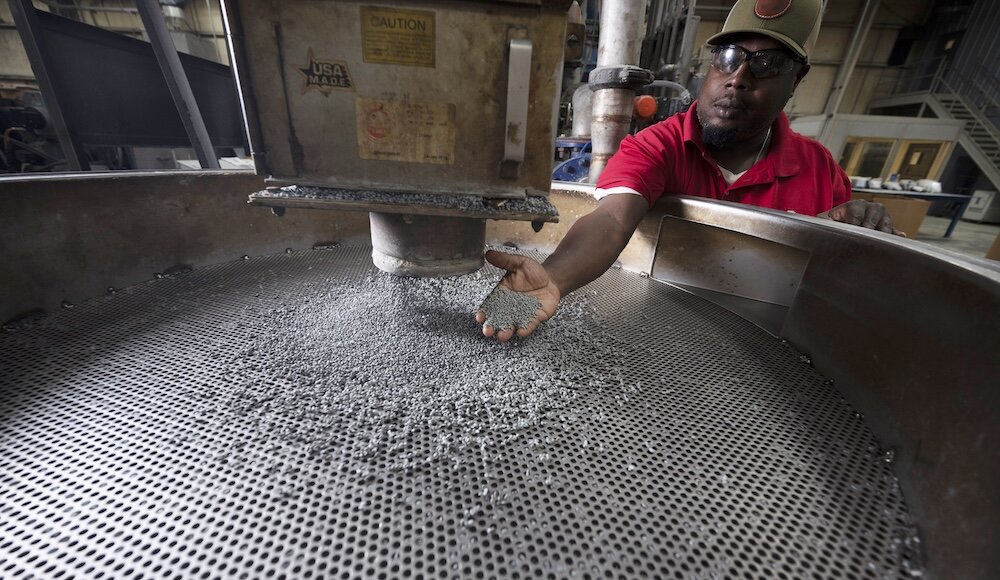
You may not be familiar with the KW Plastics name, but it’s extremely likely that plastics supplied by the Troy-based company are in your home or under the hood of your car.
“KW Plastics is the world’s largest recycler and supplier of high-density polyethylene and polypropylene recycled resins,” says Stephanie Baker, director of advocacy for KW Plastics Recycling Division. Materials produced by the company are sold to many of the most popular brands in America.
KW Plastics’ company story is one of growth and innovation, responding to market needs and developing new technologies through years of in-house research.
Formed in 1981 to recycle polypropylene (PP) plastic from used automotive battery casings, KW Plastics set out to solve the issue of safe disposal of these hazardous materials.
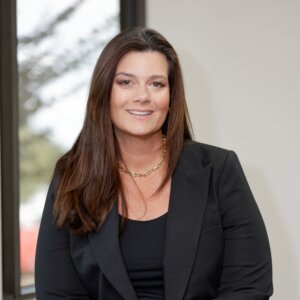
“The result was a recycled resin that fulfilled environment regulations, material specifications and offered economic savings to automotive battery manufacturers,” Baker says.
As distribution needs increased on the west coast, KW Plastics opened a second facility in the mid-1980s in Bakersfield, California, which is still operating there.
KW is part of a family of businesses, which includes the Wiley Sanders Truck Lines. The company gets its name from the first initials of its founders, Kenny Campbell and Wiley Sanders.
The initial battery casing recycling business successfully captured a large portion of the market share, and Campbell and Sanders began to look for ways to diversify and expand the business.
In the early 1990s, residential curbside recycling programs were being implemented across the U.S. The KW Plastics Recycling Division was opened in 1993 to recycle post-consumer high-density polyethylene (HDPE) — household plastic bottles like milk jugs, detergent containers and shampoo bottles — collected from these recycling programs. In 1998, KW Plastics entered the packaging industry with KW Container, an injection company that molds paint containers from recycled PP. These containers are sold to top paint brands and can be found at nearly all major paint and home improvement stores.
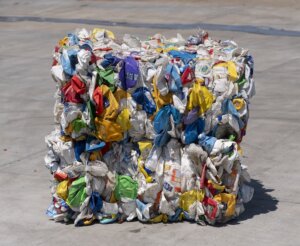
Across its operations, KW Plastics processes approximately 7.5 million containers each day and more than 750 million pounds of plastic annually. In addition to HDPE, the company recycles PP plastic, commonly referred to as #5 resin, which is used in take-out food packaging, ketchup and syrup bottles, and storage containers.
The company purchases bales of sorted and graded plastic from residential collection programs and material recovery facilities throughout North America. Through a proprietary washing, blending and extrusion process, the company reprocesses the recycled materials into recycled resin pellets that are sold to various molders across the country.
“End-use applications include packaging for household and personal care items, as well as automotive, agriculture, recreational and durable goods,” Baker says. “We have strong market demand with brand owners’ commitments to use post-consumer recycled content in more packaging.”
The company operates 19 extruders and has seven custom wash lines with the eighth being installed at this time.
KW Plastics has a dedicated quality lab to test both inbound and outbound material. Each load of recycled resin sold is first certified and matched to customer specification. “We work closely with several of our customers during their design and innovation phases to test, modify and experiment with material choices to ensure the right resin at the right percentage to meet — if not exceed — their expectations,” says Baker. “Several of our customers require rigorous testing, particularly our automotive molders. We also have letters of no objection from the FDA for two of our products.”
Baker notes that KW Plastics sees itself as equal part plastic recycler and post-consumer resin supplier, providing some of the world’s largest brands with high-quality material.
“We add value to material that otherwise costs money to bury in a landfill,” says Baker.
“Recycling has both economic and environmental rewards, and we consider ourselves a manufacturer that plays a significant role in helping our customers achieve their sustainability goals.”
KW Plastics supplies to several operations within the state of Alabama, including automotive suppliers, plastic pipe manufacturers, irrigation systems and a toy company.
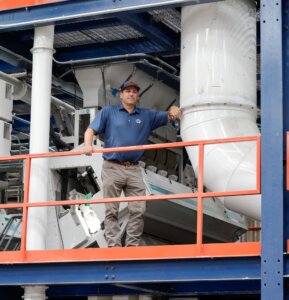
Supply is one of the largest challenges facing the plastics recycling industry. KW Plastics is among many Alabama companies that rely on recycled materials. Other reclaimers operating in the state reprocess paper, polyethylene terephthalate (PET) plastic, steel and aluminum.
“The Southeast has strong end markets for these commodities, and yet we supply more than we source to our own state and regions,” Baker says. “While Alabamians may have recyclable materials in their homes, our state is lacking the investment and infrastructure to get these valuable materials from the garbage can to the recycling bin and to facilities like ours.”
KW Plastics has played an instrumental role in advocating for legislative policies to boost recycling efforts in the state. Baker serves on the Association of Plastic Recyclers (APR) Communications and Public Affairs Committee, the board of the Alabama Recycling Coalition, and as a member of the Recycled Materials Association (ReMA) and the Scrap Recycling Association of Alabama (SRAA).
Across its facilities, the KW companies, not including the trucking business, employ approximately 600 people in roles from welders, electricians and fork-lift drivers to extruder operators, maintenance personnel, IT professionals and lab technicians, in addition to its sales and procurement teams.
The company is led by General Manager Scott Saunders and Director of Operations Christopher Campbell.
Saunders has been with KW since 1994, when he joined as director of raw material procurement. He was named GM in 2007 and currently serves on the board of the APR and ReMA.
Campbell has been with the company for 20 years, working in a variety of departments, including shipping and receiving, customer service and sales, and plant management.
The company and its leadership maintain a close connection to the local community. Baker is in her second term as a member of the Troy City Council, currently serving as president pro tempore.
KW Plastics creates a significant economic impact for the city of Troy. “As one of the largest employers in Pike County, the Sanders/KW family of companies has the largest industrial footprint in Pike County, with five locations along or near Henderson Highway, including a rail site,” Baker says.
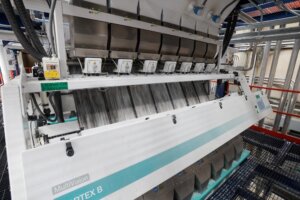
The industrial utility load of the KW companies allows the city of Troy to purchase wholesale electricity and offer lower rates to its residents. This benefit is attractive to new business and supports the expansion of existing businesses, she notes.
KW Plastics also has worked closely with Troy University to offer grant support, share industry connections and support the advancement of plastics recycling. The university received federal funding to establish the Center for Materials and Manufacturing Sciences (CMMS), which provides an opportunity for R&D and the commercialization of polymer science technology.
At the plant, KW Plastics has plans for continued growth with an additional wash line and, possibly, expanding capacity to meet market demand, Baker says.
“Recycling is manufacturing,” she adds. “While it has incredible environmental rewards, there’s also a very strong economic benefit.”
Kathleen Farrell and Stew Milne are freelance contributors to Business Alabama. She is based in Mobile and he in Auburn.
This article appears in the July 2025 issue of Business Alabama.