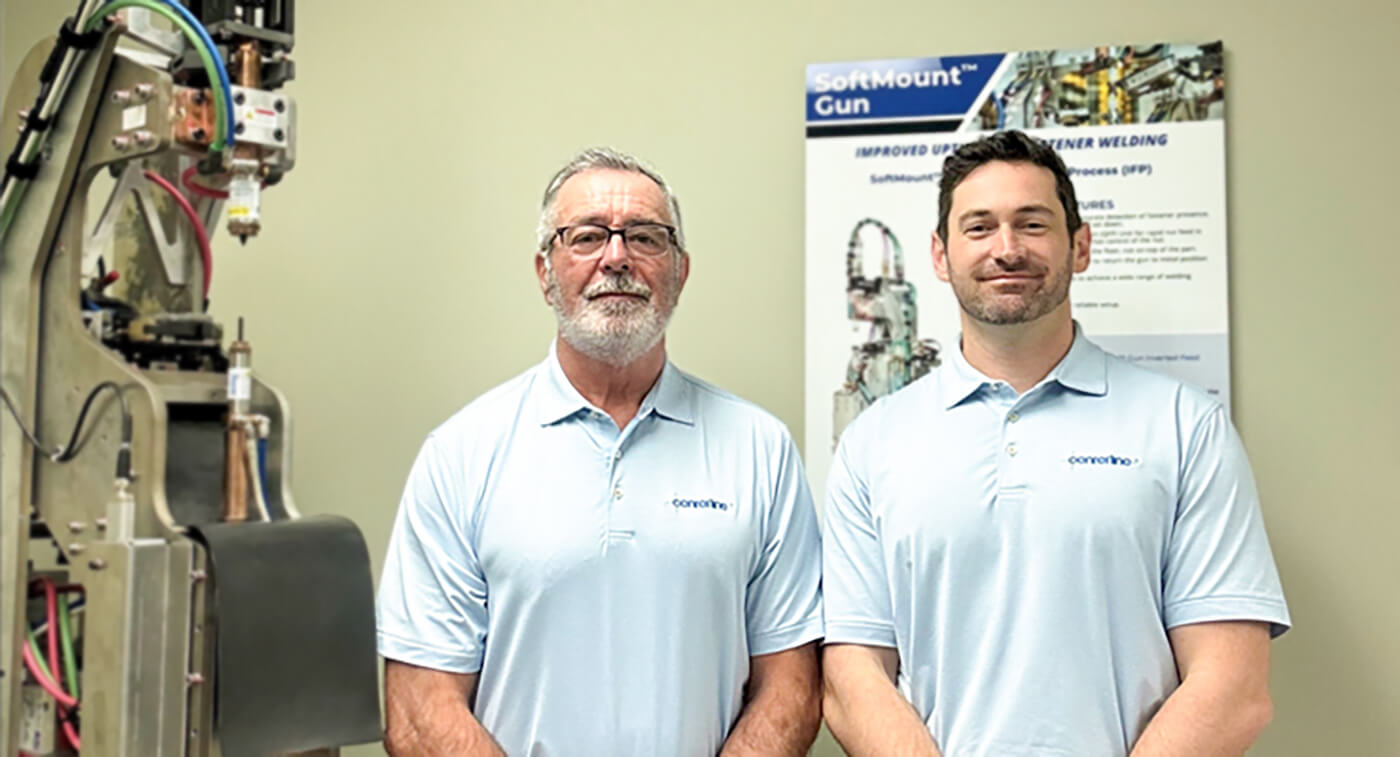
CenterLine’s Southeast location is based in Birmingham, AL and headed by Stuart Rogers (left) and David Rogers (right). They have 50 years of combined experience in the automotive industry. Stuart’s journey began as an electrical engineer, honing his expertise in resistance welding and contributing significantly to CenterLine’s growth over his 14-year tenure. On the other hand, Stuart’s son, David, equipped with a Marketing degree from the University of Alabama, delved into robot programming and worked with various joining technologies before joining CenterLine’s Account Management team in 2018. Stuart and David are strategically based in the Southeast, as this is a central location that allows them to respond quickly to our customers’ needs.
Based in Windsor, Canada, CenterLine is a privately held corporation specializing in advanced automation processes and joining technologies tailored to welding, joining, metal forming, and cold spray applications. As a vertically integrated enterprise, we provide a wide range of product offerings to OEMs, Tier Suppliers, and Integrators in the automotive, mass transit, aerospace, and defense industries to meet their global market demands.
Aside from our North American operations in Windsor, Ontario; Birmingham, Alabama; and Queretaro, Mexico, we have manufacturing and service support facilities in Brazil, Germany, Romania, India, and China to support our customers’ international operations.
If you are facing challenges with inline robotic fastener welding, locating the stamping, and welding the fastener concentric to the hole, CenterLine offers innovative solutions for fastener projection welding. Our solutions provide process monitoring, consistent pushout force, and maintaining concentricity between the fastener and the stamping hole without the risk of expulsions in the threads.
Consistent inline robotic projection welding offers manufacturers a cost and quality advantage over traditional operator-loaded press welders. The days of keeping a broom outside the cell to nudge a part stuck on the weld pin are gone! That is why we have developed an optimal solution, the SoftMount™ Gun.
The SoftMount™ Gun is designed to mechanically fine-adjust its position to a stamped hole to weld a fastener consistently. Its compliance feature and the entire design have been optimized to create the best balance between stability and ease of movement. The gun is available in two configurations:
- The Inverted Feed Process (IFP), where the fasteners are fed in the inverted orientation, with the projections facing up.
- The Standard Feed Process (SFP), where the fasteners are fed in the most common orientation, with the projections facing down.
To further enhance the gun’s productivity, we have developed two fastener delivery systems:
- The Patented Quick Fastener Placement (QFP), which provides a positive handoff of the inverted fastener (nut) to the moveable electrode.
- The Upper Stud Feeder (USF), which feeds stud fasteners to the upper electrode.
Both systems are designed to feed the fastener to the electrode while the robot is locating the workpiece to the weld position. This buries the fastener’s feed time, thus reducing the cycle time and improving overall efficiency.
The SoftMount™ Gun is an alternative to expensive and dedicated Capacitive Discharge Welders. The Controlled Pulse Resistance Welding (CPRW) process with our Dynamic Response Module (DRM) for fast follow-up ensures consistent and efficient projection welding of high-yield and hot-stamped materials, providing superior quality using standard MFDC weld controls.
For more detailed information and inquiries, do not hesitate to contact Stuart Rogers or David Rogers at our local sales and service office in Birmingham by calling 205-310-9103 or emailing [email protected].