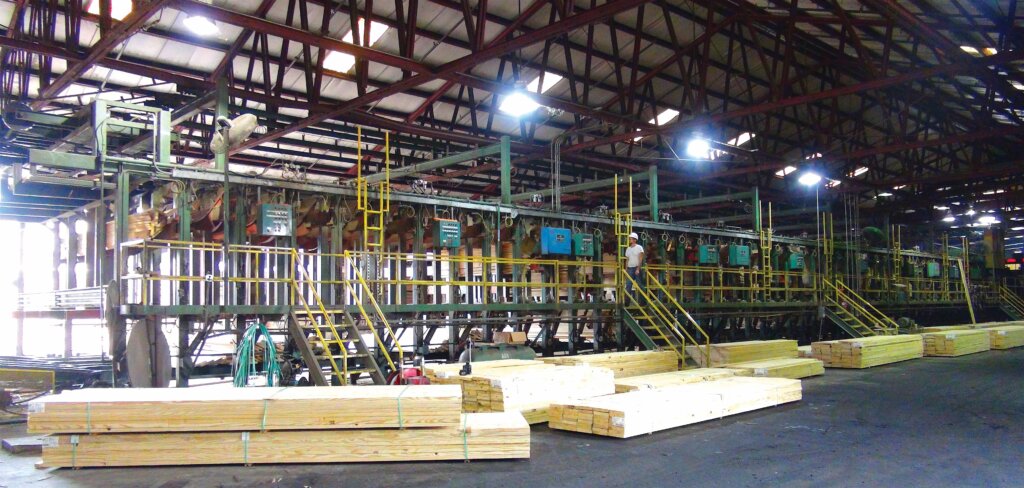
This year, T.R. Miller Mill Co. turns 150 years old.
Let that sink in.
One hundred and fifty years ago, Ulysses S. Grant was president of the United States, the newly invented internal combustion engine was all the rage, and mill acreage was purchased near Brewton, 46 years before Brewton was Brewton.
Today, with about 208 workers, T.R. Miller Mill Co. is one of the 150 largest softwood lumber producers in America. It is also one of the oldest privately held forest product companies in business today. But to understand this hometown success story, one must understand its history, beginning seven years after the U.S. Civil War.
“When we hire people, they have to hear our story,” says the company’s human resources director, Michael Baty. “We believe this is one of the best companies to work for in the area. Our history illustrates that. It is part of our culture.”
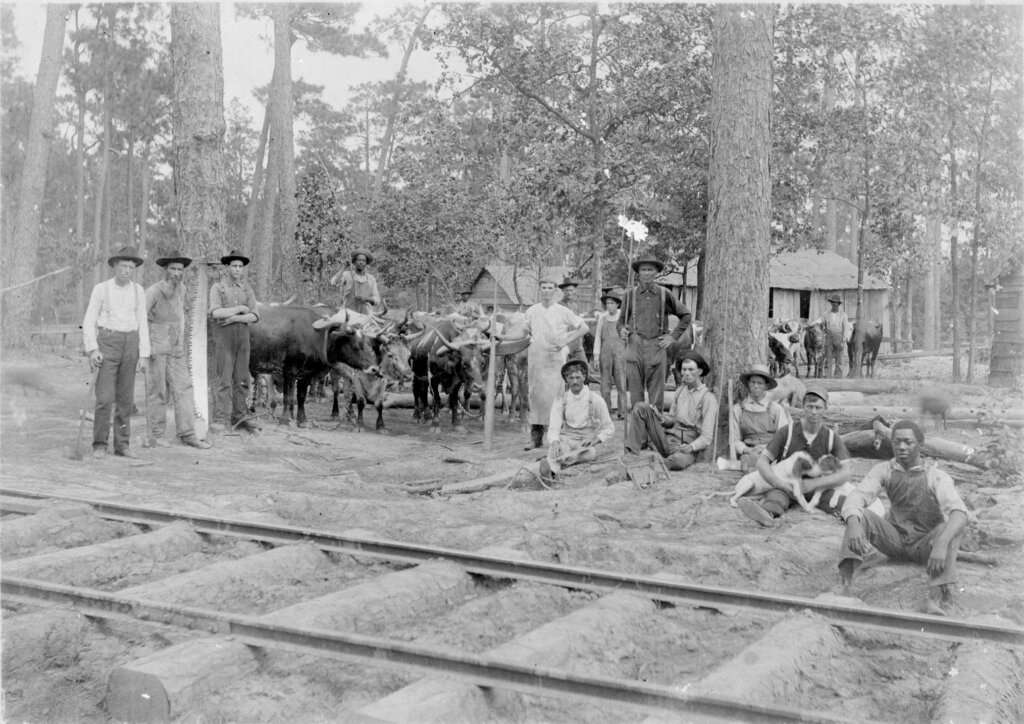
The tale begins as Cedar Creek Mill Co., with a land purchase by Elisha Downing on June 26, 1872. The rest is history — 150 years’ worth.
A working mill was already in place on Downing’s acquisition, three miles from present day Brewton. But little is known about the pre-1872 days.
Downing developed and operated the fledgling business until 1899. He then sold the company to his son, Wiley Downing, and Thomas Richard (T.R.) Miller and Francis C. Brent. The latter two had been a captive audience, literally.
“Earlier in their lives, Brent and Miller were Confederate prisoners of war held in the same prison,” says Thomas E. McMillan Jr., former director of T.R. Miller Mill Co., and author of “Logging the Mill.” “We are not sure if they knew each other back then.”
With the team in place, operations continued. “Originally, logs were obtained by oxen pulling carts,” notes McMillan, who is also partner and director of PMT Publishing. The lifeblood of the wood mill, like all mills of the day, was the network of creeks and rivers used for wood transportation. “Logs were off-loaded from ox carts and floated down Cedar Creek,” recalls the company’s former director.
Actually, it was more than off-loading — it was an art. While traveling down the creek, each log was turned “butt-end” first for mill delivery. Log turners were tasked with keeping the logs straight as they flowed downstream.
The men balanced, walked on and jumped from log to log, agile as cats, as the procession moved downstream. According to early company records, good log turners never got their feet wet.
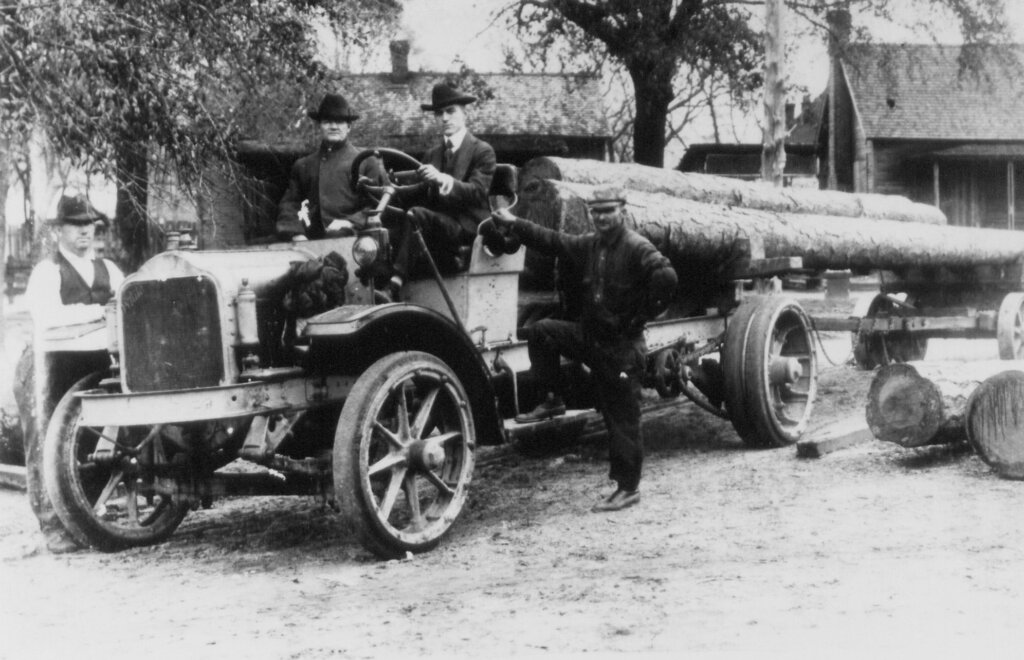
But in the late 1800s and early 1900s the future was upon us, including ox-free deliveries. The ever-trusty beasts of burden, who never questioned company benefits, were phased out in the 1940s.
In 1892, the company’s main site moved to Brewton, then 7 years old. The flagship location started Brewton operations as a steam-operated mill. After several changes in ownership and various land purchases the company became the T.R. Miller Mill Co.
Rail transportation became the primary means of log transit in 1905 and continued until about 1940, when trucks became Miller’s principal hauler for raw materials and finished lumber.
The Brewton company was not without challengers. Southern yellow pine to Alabama was like the Gold Rush to Alaska — highly sought and perpetually valuable. The lumber business back then, like today, was highly competitive. T.R. Miller persevered where others did not.
“At one time there were at least 27 other sawmills around here,” recalls McMillan. “But others only had the means to cut nearby timber within about a three-mile radius.” Oxen could not travel much past that distance, he adds.
McMillan continues, “In addition, all of those mills were located on or near a creek, which was relied on for log transport. Creeks were not always dependable.”
Occasionally, mills delayed or ceased production due to drought. Operations often shut down as companies waited for a good rain.
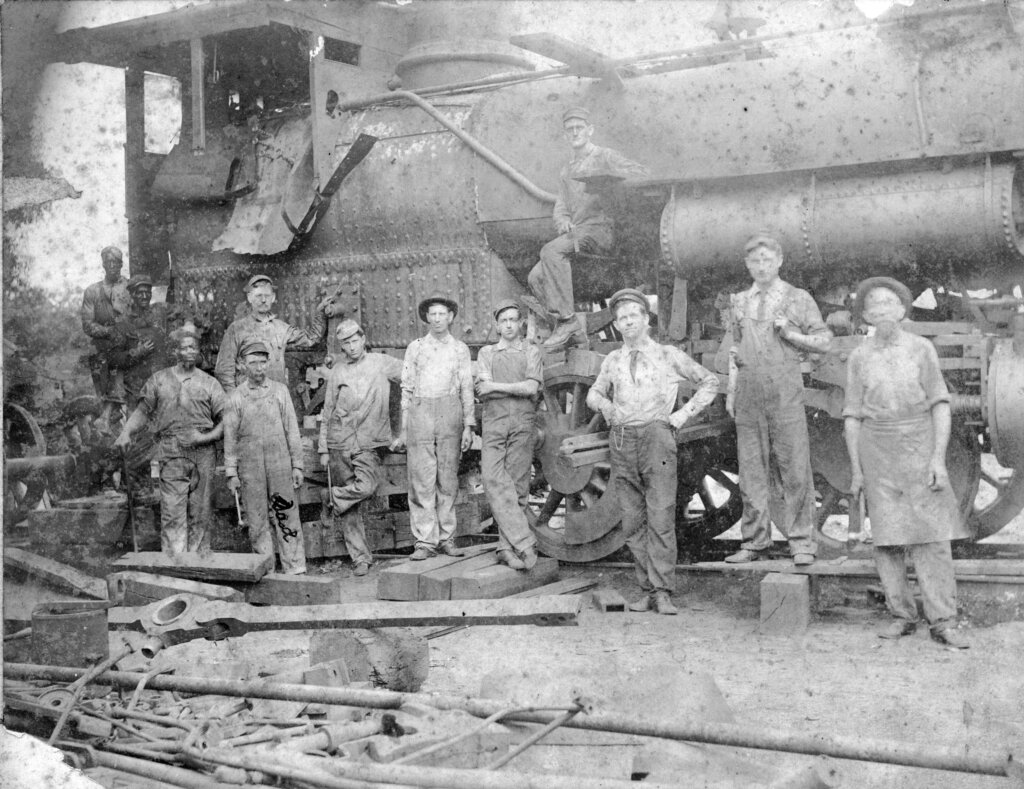
“T.R. Miller saw the value of trains and trucks and the necessity to reach out greater distances for timber,” says McMillan. “He also recognized the value of good environmental practices, which also helped the business. While other mills practiced ‘cut and move on,’ Miller replanted his forests.”
In the early days, most of the finished lumber products were transported to Pensacola, Florida, where they were loaded on barges for European customers eagerly waiting across the Atlantic. Today, most of the company’s products are sold domestically.
Since its founding, T.R. Miller Mill Co. has been a family-owned business. Today the primary owners are the Miller, McMillan and W.T. Neal families. Other prominent area families had administrative and/or ownership stakes over the years. Familiar names include Dixon, McGowin, Blacksher, Foshee and Douglas — many of the names you’ll find on Brewton streets signs.
Even if the surnames don’t match, says Baty, the employees seem like family, too. “Approximately 33% of our workforce has been with the company for over 25 years,” he says. “That is unheard of in today’s industry.”
One such employee is Ricky Stanley. Born in nearby Atmore, Stanley moved to Brewton at age 15. He graduated from T.R. Miller High School, named for the mill he would one would day lead as president and CEO.
“I hired into the research and development department of the box plant,” recalls Stanley, a 40-year employee. “I designed wire bound boxes and industrial products.” In 2016 he was named president. He believes T.R. Miller’s opportunities are available to all employees.
“We are a private company where everyone is a person,” says Stanley. “We each have different responsibilities but at the end of the day we are here for a common goal: we make great things from southern yellow pine.”
Today’s economy is a puzzle: “The country is in an economic slowdown and inflation is the highest it has been in decades,” he says. But he remains positive. “The housing market is strong and lumber is connected to the housing market. I believe we have underbuilt housing in this country for years. The next several years should be good for us.”
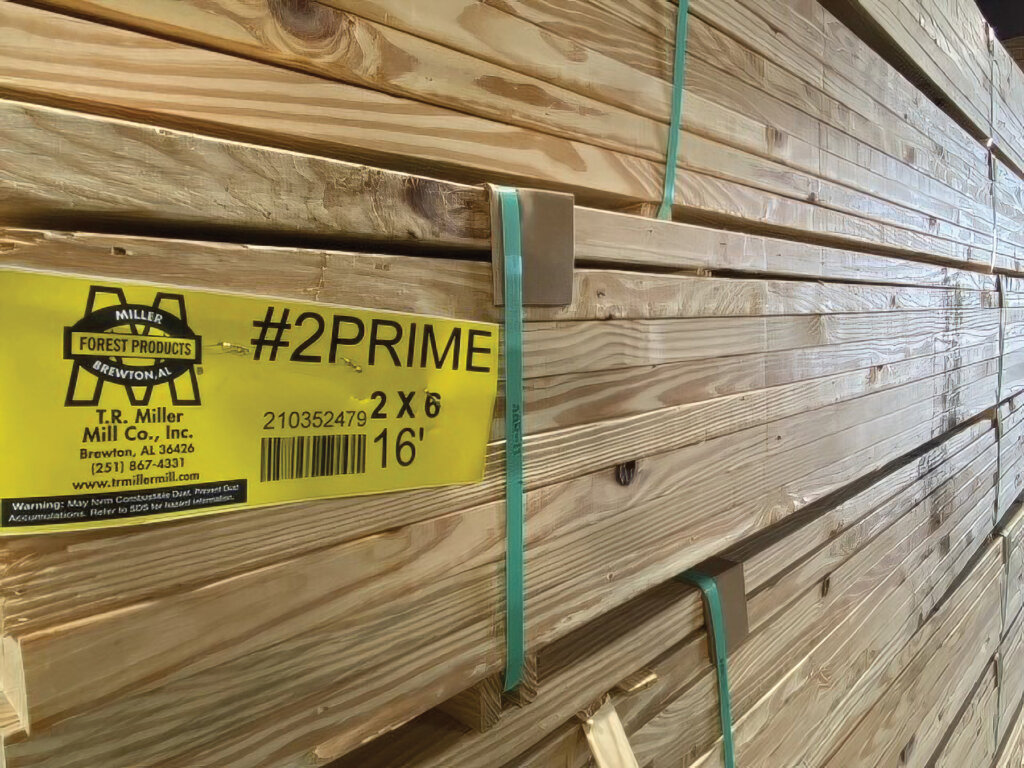
With log trucks rolling into 215 Deer St. and finished product rolling out all day, T.R. Miller Mill Co. has a promising future. The sawmill is budgeted to cut 3.2 million board feet a week, totaling approximately 165 million board feet for the year. In addition, Miller manufactures about 100,000 utility poles annually — one-sixth of the U.S. market.
T.R. Miller’s production schedule is ambitious. It always has been. But not to worry — the company has 150 years of experience.
Emmett Burnett is a Satsuma-based freelancer for Business Alabama.
This article appears in the July 2022 issue of Business Alabama.