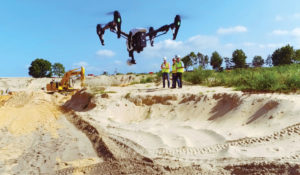
There essentially has been construction work for as long as there have been people. Creating shelters is one of the basic necessities of life, even if for centuries those projects involved little more than cutting trees and moving rocks.
While the world has moved on, in many ways the foundation of construction work has remained rooted in the past. The industry often operates like it’s the mid-20th century, which might as well be the Middle Ages, considering how rapidly technology has advanced in recent decades.
This lack of innovation in the industry is evident in the bottom line. According to an October 2018 article in Fortune magazine, construction projects regularly lose up to a third of their value due to inefficiency and waste. As a result, the industry has averaged only 1 percent annual growth over the past 20 years, compared to 2.8 percent for the global economy as a whole. The Fortune article states that if construction could increase its productivity to the level of most other sectors, the industry would experience $1.6 trillion in cost savings.
“There is a need for more technology in construction, because construction has a lot of lost efficiency that can be improved,” says Dane Pemberton, project manager at Birmingham-based BL Harbert International. “So you’re starting to see a huge movement in the tech world to push technology into construction, because they think this is a market with the most growth potential. Every year lately it feels like we make a big leap forward.”
Indeed, an industry built on brick and mortar has started to embrace programs and applications. According to a 2018 Construction Technology Trends report conducted by Software Connect, more than 80 percent of construction officials surveyed said their company was increasing the amount of money spent on technology, with double-digit percent increases on such areas as virtual design, drones, cloud-hosting software and 3D printing.
“For a long time we had technology that looked good on paper, but when you put it in the field it actually made their jobs harder,” says Eric Cleveland, IT manager for jobsite services at Birmingham’s Brasfield & Gorrie. “They’d just give data to somebody to report somewhere, and really all it did was create more work for the people on the ground.
“Now we’re finding technology that actually improves the job. These are things built for construction with the people on the ground in mind, and not just designed for the decision-makers.”
Here are some examples.
Tablets instead of paper
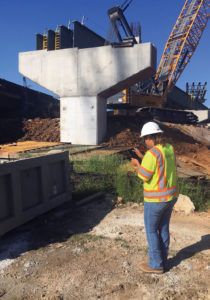
One of construction’s most common images is of several people in hardhats gathered together and looking at blueprints spread out over a barrel or box. This image is about to fade into cyberspace, as tablets and other portable electronic devices replace these paper plans.
“You’re seeing a big move away from paper,” says Adam Patterson, project manager at Mobile-based Volkert Inc. “Tablets enable you to store all your contract plans and documents on a single device onsite that is searchable and accessible and can be easily shared with everybody on your staff.”
This change will save companies both money (a single set of plans can cost nearly $1,000 to print, and multiple copies are needed) and time, since there no longer will be delays because somebody picked up the wrong set of plans or didn’t receive the updated version.
“It won’t be long before paper drawings are no longer a thing in construction,” Cleveland says.
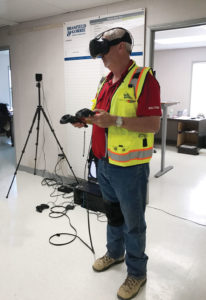
Reality Capture
One of the most challenging aspects of construction has been taking a two-dimensional plan and turning it into a three-dimensional structure. That will no longer be an issue with the increased use of Reality Capture, which can create a 3D model out of photographs or laser scans.
“Just because it looks good in 2D doesn’t mean that all the parts and pieces will fit together in 3D, especially with things like HVAC, plumbing and electrical,” says Mike Dean, director of virtual design and construction for Caddell Construction Co. in Montgomery. “But you don’t know for sure until you get out in the field. Then if there’s a problem, you have people and material and equipment sitting around as you try to solve the puzzle.
“That’s the old way. The industry has shifted and gotten better about utilizing the computer model and implementing it in the field. Now we uncover problem areas before we get to the construction phase. We’re getting closer to being able to build exactly what we design and plan without constantly revamping it.”
360 Cameras
Many hotel websites offer the ability to take a 360-degree view of one of the rooms, as well as the surrounding property. That same technology is being used in construction, enabling designers and project officials to analyze progress remotely.
“It’s Google street view for construction,” says Shawn Mancill, regional VDC manager at Brasfield & Gorrie. “It allows us to do a virtual walk-through and take care of issues that the architect or owner might have. We’ve been paying companies thousands of dollars to do progress photos. Now we can do it ourselves with a $500 camera and the software.”
Safety
The use of data analytics is enabling construction companies to better analyze what takes place onsite each day and how it might correlate with any safety issues that occur. Pemberton says Harbert recently implemented a computer program called Controlling Activity Risk and Exposure (CARE) that accumulates data through daily reports, then identifies risk areas.
“Our people in the field do safety observations, then we put the data on a chart and use the analytics to foresee possible upcoming safety hazards,” Pemberton says. “If we see a trend of people not wearing the proper safety equipment at the right times or something like that, we’ll focus our training on that area. It’s using technology to improve safety.”
Drones
According to the survey by Software Connect, more than a quarter of the industry will be using drones on a regular basis by next year to do aerial surveys of construction sites. Goldman Sachs predicts the industry will lead all commercial sectors in drone adoption, spending nearly $11 billion on the technology.
“The growth in drones has exploded,” says Mancill, who noted that Brasfield & Gorrie now has 33 licensed drone pilots. “We can fly a drone and capture the entirety of a 500-acre site in a single day. That would take three weeks for a (land) survey.”
Onsite internet access
All these technological additions won’t do the industry much good if they cannot be accessed on the construction site. And even in urban areas, it can be difficult to access the internet off anything except cellular connections, which can be spotty and often are not powerful enough.
The solution is appearing in microwave technology and point-to-point wireless Ethernet. This allows companies to take the existing internet connection in a building and wirelessly transmit the signal to a nearby construction site.
“We’ve really seen a lot of growth in that in just the last two years,” Cleveland says. “Our jobs have made such a move toward technology that so much of what we do now is dependent on the internet. The vast majority of files are stored online and shared with multiple people. They’re using project-management systems to collaborate. So getting them a good internet connection is a big deal.”
Cary Estes is a freelance contributor to Business Alabama. He is based in Birmingham.