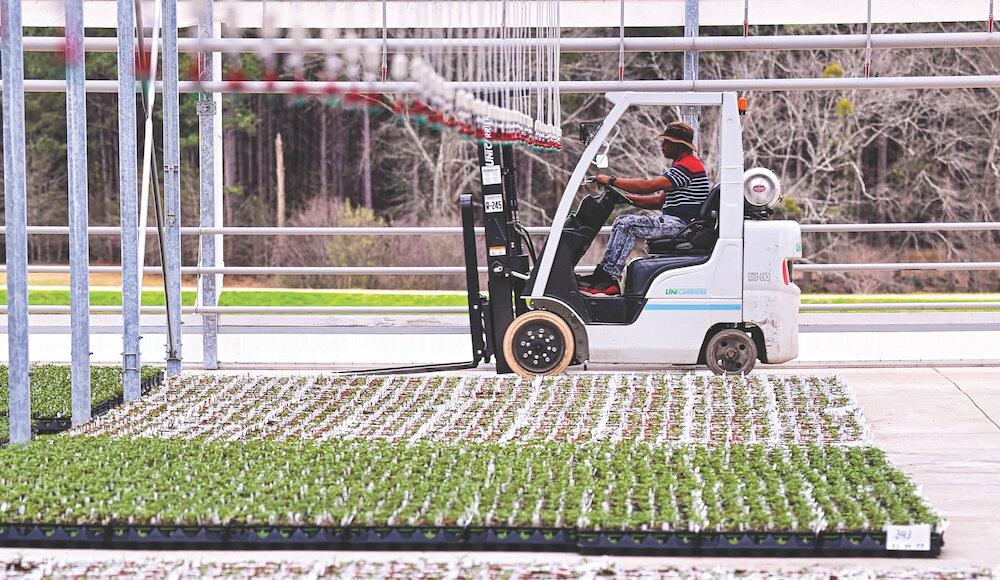
The sign in front of the Bonnie Plants facility in Union Springs proclaims, “Our roots run deep.” Indeed, the history of the company dates all the way back to 1918, when Livingston and Bonnie Paulk planted two pounds of cabbage seeds in their backyard garden and sold the ensuing produce.
More than a century later, those deep roots support a thriving business that has branched far beyond its humble Union Springs origins. Bonnie Plants is now the largest grower of vegetable and herb plants for home gardens in the United States, with 87 facilities across the country producing nearly 30 million flats annually. The company supplies approximately 17,000 retail accounts and generates annual sales revenue of more than $400 million.
Still, despite all this growth, Bonnie Plants maintains a major presence in tiny Union Springs, located 45 miles southeast of Montgomery in rural Bullock County. In fact, the company is digging even more firmly into the local soil. While the headquarters moved to Opelika at the beginning of this year, that opened up space in Union Springs for a $17 million greenhouse upgrade, along with expansion of the company’s e-commerce distribution facility.
“We had exhausted the office space here, so it was time for a new home,” says Sidney Phelps, who is director of e-commerce and a self-proclaimed “third-generation Bonnie kid” who has been with the company for nearly 23 years. “Union Springs is a little bit off the beaten path. Opelika makes it easier for our retail clients to come in and have meetings with us.
“But there was never a point where we were taking any of the production and heart of the business away from Bullock County. This is where all that takes place. This is the biggest investment Bonnie has made in a long time, and it’s the most state-of-the-art facility we have.”
The new layout includes 305,000 square feet of natural-ventilation greenhouses, equipped with high-tech temperature and irrigation controls. Each greenhouse is connected to a 7,800-square-foot production complex and a 45,900-square-foot distribution warehouse, all tied together as one facility.
“We had been expanding for years in different pieces, and we started having all these little subsets that weren’t connected,” Phelps says. “You had to go here, there and everywhere to accomplish one task. With this setup, everything is connected on a 7-acre concrete pad, and it’s much more efficient.”
Phelps says the greenhouse facility makes it possible for Bonnie to produce an even greater variety of products, including succulents, flowers and house plants. Meanwhile, the new e-commerce warehouse is making it easier for the company to ship all those new items. According to Bonnie Plants, these expanded operations have resulted in an increase of 60 jobs, bringing the total number of workers (including part-time) to more than 200.
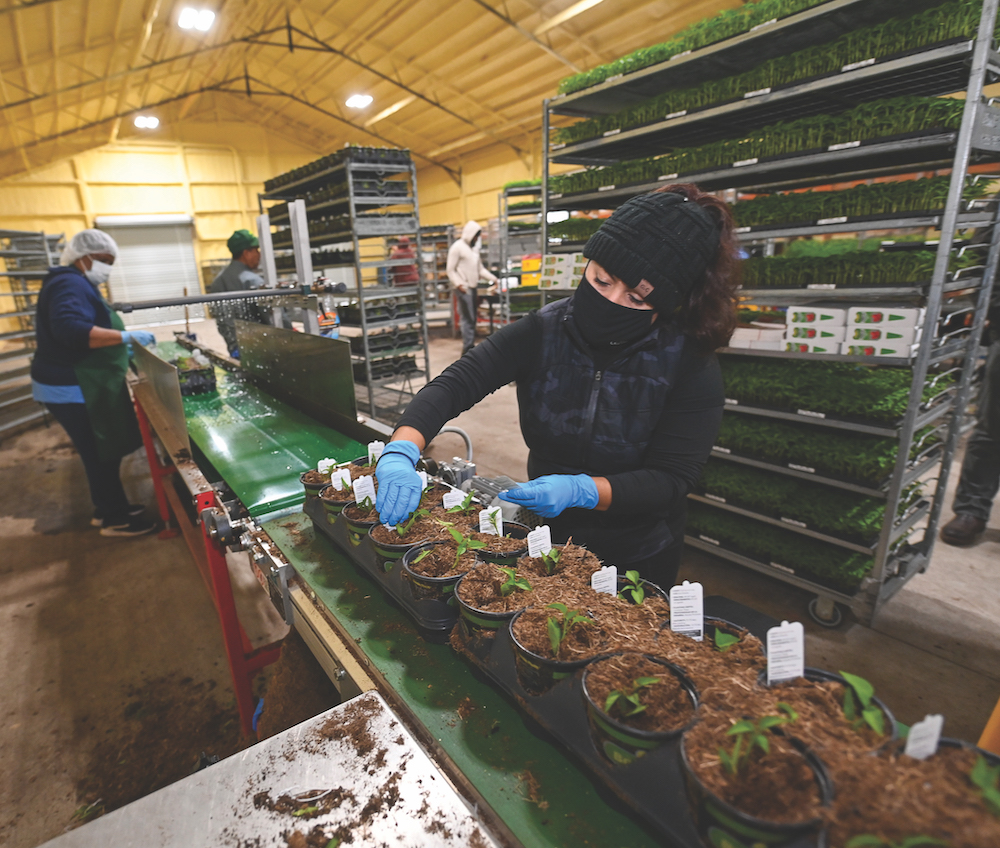
“From innovative new products to increased e-commerce demand, this investment is all about creating an experience that will enhance the lives of our consumers better than ever before,” says Bonnie Plants President and CEO Mike Sutterer, who took over the company in January of 2020 after two decades with Scotts Miracle-Gro. “Not only have we improved how we produce and distribute vegetable and herb plants, but … this modern facility makes it possible to grow and deliver any live good any time of the year.”
The temperature control alone makes the new greenhouse a modern marvel. A weather station on top of the structure analyzes the conditions and automatically makes any needed changes to the interior temperature.
If it gets too cold outside, a steam-heat system located along the top and sides of the greenhouse provides warmth. Then when the outside temperature starts to rise, a three-tier cooling technique keeps the plants comfortable. First, the side curtains roll up to allow for better air circulation. If that doesn’t provide enough ventilation, the roof opens. Finally, a retractable shade is brought out to shield the plants from the direct sunlight of an Alabama August.
“This way, you’re not just forcing in air to try to cool everything off,” Phelps says. “It keeps the temperature inside the greenhouse much more stable, so the plants aren’t under as much stress, which makes for a healthier plant.”
In addition, the weather station can detect whenever an approaching storm is within 15 minutes of the site. When that happens, the system automatically starts closing all the openings to the greenhouse. “And we can run all this from an iPhone,” Phelps says.
The greenhouse also is equipped with an automated irrigation system. And the overall space is better utilized, allowing for more than 7,000 hanging baskets to be positioned above the rows upon rows of flats arranged along the floor.
Next to the greenhouse is the new e-commerce fulfillment center, which handles packaging and shipment of all the orders from the Bonnie Plants website, as well as from the company’s retail partners. Only part of the 2.2-acre facility currently is being used, but the company is so confident its e-commerce program will continue to expand — it has grown 860% over the past three years — that there already is an additional 3-acre pad ready for future development.
“We also have smaller fulfillment sites in Ohio, New York, California and Utah. So we can touch 95% of the country within two days,” Phelps says. “We eventually want to be the Amazon fulfillment of live goods.”
While all this is taking place in Union Springs, the company’s executive leadership and other officials are settling into their new headquarters in Opelika. To evoke Bonnie’s agriculture nature, the headquarters building resembles a farmhouse and it is filled with sustainable features, including a 10-foot-high, indoor living-plant wall designed to purify air in the office.
Phelps says the move to Opelika allows Bonnie Plants to have a presence near Auburn University, which has teamed with the company on two endowed scholarships. “Considering the partnerships we have with Auburn, moving the corporate headquarters (to neighboring Opelika) is a great fit,” Phelps says.
One of the scholarships is with the College of Agriculture for a student majoring in horticulture, and the other is with the Harbert College of Business focusing on business analytics and supply chain. Bonnie also recently donated $1.2 million toward the development of a 2-acre Children’s Garden at Auburn, providing hands-on learning about how to grow and care for plants.
“Everything we have been doing lately is all part of our mission to create the best products we can to impact people’s lives daily,” Phelps says. “We’re not just putting a plant in a box. We’re actually having a positive effect on someone’s life every day.”
Cary Estes and Julie Bennett are freelance contributors to Business Alabama. He is based in Birmingham and she in Auburn.
This story originally appeared in the July 2022 issue of Business Alabama.