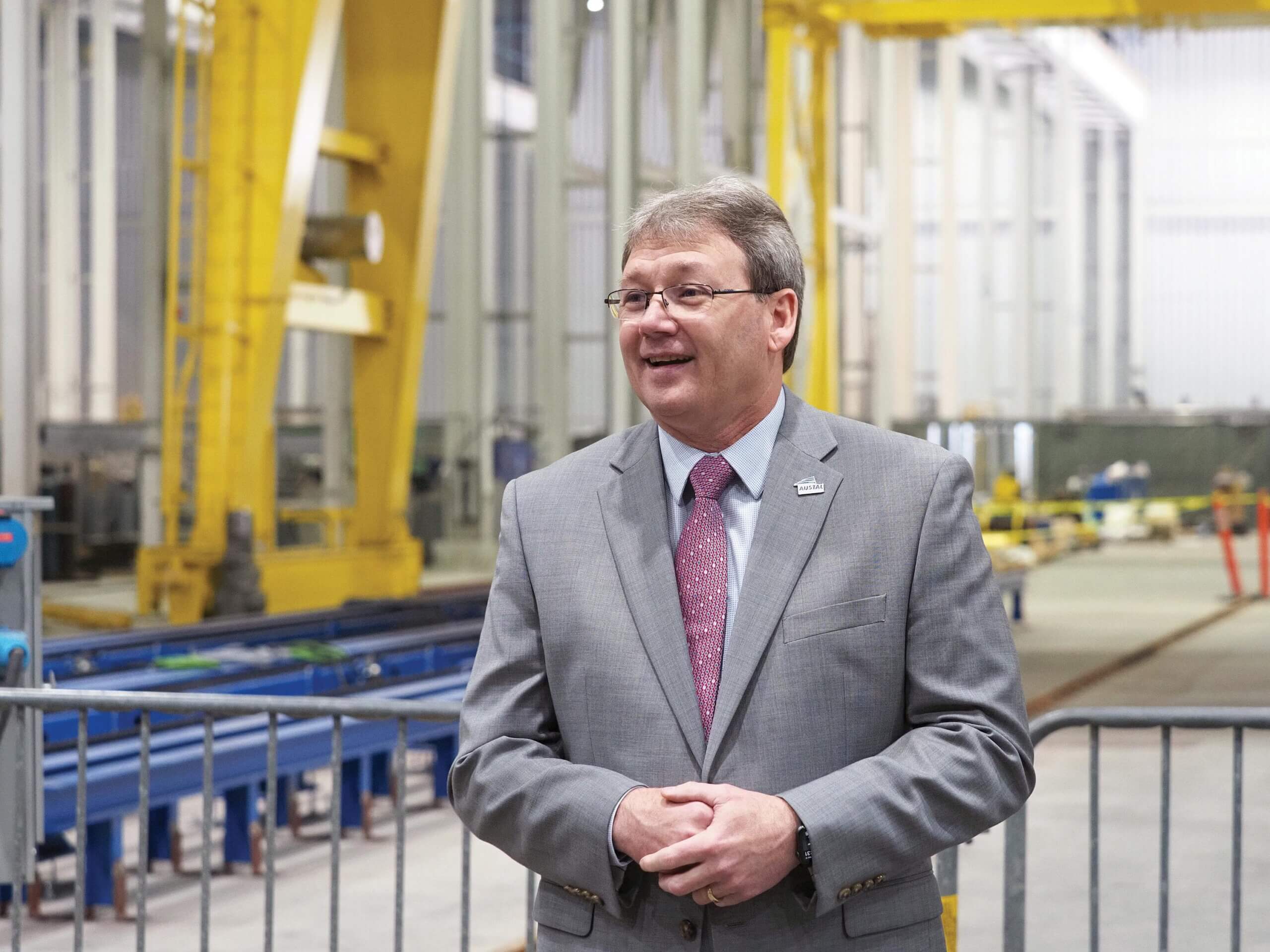
In late April, Austal USA opened a steel manufacturing line right next door to the aluminum shipbuilding lines it has operated for more than 20 years.
“In some ways it’s a seismic shift; in some ways it’s just a logical progression,” says Larry Ryder, vice president for business development and external affairs.
The addition makes Austal “the only yard in the U.S. that can build full-blown warfighter ships in aluminum or steel,” said Austal USA President Rusty Murdaugh at the opening ceremonies for the new line.
Opening in 1999 with about 100 employees, the company has grown to about 2,700 employees now, waxing and waning with government contracts but always among Mobile County’s largest industrial employers.
Its aluminum manufacturing facilities have grown from the 90×60 assembly bay to four final assembly bays, a 700,000-square-foot Module Manufacturing Facility and support structures on 165 acres on the Mobile River, just across the water from downtown.
In the last 20 years, it has delivered 27 ships to the Navy.
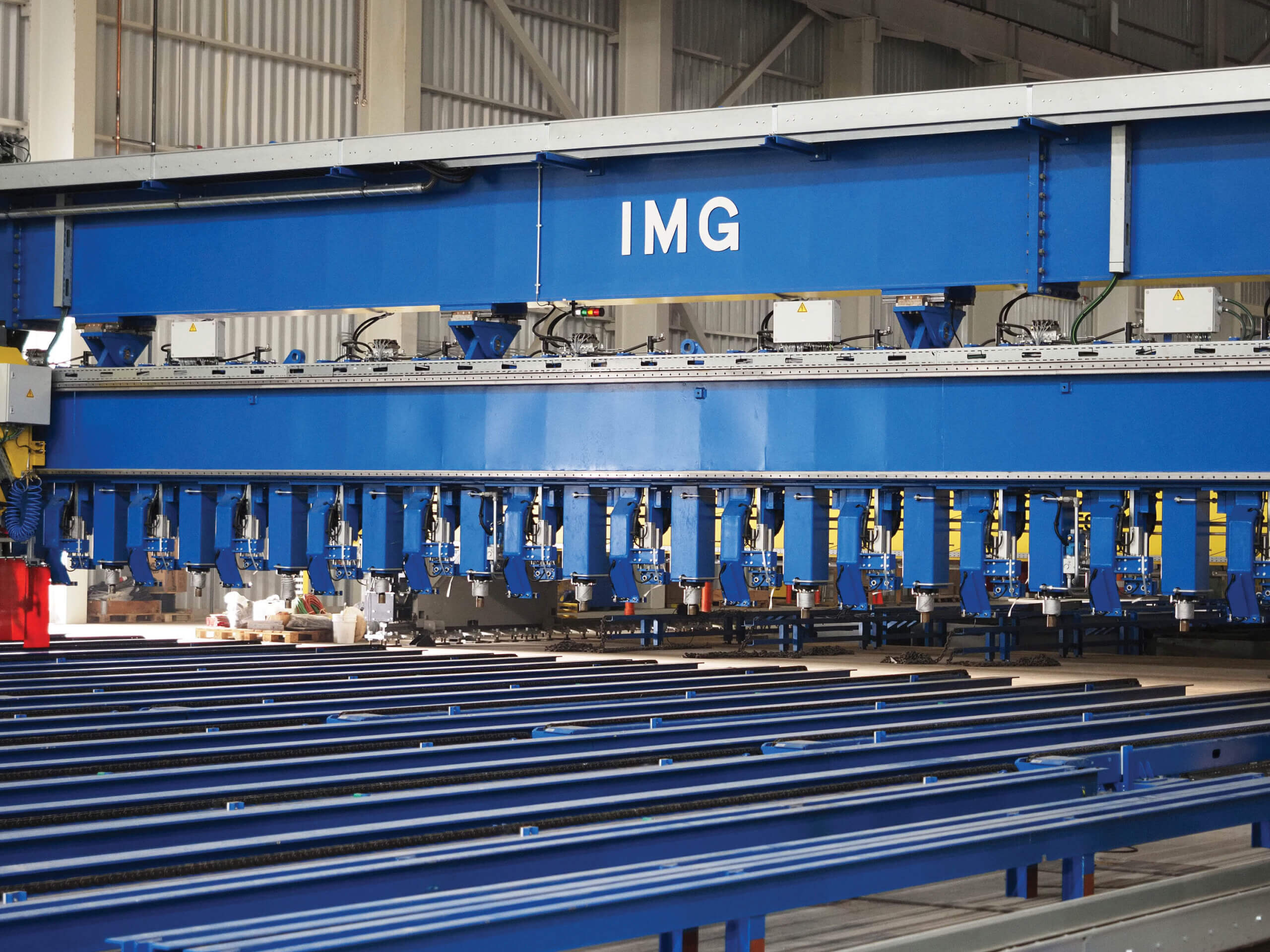
Now a steel line hums beside the others.
“It’s a really significant change for the company,” Ryder says. “It gives us new markets. But in some ways, it’s just continuing what we’ve been doing — building quality ships on time and on budget.”
When Austal, subsidiary of Australian firm Austal Ltd., first dipped its toes in the U.S. Navy marketplace, the Navy wanted aluminum-hulled ships, which are faster and, because of their shallower draft, able to function in shallower water.
Now the Navy is prioritizing qualities best found in steel ships, enough so that Austal received $50 million in Department of Defense funding to add the new capability.
“It’s not a transition,” Ryder adds. “It’s an addition.”
And the Navy has responded warmly, sending senior officials to the opening ceremonies for the new steel line.
Already a Towing, Salvage and Rescue Ship is under contract and the firm is competing on several more contracts including a frigate class option.
Adding an entirely new capability would not be easy, says Mike Bell, senior vice president of operations, except that “Austal was really, really smart in the way it laid out the campus, setting it up to be a lean manufacturing facility.”
Says Bell, “Other yards build a ship; we manufacture a ship.”
The distinction is the adherence to lean manufacturing technics. Workspace and tools are organized just so. Individual workers check their own work and carry responsibility for its quality. “And the product itself flows in a way that gives us flexibility to build a lot of different things.”
“To go from aluminum to steel, we had to add a steel line,” says Bell. “But all other processes are the same with only minor changes.” For electricians and machinists, for example, the work is the same.
Welding steel is easier than welding aluminum, he says, so it’s easy for welders to transition. All the aluminum welders were specially trained by Austal and AIDT. But all are capable of transitioning to steel if need be.
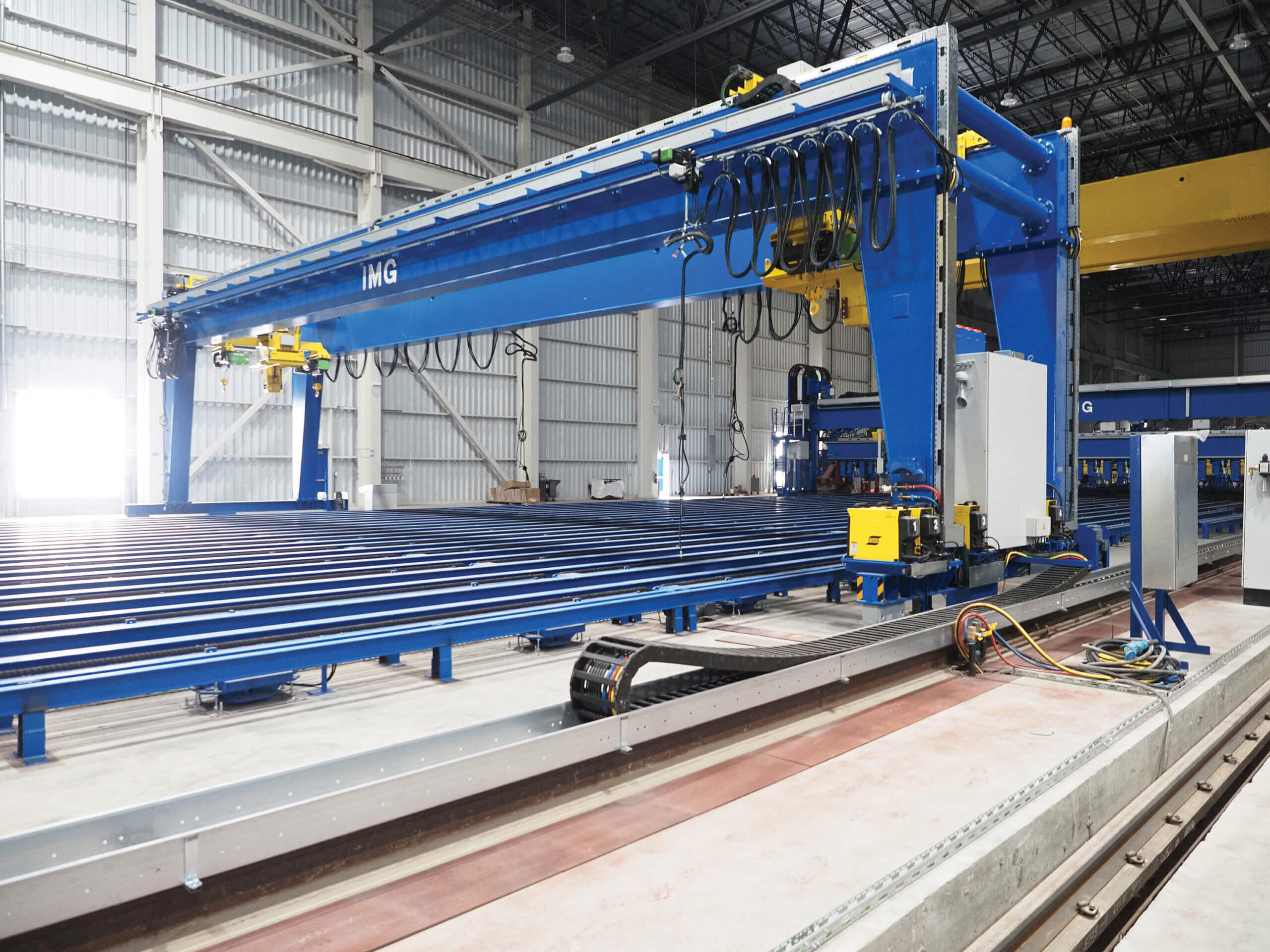
Early work on steel ships will be much more automated than the present aluminum line, with plates cut, bent and initial welding done through robotics.
Next, pieces move to the Modular Manufacturing Facility, where they are transformed into a module; then more welding, piping, electrical, machinery, fit outs, insulation and painting. And then out of the MMF for final assembly.
With the new capabilities, says Bell, “We’ll be able to bid on anything but submarines or aircraft carriers.”
In fact, Austal is working on elevators for aircraft carriers — support work for the enormous shipbuilders who have chosen to build the enormous carrier craft.
How does the new capability affect business prospects?
“Manufacturing is always feast or famine,” says Bell. But the firm is actively bidding multiple contracts in steel and just was awarded another aluminum ship contract.
He expects employment to head back to the high 3,000s.
“Our training program is really robust,” Bell says. “We take people who’ve never done manufacturing — we were taking people from McDonald’s and lawn care — and 12 weeks later they were welding…. Our workforce is very young, but they are by far the best shipbuilders in the nation.”
Over the last 40 plus years, he has watched the number of master craftsmen dwindle as everyone seemed to prefer a college-based career. But that has been swinging back. “Now we have master craftsmen in every line.”
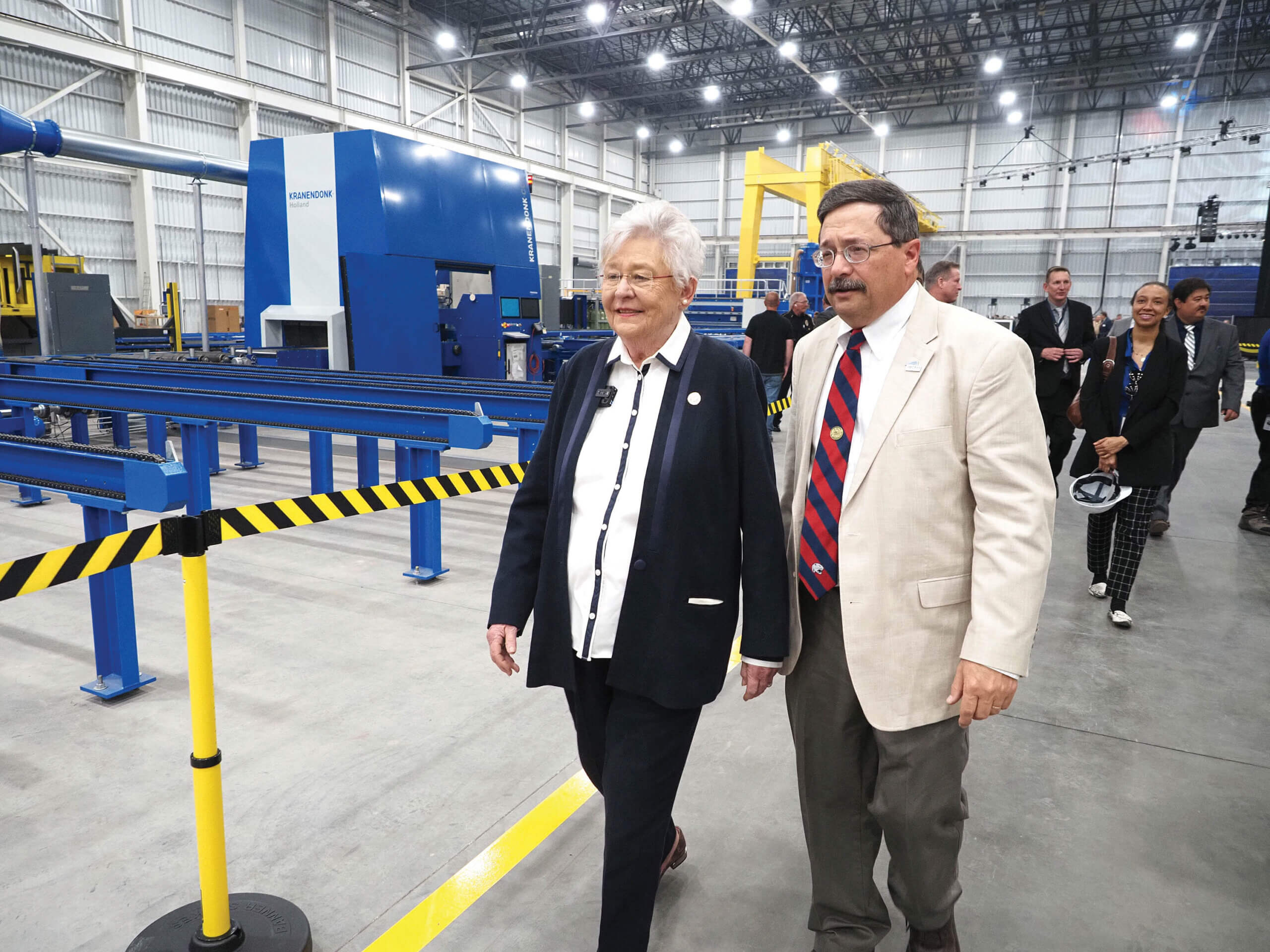
Steel to feed the new line will be coming less than 25 miles from the SSAB plant in Axis, just upriver from Mobile. “It wasn’t hard to find a supplier,” Bell says, “but we’re not like a traditional yard with acres and acres of space. We only cut about two days’ worth of material.” So, it relies on just-in-time delivery, which suited SSAB just fine.
Like Ryder, Bell believes that addition of steel is just a logical step, taking advantage of the flexibility that lean manufacturing allows.
“Henry Ford revolutionized manufacturing by setting up the assembly line,” Bell says. He could build Model Ts quickly, but every vehicle was the same.
“Lean manufacturing takes what Ford did and changes it to give you the flexibility to get low production costs with the flexibility you need to do whatever you have to do.”
Buzz around the plant is entirely positive, he says.
“My team is looking forward to cutting that first piece [slated for late June or early July] and getting that first steel ship in the water.”
Nedra Bloom is copy editor for Business Alabama and Mike Kittrell is a freelance contributor.
This article appeared in the June 2022 issue of Business Alabama.