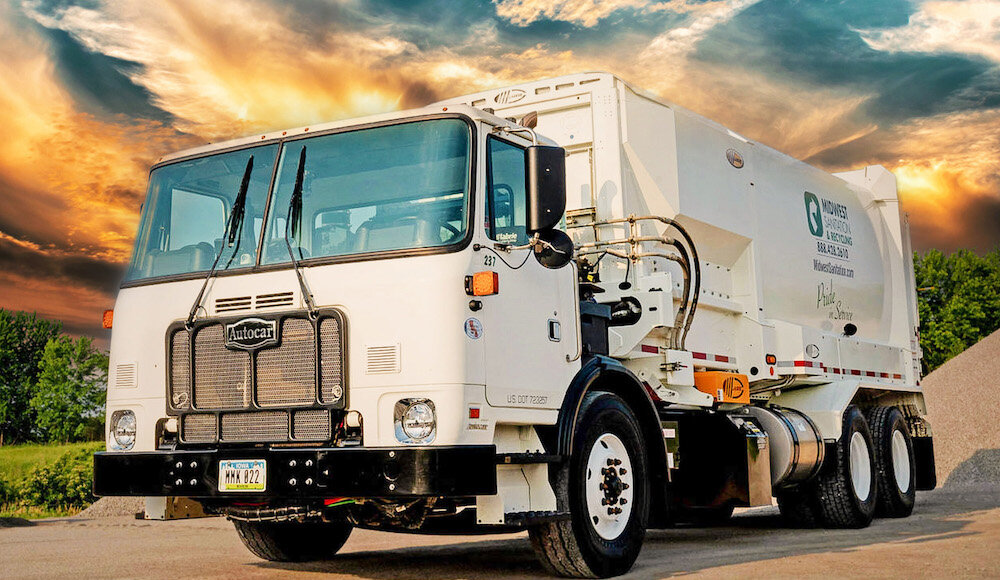
Autocar built the first motor truck commercially available in the United States in 1899 to carry packages during the height of the industrial revolution.
The delivery wagon was “purpose-built,” boasting a payload capacity of 700 pounds, offering 5- or 8-horsepower motors and featuring an “engine-under-the-seat” design that maximized area for freight — a precursor of Autocar’s Cab-Over-Engine design used on every Autocar truck today.
In fact, 125 years later, Autocar LLC remains a 100% American-owned private company that prides itself on custom engineering and innovation in manufacturing premium, severe-duty vocational trucks. Many of these are built right here in Alabama, at Autocar’s headquarters in a sprawling complex just off Pinson Valley Parkway near Birmingham. The company operates an additional manufacturing location in Hagerstown, Indiana.
“I often get asked why the company is called Autocar, since we only make trucks these days,” says Tim Thornton, vice president and general manager refuse at Autocar. “But it started out as a car company and was pretty inventive…developing something called the rear reduction axle, then the double rear reduction axle. Now this double rear reduction axle could carry a very heavy payload under very low horsepower without losing speed, so [Autocar] quickly had a significant niche and competitive advantage in the hauling space. They really had such a competitive advantage that they quit making cars altogether and just became a truck company.”
And not just any truck company. Early on, company leaders recognized the need for quality, customizable, reliable trucks, and have built on their innovations to nurture a direct relationship with customers to “exceed their expectations.” What sets the Autocar vehicles apart is that they are not built on a standard assembly line, but rather one at a time, for specific applications.
Officials say the vocational trucks coming out of Autocar’s facilities support America’s economic infrastructure by providing critical tools for waste collection, transportation and logistics, construction and concrete sectors. Importantly, the company is not set up by vehicle platform but by vocation, making its obsessive drive to solve specific vocational jobs possible.
The two main vehicles made at the Birmingham location are the ACX Severe Duty Cabover, used mainly for refuse collection and pumping concrete, and the DC-64 Severe Duty Conventional Class 8 work truck, built from the ground up with every detail custom-engineered for a variety of commercial applications.
“We pride ourselves on being a customer-centric company,” says Thornton. “But what does that really mean? What’s very unique about us is we’re very hands-on, very engaged with the end customer that’s using the truck, and we don’t hand it off to a dealer to do that work for us. We work with dealers and we sell through dealers, but we’re very engaged directly with our end customer base. We try to understand our customer and what they need and build a vehicle that is very specific to that customer’s needs and applications.”
This means that the people building each vehicle understand ahead of time what it will be used for and what specific additional machinery will need to be added to the vehicle. By taking this approach, he says, it makes for a better integration of specialty equipment and a more reliable end product.
“We have our trucks essentially connector ready so that when it goes to the upfitter, the wiring harnesses, hoses and splices are already installed and everything is pre-configured,” says Thornton. “And we’re really the only company that does this level of integration.”
“And when we say we’re a vocational truck manufacturer, we truly are vocational, which means we make things pretty much in any configuration that you can think of,” he adds. “Automated side loaders, rear loaders, front-end loaders, roll-off trucks…. we make them in both conventional and cab-overs. We’ve done concrete belt-conveyor trucks, dump trucks, fuel tankers, cargo lifts, bucket cranes. We do rear discharge mixers, terminal tractors, paint strippers, water blasters, dump trucks, street sweepers…you name it.”
“With our diversity of applications, we sell to a lot of different types of companies and organizations,” says Thornton. “We even sell to the city of Birmingham, which runs our ACX in an automated side-loader application with a higher body on it.”
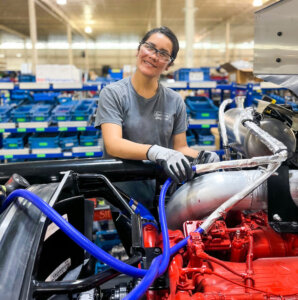
Powering the Future
The Birmingham facility recently added a dedicated EV component assembly line to ensure the best power unit and battery pack build quality for better zero-emission vehicles in the commercial space.
In fact, Autocar introduced electric vehicles almost 100 years ago and offered electric options for commercial use in the 1920s. Autocar LLC remains an industry leader in green innovation, developing several all-electric zero-emission vocational vehicles including an industry-leading E-ACX.
“We keep all of that fairly confidential and proprietary because we think we’ve created a competitive advantage in the development and the unique innovations that we’ve been able to do,” says Thornton. “We’re still in the infancy stage of going into those markets, but I will say that our E-ACX refuse truck that’s running in the field is outperforming every other truck that’s been tested. Essentially, we’re being told from customers and people who are running it that our truck — from a range and payload performance — is better than any truck they’ve seen, so that’s really encouraging. But we haven’t officially launched that product yet, but we plan to do a full launch soon.”
Jennifer G. Williams is a freelance contributor to Business Alabama. She is based in Hartselle.
This article appears in the March 2024 issue of Business Alabama.